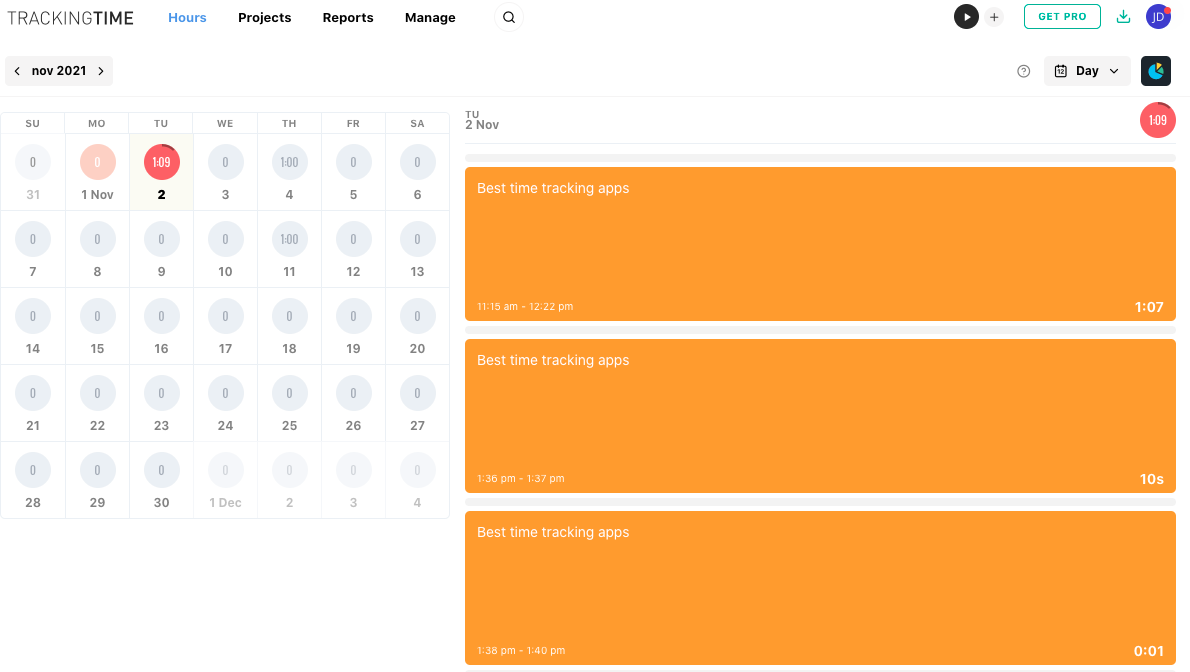
Crisis managers require a variety of skills. It is possible to recognize a crisis and intervene before it becomes critical. In a slow-moving crisis, the effects may not be apparent until later. Leaders who are successful practice early recognition. They stay on top of current events in the world to help them manage their crisis. A skilled crisis manager can help a company cope with a crisis and ensure the continuity of normal operations.
Priorities for crisis managers
Priorities for crisis managers must be clearly and precisely defined. It is important that the team includes people who can be calm and make quick decisions. It should also contain detail-oriented and process-oriented members. A clear chain is necessary to ensure that all members of the team are in line with one another. Also, the team should be trained properly to accomplish its assigned tasks. In the event of a crisis, it is important to restructure the team according to the specific needs of the crisis.
