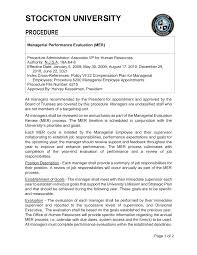
Time boxing is a time management technique used to manage your time effectively and efficiently. This involves setting time limits to allow your team members the ability to complete tasks. After everyone has committed to working within the time limit, you can assign tasks to them and encourage them to be better organized. At the end a time box should be reviewed by the team and they should decide on the next steps. Here are some benefits and challenges of time boxing.
Lessons from David Sherwin's Method
David Sherwin’s timeboxing method is one of the best methods to make sure you get more done with less time. This process starts with assigning very specific tasks to small blocks of time. Each task can have its own time box, and you can also give yourself a bit of wiggle room when you're planning how long it will take.
This technique is great for brainstorming. It can make a complex problem more manageable. It helps to break down a complicated design problem into smaller parts. Then you can allocate time for each task and assess progress.
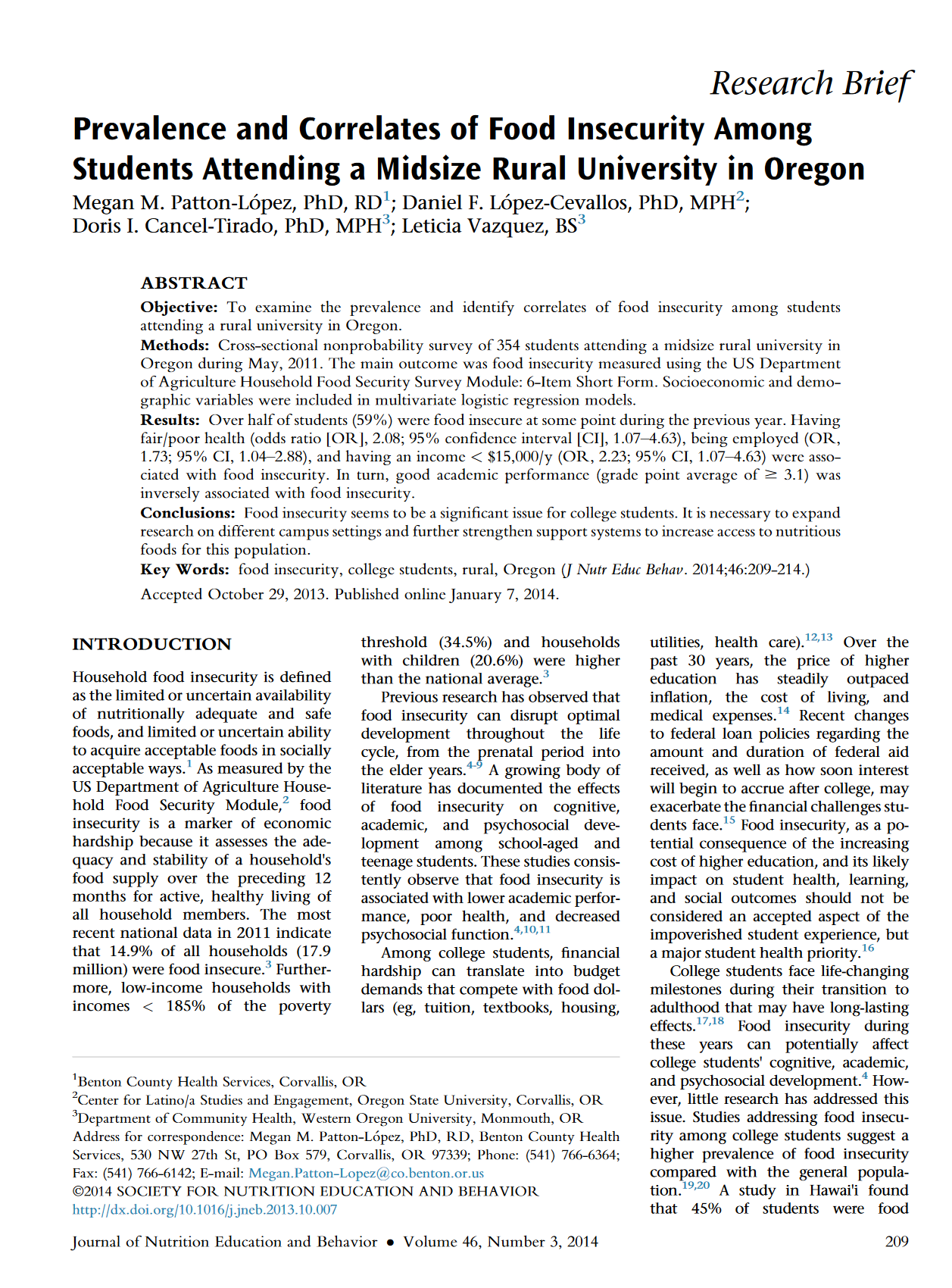
Benefits
Time boxing is a powerful tool which helps you stay focused, and stops procrastination. It can also help to reduce distractions. Turning off notifications and blocking sites can help you stay productive while you work on a project. Time boxing, unlike other methods that can cost money or take up too much time to implement, is simple and free.
Time boxing helps you get more done and helps you feel like you're making progress. This technique can also help with project paralysis. It helps you break a large task down into small, manageable pieces, like creating a marketing plan. It's also possible to place each task on a schedule and track how much time was spent on each.
Challenges
Time boxing can be used to maximize productivity in short time blocks. This technique can be used for multiple tasks such as writing articles. Time boxing is about setting realistic goals. An article writer, for example, should aim to write 1,000 words within a given time frame.
