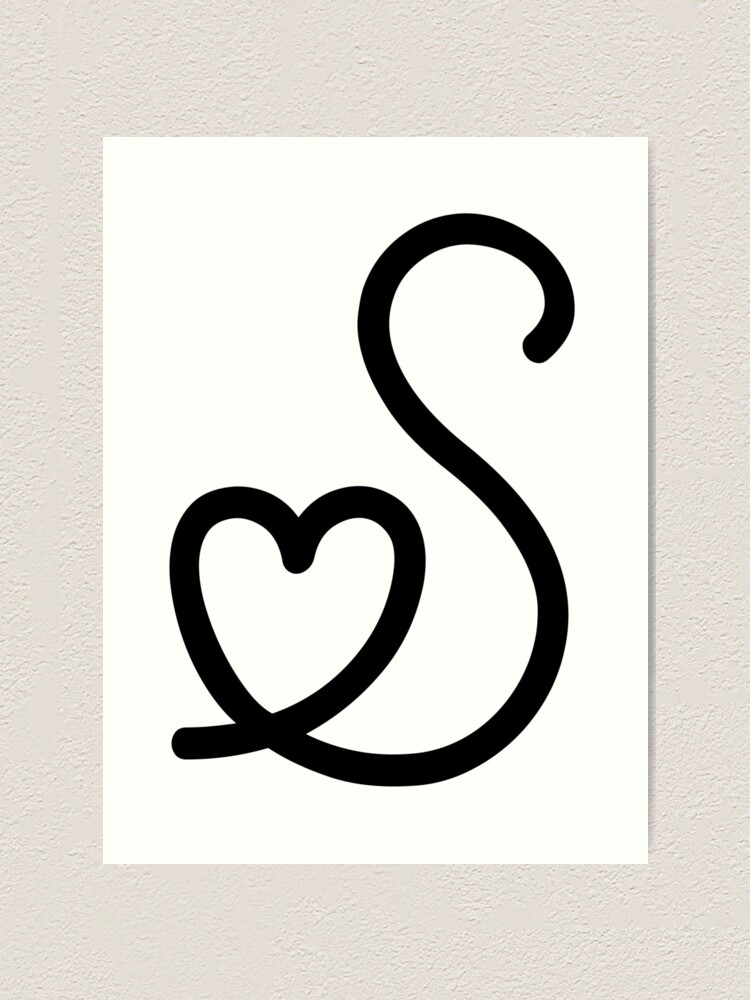
A priority matrix can help you prioritize tasks and organize your activities according to their importance and urgency. The first step in creating a priorities matrix is creating a list of tasks that need to be prioritized. Write down every item and then map them. You can create separate lists for personal and work items if necessary. You will be able to see how the various tasks are interconnected.
A priority matrix is a way to organize your tasks based on importance and urgency.
A priority matrix helps you to plan your time and prioritize the most important tasks. You can even model your priorities numerically, using a simple 1-10 scale. Once you've identified your priorities you can break down your workload into distinct quadrants according importance and urgency. You can delegate the less urgent items to others and plan your daily activities accordingly.
The priority matrix is a great organizational tool that can save you both time and money. It can be used for all kinds of work and can be customized to fit your business or team's needs. This system is used by many businesses to organize tasks based their importance or urgency. It's also useful in project management and prioritization. This will allow you to identify which tasks are essential for your goals.
Todoist
Priorities are essential for managing your time. Todoist makes it easy to prioritize tasks. It lets you organize tasks by priority levels and labels. Each task can be given a unique label. You can also assign different priority levels to each. Todoist lets you search for labels and organize tasks by priority level.