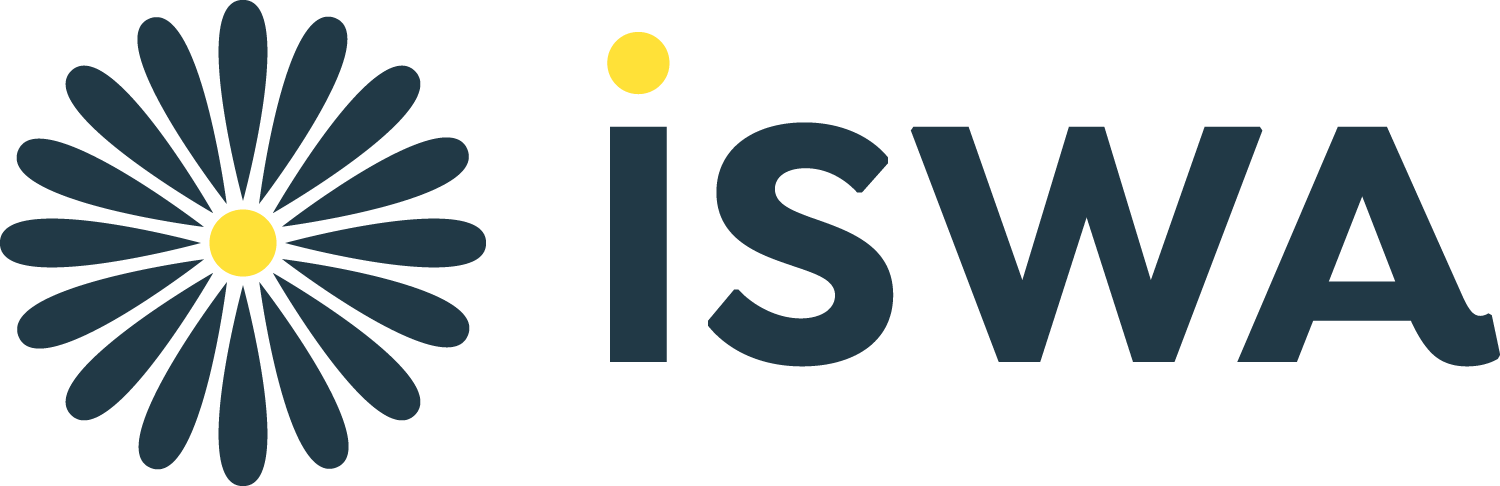
Characteristics for crisis management specialists
You need to have both the skills and experience necessary to be a competent crisis management specialist. Professionals who work in crisis management need to be skilled, experienced, and well-informed. He or she must also have excellent active listening skills. This type of person should be able to handle chaos and stress while remaining calm and focused. They should also be able work well with people from different departments and different roles.
Crisis managers may use certain techniques
To manage a critical event, crisis managers have many options. The art of crisis management requires planning and preparation. The top crisis managers use techniques that are based on resilience. It is the ability of a person to quickly recover from a difficult situation or the vulnerability to an unexpected event. High-performing managers have sharp memory and are able make quick decisions. This allows them to react more quickly and accurately. They embrace vulnerability which allows them prepare for any crisis ahead of it.
The impact of a crisis on an organisation
The Impact of Crisis Upon an Organization examines the damage that a business can suffer during a crisis, and how to avoid or mitigate it. This book examines the factors that affect the value of an organization and the impact that a crisis can have on its viability and reputation. In this digital age, all commercial organizations operate in a challenging environment. Trust is low, and the expectations for good governance are high. Communication between companies is difficult between stakeholders and companies. Traditional target audiences have been broken up into social networks, so issues can be resolved quickly.
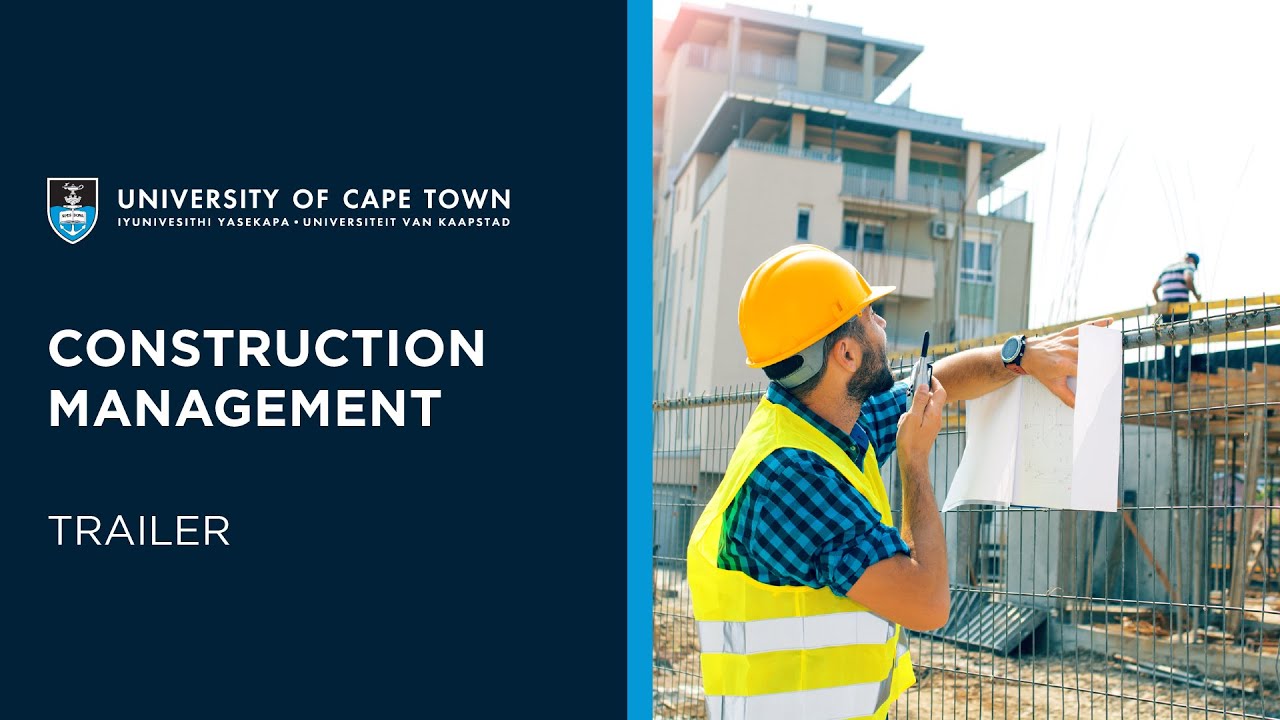
Management skills are required by crisis managers
Communication is an important skill for any crisis manager. These skills are critical to the management of any crisis, no matter how large or small. To resolve the crisis as quickly as possible, they will need to communicate clearly and effectively. They must be calm and able to make quick decisions and delegate. Combining these skills will make crisis managers far more likely achieve a positive outcome.
FAQ
Why is it important for companies to use project management techniques?
To ensure projects run smoothly and meet deadlines, project management techniques are employed.
This is because many businesses depend heavily upon project work to produce products and services.
These projects must be managed efficiently and effectively by companies.
Companies may lose their reputation, time and money if they do not have effective project management.
What are management concepts, you ask?
Management Concepts are the management principles and practices that managers use in managing people and resources. They cover topics such as job descriptions and performance evaluations, human resource policies, training programs, employee motivation, compens systems, organizational structure, among others.