Time boxing is a great method for improving work-life balance, but it has a few challenges. Time boxing works best when everyone is working together and has an idea of what the day will look like. This helps prevent long meetings that can delay deliverables, cause poor quality work, and extend work hours. This helps ensure that all team members keep track of their allocated time. If one team member fails to comply with time boxing, the other team member can redirect them toward a different task.
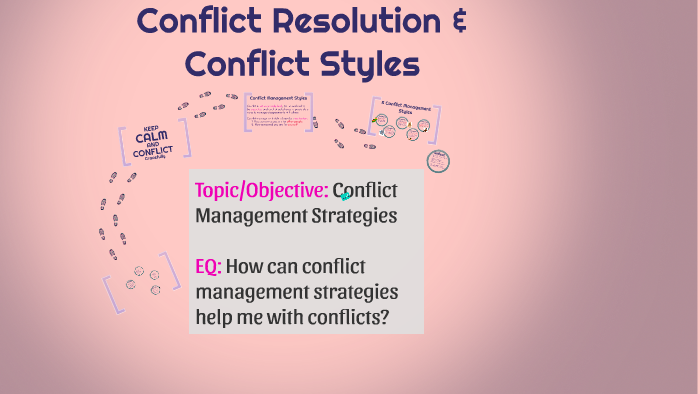
Implementation
Time boxing refers to a time management strategy that helps people stay focused on one task while using time efficiently. It also helps people manage their priorities. If done well, time boxing will help you complete tasks in the most efficient way. It only works if you give your full attention to the task and stay focused within the allotted time. To achieve this, you can use tools that help you set a timer and stay focused.
Before you can implement time boxing, it is important to decide what task you are going to tackle. You should consider its importance, how much time you'll need to complete it, and whether it will create value. This will allow you to determine a realistic start date. Otherwise, you'll end up working longer than you thought.
FAQ
How can a manager improve his/her managerial skills?
You can improve your management skills by practicing them at all times.
Managers must monitor the performance of subordinates constantly.
You must act quickly if you notice that your subordinate isn’t performing to their standards.
You should be able to identify what needs improvement and how to improve things.
What is the difference in Six Sigma and TQM?
The major difference between the two tools for quality management is that six Sigma focuses on eliminating defect while total quality control (TQM), on improving processes and decreasing costs.
