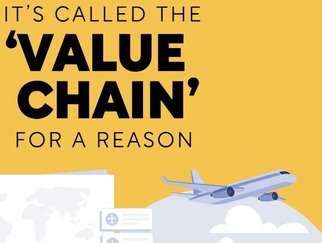
Logistics requires a lot of lead time. It's the time taken between receiving a product and sending it. It is also known as handling lead time or shipping lead time. This time is vital for meeting customer demands and improving business productivity. Lead time is also an important metric in inventory management. It can help you determine the costs associated to various parts of your supply network. Let's discuss the most important aspects of lead time.
Inventory carrying cost
It is important to track lead time as well as inventory carrying costs in a supply chain. Both are indicators that inventory is too high. If they are high, you will need to reduce order frequency or keep stock in motion. Carrying cost, which is related to how much a company spends maintaining inventory, is another important metric to monitor.
The biggest component of inventory carrying costs is the cost to capital. It includes the cost of capital to purchase products, and any interest- or loan fees. This can adversely impact cash flow and lead to the need of additional capital. This cost can be reduced by forecasting the demand for products and making smarter purchasing decisions. They can also negotiate lower purchase prices with suppliers.
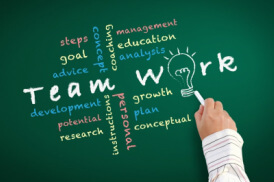
Delivery lead times
A delivery lead-time in a supply network is the time that it takes for customers to place orders and receive their goods. It must be calculated for all products in a supply chain. This time will vary depending on how many parts of the chain the customer purchases, as well as each piece's production capacity. The customer will have accumulated lead time from all players by the time they reach the end of their supply chain. It is important to measure this time accurately.
The first step towards reducing the supply chain's lead times is to identify the crucial parts of the process. If a company has to produce certain quantities of custom water bottles in a short time, they can reduce their lead times by identifying the parts that take longer than one working day. A manufacturer might need to produce a specific number of water bottles within a given time frame. They can program a printing machine that will start the process as they are manufacturing the bottles.
Order lead time
Improving lead times is a critical aspect of managing a supply chain. You can do this by improving your supplier relationships, streamlining your ordering process, and reducing lead times. By placing orders earlier and communicating regularly with suppliers, you can improve order-to delivery. This will improve the customer experience and reduce time to receive orders.