What is the best way to motivate your employees as a manager?
Motivation refers to the desire or need to succeed.
Enjoyable activities can motivate you.
You can also feel motivated by making a positive contribution to the success in the organization.
For example, if you want to become a doctor, you'll probably find it more motivating to see patients than to study medicine books all day.
A different type of motivation comes directly from the inside.
One example is a strong sense that you are responsible for helping others.
You may even find it enjoyable to work hard.
If you don’t feel motivated, find out why.
Next, think of ways you can improve your motivation.
Statistics
- The BLS says that financial services jobs like banking are expected to grow 4% by 2030, about as fast as the national average. (wgu.edu)
- 100% of the courses are offered online, and no campus visits are required — a big time-saver for you. (online.uc.edu)
- UpCounsel accepts only the top 5 percent of lawyers on its site. (upcounsel.com)
- Hire the top business lawyers and save up to 60% on legal fees (upcounsel.com)
- The average salary for financial advisors in 2021 is around $60,000 per year, with the top 10% of the profession making more than $111,000 per year. (wgu.edu)
External Links
How To
What is Lean Manufacturing?
Lean Manufacturing processes are used to reduce waste and improve efficiency through structured methods. They were developed in Japan by Toyota Motor Corporation (in the 1980s). The goal was to produce quality products at lower cost. Lean manufacturing seeks to eliminate unnecessary steps and activities in the production process. It has five components: continuous improvement and pull systems; just-in time; continuous change; and kaizen (continuous innovation). Pull systems involve producing only what the customer wants without any extra work. Continuous improvement is the continuous improvement of existing processes. Just-in time refers to components and materials being delivered right at the place they are needed. Kaizen means continuous improvement. Kaizen involves making small changes and improving continuously. Last but not least, 5S is for sort. These five elements work together to produce the best results.
Lean Production System
Six key concepts make up the lean manufacturing system.
-
Flow is about moving material and information as near as customers can.
-
Value stream mapping- This allows you to break down each step of a process and create a flowchart detailing the entire process.
-
Five S's: Sort, Shine Standardize, Sustain, Set In Order, Shine and Shine
-
Kanban: Use visual signals such stickers, colored tape, or any other visual cues, to keep track your inventory.
-
Theory of constraints: Identify bottlenecks and use lean tools such as kanban boards to eliminate them.
-
Just-in-time - deliver components and materials directly to the point of use;
-
Continuous improvement - Make incremental improvements rather than overhauling the entire process.