Six Sigma is an approach for continuous improvement. It emphasizes the elimination of defects by using statistical methods such as control charts, p-charts, and Pareto analysis.
This method has the goal to reduce variation of product output. This is done by identifying root causes and rectifying them.
Total quality management involves measuring and monitoring all aspects of the organization. It also includes the training of employees to improve performance.
It is often used to increase productivity.
How do you effectively manage employees?
Managing employees effectively means ensuring that they are happy and productive.
This also involves setting clear expectations and monitoring their performance.
To do this successfully, managers need to set clear goals for themselves and for their teams.
They need to communicate clearly with staff members. They should also ensure that they both reward high performers and discipline those who are not performing to their standards.
They must also keep track of the activities of their team. These include:
-
What did you accomplish?
-
How much work was put in?
-
Who did it?
-
Was it done?
-
Why was this done?
This information can help you monitor your performance and to evaluate your results.
Why is it important that companies use project management methods?
Project management techniques are used to ensure that projects run smoothly and meet deadlines.
Because most businesses depend heavily on project work to produce goods or services,
These projects require companies to be efficient and effective managers.
Companies could lose their time, reputation, and money without effective project management.
What is the difference between a project and a program?
A project is temporary while a programme is permanent.
A project usually has a specific goal and deadline.
It is often carried out by a team of people who report back to someone else.
A program will usually have a set number of goals and objectives.
It is usually implemented by a single person.
What are the 4 major functions of management
Management is responsible in planning, organizing and directing people and resources. It includes the development of policies and procedures as well as setting goals.
Management assists an organization in achieving its goals by providing direction, coordination and control, leadership, motivation, supervision and training, as well as evaluation.
Management has four primary functions:
Planning – Planning involves deciding what needs to happen.
Organizing: Organizing refers to deciding how things should work.
Directing – This means to get people to follow directions.
Controlling - Controlling means ensuring that people carry out tasks according to plan.
Statistics
- This field is expected to grow about 7% by 2028, a bit faster than the national average for job growth. (wgu.edu)
- The BLS says that financial services jobs like banking are expected to grow 4% by 2030, about as fast as the national average. (wgu.edu)
- Our program is 100% engineered for your success. (online.uc.edu)
- Your choice in Step 5 may very likely be the same or similar to the alternative you placed at the top of your list at the end of Step 4. (umassd.edu)
- The profession is expected to grow 7% by 2028, a bit faster than the national average. (wgu.edu)
External Links
How To
How do I do the Kaizen Method?
Kaizen means continuous improvement. Kaizen is a Japanese concept that encourages constant improvement by small incremental changes. It's a process where people work together to improve their processes continuously.
Kaizen is one of the most effective methods used in Lean Manufacturing. In this concept, employees who are responsible for the production line must identify problems that exist during the manufacturing process and try to solve them before they become big issues. This will increase the quality and decrease the cost of the products.
Kaizen is the idea that every worker should be aware of what is going on around them. It is important to correct any problems immediately if they are discovered. If someone spots a problem while at work, they should immediately report it to their manager.
Kaizen has a set of basic principles that we all follow. The end product is always our starting point and we work toward the beginning. In order to improve our factory's production, we must first fix the machines producing the final product. We then fix the machines producing components, and the machines producing raw materials. We then fix the workers that work with those machines.
This approach is called 'kaizen' because it focuses on improving everything steps by step. We finish fixing the factory and then go back to the beginning. This continues until we achieve perfection.
To implement kaizen in your business, you need to find out how to measure its effectiveness. There are several ways that you can tell if your kaizen system is working. One of these ways is to check the number of defects found on the finished products. Another method is to determine how much productivity has improved since the implementation of kaizen.
If you want to find out if your kaizen is actually working, ask yourself why. Is it because the law required it or because you want to save money. Did you really think that it would help you achieve success?
Let's say you answered yes or all of these questions. Congratulations! You're now ready to get started with kaizen.