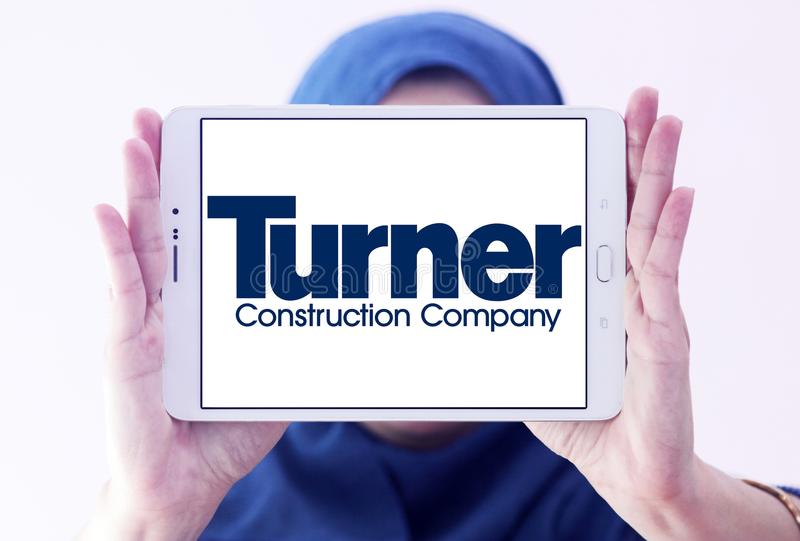
Todoist's flexibility makes it great for team and product management. Using this system for managing your workload will help you get more done. It organizes and schedules your work day. To help you keep track of your tasks, the software uses the Getting Things Done approach. You also have the option to delegate tasks, and move them between inboxes.
Eisenhower matrix
The Eisenhower priority matrix helps you prioritize your time and identify what is most important. While some tasks might require immediate attention, others may not be as urgent but require thoughtful planning. These tasks can be assigned to less-important or urgent quadrants so that they are available for future consideration. The Eisenhower matrix is an excellent tool for simplifying your to-do-list.
The Eisenhower priorities grid can be used to help prioritize tasks and reach long-term objectives. This matrix helps you decide which tasks need to be completed immediately and which should be delayed. The idea is to prioritize the most important tasks first.
PERT matrix
The PERT matrix is one of the tools that project managers use to plan and execute their projects. It's a network made up of boxes that are numbered and represent different events during the project. These boxes are either rectangular or circular, and are connected by labels. Each box holds different activities and tasks that must be completed. Each box contains an icon that indicates a specific task, and the numbers indicate the time each task should take. The team is responsible to follow the sequence in order to complete all activities.
This chart helps project managers to plan projects and ensure that they will meet deadlines. The PERT matrix helps to keep projects on schedule by defining task dependencies. They also use it to visualize their project timeline.
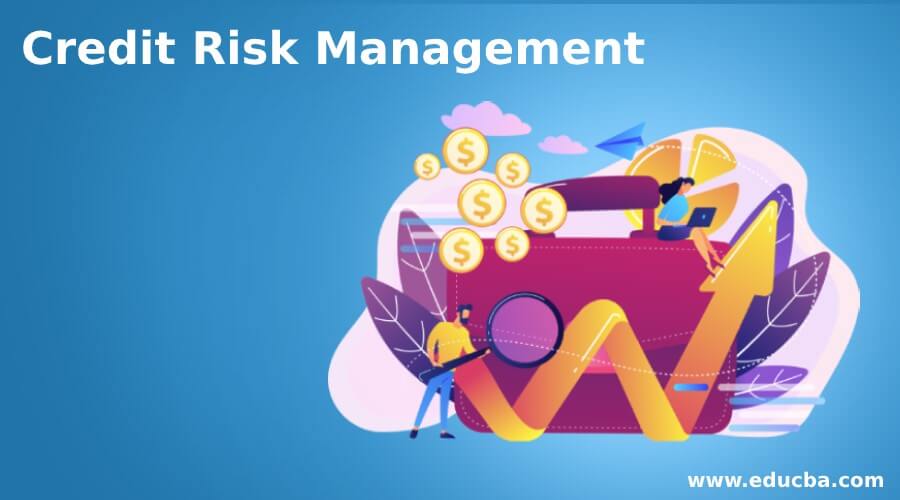
Idea prioritization matrix
Prioritizing ideas can be a crucial step in the innovation cycle. The idea prioritization matrix is a tool that helps teams prioritize ideas based on their feasibility, impact, and importance. The matrix also helps teams compare the merits of different ideas. For a priority matrix, it is best to work with a multidisciplinary group.