Depending on your business, lead times can vary. Because lead times depend on the product and when you place orders, they can vary. It also depends on which supplier you choose. If you order something Monday morning, it might take one week for it to reach you. It could take up to four days for it to arrive if it's ordered on Friday. You should calculate each part of the supply chain separately to get a more precise lead time.
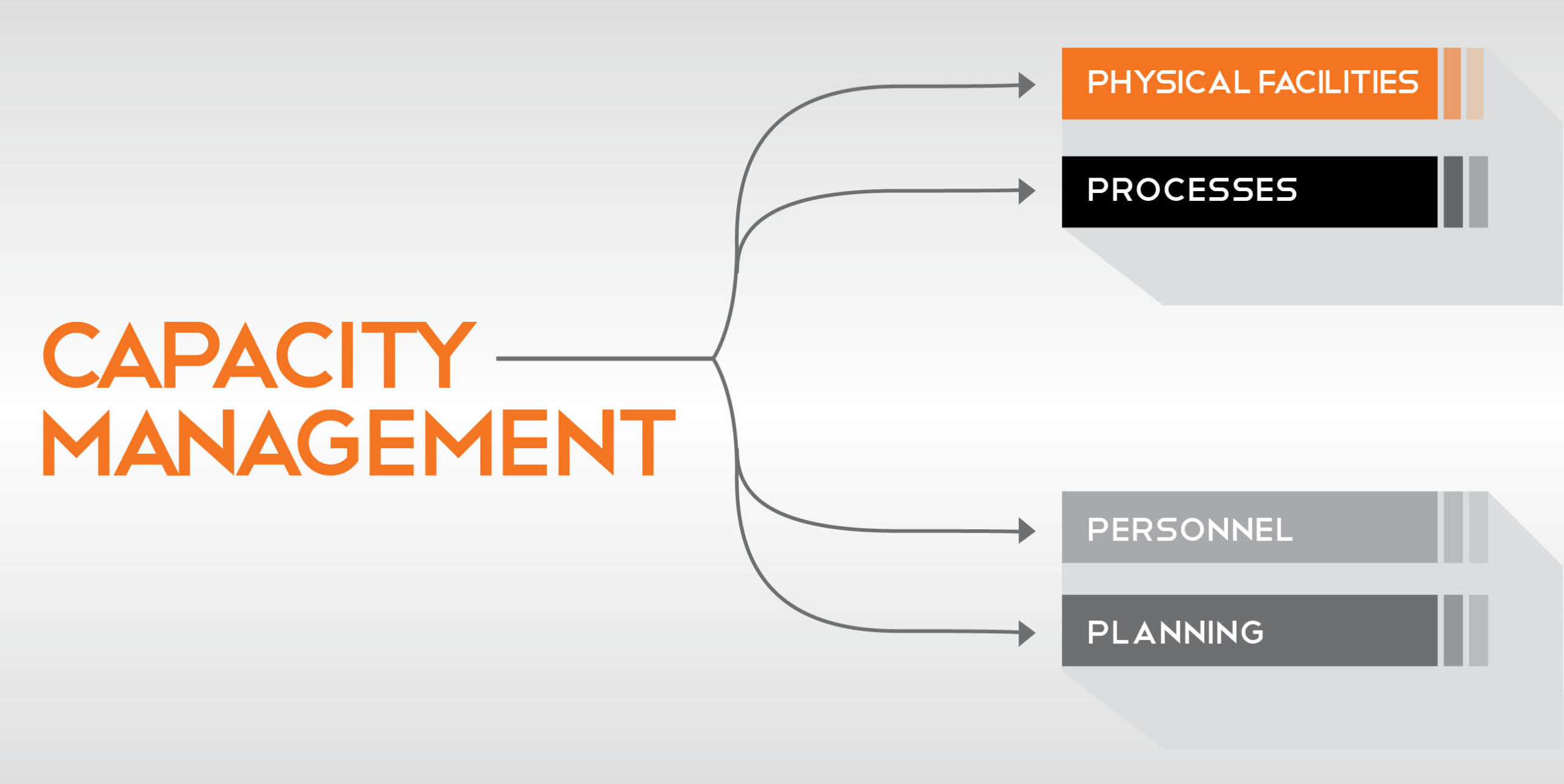
Customer satisfaction
Supply chain elements that are critical to customer satisfaction and delivery times include lead time. When calculating lead time, companies should consider how long it takes to procure and produce items. Lead times can be long, or short, and there are many factors that influence them. Supplier lead times may vary from one day to the next, and the exact amount depends on the supplier.
Businesses must measure their success against key metrics in order increase customer satisfaction. All key metrics can be used to measure order accuracy, delivery speed, replacement time, and other factors. The best supply chain can make a company more satisfied with its customers. Clients can pinpoint problem areas by using analytics that track the progress throughout the supply chain.
FAQ
How can we create a successful company culture?
A positive company culture creates a sense of belonging and respect in its people.
It's based on three main principles:
-
Everybody has something to offer.
-
Fair treatment of people is the goal
-
Individuals and groups can have mutual respect
These values are evident in the way that people act. They will treat others with consideration and courtesy.
They will respect other people's opinions.
They encourage others to express their feelings and ideas.
The company culture promotes collaboration and open communication.
People feel comfortable expressing their opinions freely without fear of reprisal.
They understand that errors will be tolerated as long they are corrected honestly.
Finally, the company culture promotes honesty and integrity.
Everyone knows that they must always tell truth.
Everyone understands there are rules that they must follow.
Nobody expects to be treated differently or given favors.
What is a management tool to help with decision-making?
A decision matrix is an easy but powerful tool to aid managers in making informed decisions. It helps them think systematically about all the options available to them.
A decision matrix can be used to show alternative options as rows or columns. This allows you to easily see how each choice affects others.
The boxes on the left hand side of this matrix represent four possible choices. Each box represents an option. The status quo (the current condition) is shown in the top row, and what would happen if there was no change?
The effect of Option 1 can be seen in the middle column. It would translate into an increase in sales from $2million to $3million.
The next two columns show the effects of choosing Options 2 and 3. These positive changes can increase sales by $1 million or $500,000. However, these also involve negative consequences. Option 2 increases costs by $100 thousand, while Option 3 decreases profits to $200 thousand.
The final column shows results of choosing Option 4. This involves decreasing sales by $1 million.
The best part of using a decision-matrix is that it doesn't require you to know which numbers belong where. The best thing about a decision matrix is that you can simply look at the cells, and immediately know whether one option is better or not.
This is because the matrix has already taken care of the hard work for you. It's as easy as comparing numbers in the appropriate cells.
Here is an example of how a decision matrix might be used in your business.
You want to decide whether or not to invest more money into advertising. You'll be able increase your monthly revenue by $5000 if you do. You will still have to pay $10000 per month in additional expenses.
By looking at the cell just below "Advertising", the net result can be calculated as $15 thousand. Advertising is more valuable than its costs.
What are your main management skills
No matter if they are running a local business or an international one, management skills are vital. They are the ability to manage people and finances, space, money, and other factors.
Management Skills are also needed when you're setting goals and objectives, planning strategies, leading teams, motivating employees, resolving problems, creating policies and procedures, and managing change.
There are so many managerial tasks!
What is the difference between a project and a program?
A program is permanent while a project can be temporary.
A project has usually a specified goal and a time limit.
It is often done in a team that reports to another.
A program is usually defined by a set or goals.
It is often done by one person.
What is Kaizen, exactly?
Kaizen is a Japanese term which means "continuous improvement." This philosophy encourages employees to continually look for ways to improve the work environment.
Kaizen is a belief that everyone should have the ability to do their job well.
Statistics
- The average salary for financial advisors in 2021 is around $60,000 per year, with the top 10% of the profession making more than $111,000 per year. (wgu.edu)
- UpCounsel accepts only the top 5 percent of lawyers on its site. (upcounsel.com)
- Our program is 100% engineered for your success. (online.uc.edu)
- 100% of the courses are offered online, and no campus visits are required — a big time-saver for you. (online.uc.edu)
- Hire the top business lawyers and save up to 60% on legal fees (upcounsel.com)
External Links
How To
What is Lean Manufacturing?
Lean Manufacturing uses structured methods to reduce waste, increase efficiency and reduce waste. They were created by Toyota Motor Corporation in Japan in the 1980s. The aim was to produce better quality products at lower costs. Lean manufacturing emphasizes removing unnecessary steps from the production process. It is composed of five fundamental elements: continuous improvement; pull systems, continuous improvements, just-in–time, kaizen, continuous change, and 5S. The production of only what the customer needs without extra work is called pull systems. Continuous improvement refers to continuously improving existing processes. Just-in–time refers when components or materials are delivered immediately to their intended destination. Kaizen stands for continuous improvement. Kaizen can be described as a process of making small improvements continuously. Five-S stands for sort. It is also the acronym for shine, standardize (standardize), and sustain. These five elements work together to produce the best results.
Lean Production System
The lean production system is based on six key concepts:
-
Flow - focuses on moving information and materials as close to customers as possible.
-
Value stream mapping - Break down each stage in a process into distinct tasks and create an overview of the whole process.
-
Five S's – Sort, Put In Order Shine, Standardize and Sustain
-
Kanban - visual cues such as stickers or colored tape can be used to track inventory.
-
Theory of constraints - identify bottlenecks in the process and eliminate them using lean tools like kanban boards;
-
Just-in time - Get components and materials delivered right at the point of usage;
-
Continuous improvement - make incremental improvements to the process rather than overhauling it all at once.