A matrix that prioritizes ideas is a tool to help rank wish-list items within larger projects. Your team might have many ideas, from multiple departments or stakeholders, when you're designing a new website. The matrix allows you to visualise the top ideas most likely to be implemented in the development process.
FAQ
How do you effectively manage employees?
Effectively managing employees requires that you ensure their happiness and productivity.
This includes setting clear expectations for their behavior and tracking their performance.
To do this successfully, managers need to set clear goals for themselves and for their teams.
They need to communicate clearly and openly with staff members. They need to communicate clearly with their staff.
They will also need to keep records about their team's activities. These include:
-
What did you accomplish?
-
How much work were you able to accomplish?
-
Who did it?
-
What was the moment it was completed?
-
Why?
This information can be used for monitoring performance and evaluating results.
What is TQM exactly?
When manufacturing companies realized that price was not enough to compete, the industrial revolution brought about the quality movement. They had to improve efficiency and quality if they were to remain competitive.
Management realized the need to improve and created Total Quality Management, which focused on improving all aspects within an organization's performance. It involved continuous improvement, employee participation, and customer satisfaction.
It seems so difficult sometimes to make sound business decisions.
Businesses are complex systems, and they have many moving parts. It is difficult for people in charge of businesses to manage multiple priorities simultaneously and also deal with uncertainty.
Understanding how these factors impact the whole system is key to making informed decisions.
It is important to consider the functions and reasons for each part of the system. Next, consider how each piece interacts with the others.
Ask yourself if there are hidden assumptions that have influenced your behavior. If you don't have any, it may be time to revisit them.
If you're still stuck after all this, try asking someone else for help. You might find their perspective is different from yours and they may have insight that can help you find the solution.
Statistics
- Our program is 100% engineered for your success. (online.uc.edu)
- Your choice in Step 5 may very likely be the same or similar to the alternative you placed at the top of your list at the end of Step 4. (umassd.edu)
- UpCounsel accepts only the top 5 percent of lawyers on its site. (upcounsel.com)
- The average salary for financial advisors in 2021 is around $60,000 per year, with the top 10% of the profession making more than $111,000 per year. (wgu.edu)
- 100% of the courses are offered online, and no campus visits are required — a big time-saver for you. (online.uc.edu)
External Links
How To
How is Lean Manufacturing done?
Lean Manufacturing uses structured methods to reduce waste, increase efficiency and reduce waste. These processes were created by Toyota Motor Corporation, Japan in the 1980s. It was designed to produce high-quality products at lower prices while maintaining their quality. Lean manufacturing eliminates unnecessary steps and activities from a production process. It includes five main elements: pull systems (continuous improvement), continuous improvement (just-in-time), kaizen (5S), and continuous change (continuous changes). It is a system that produces only the product the customer requests without additional work. Continuous improvement involves constantly improving upon existing processes. Just-in-time refers to when components and materials are delivered directly to the point where they are needed. Kaizen means continuous improvement. Kaizen involves making small changes and improving continuously. Five-S stands for sort. It is also the acronym for shine, standardize (standardize), and sustain. These five elements work together to produce the best results.
Lean Production System
Six key concepts are the basis of lean production:
-
Flow - focuses on moving information and materials as close to customers as possible.
-
Value stream mapping- This allows you to break down each step of a process and create a flowchart detailing the entire process.
-
Five S's: Sort, Shine Standardize, Sustain, Set In Order, Shine and Shine
-
Kanban - use visual signals such as colored tape, stickers, or other visual cues to keep track of inventory;
-
Theory of constraints: Identify bottlenecks and use lean tools such as kanban boards to eliminate them.
-
Just-in-time - deliver components and materials directly to the point of use;
-
Continuous improvement - Make incremental improvements rather than overhauling the entire process.