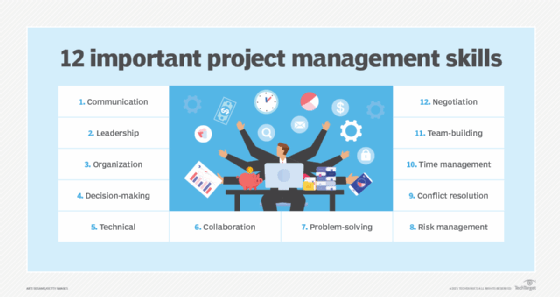
Proper waste management is essential when managing waste from chemical processes or manufacturing facilities. To avoid the formation of harmful fumes and aerosols, incompatible substances should be stored separately in secondary containment bins. Incompatible chemicals should not mixed with other chemicals as they can cause fires and explosions.
Hazards
To prevent environmental and health hazards, chemicals must be properly disposed. Proper disposal means identifying the chemical waste streams that need to be disposed. This is usually done at the conclusion of an experiment. In some cases, hazardous and normal wastes may be mixed together to save money. This is not an option.
You should always check the MSDS (material safety data sheets) for hazardous chemicals before you store them. These sheets are available online and can be obtained directly from the manufacturer. These documents contain information on the chemical's hazards, such as its composition and quantity. You will also find recommended emergency procedures like how to handle a leak.
Regulations
Chemical waste management rules govern the disposal of chemical waste in all workplaces, from laboratories to manufacturing plants. Most chemical wastes are generated in laboratories, but there are other types of waste that are not laboratory-related. These include contaminated soils or building materials. Expired chemicals are also subject to disposal rules.
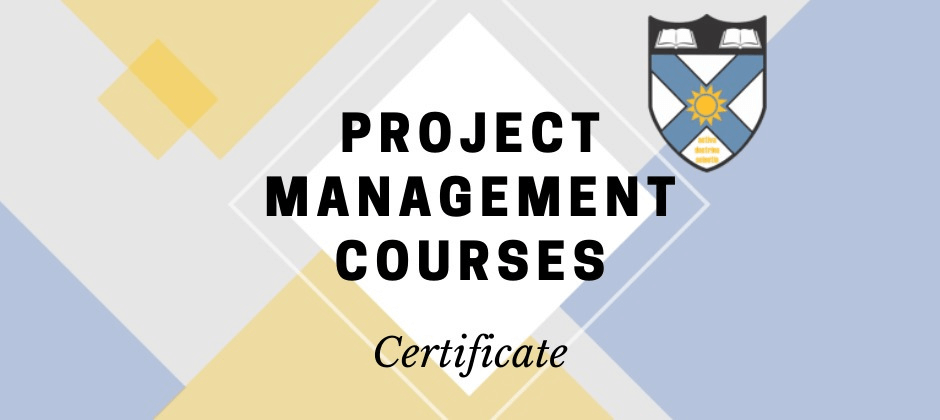
Hazardous waste handling is an important part of safety protocols. Employees must ensure that hazardous wastes are properly handled. This is done to reduce exposure and potential environmental contamination. Two University programs have been created to support employees in complying and meeting the regulations.
Collection
The Chemical Collection request form is the first step of the collection process. This form must be filled out for each waste container. Multiple containers of the chemical waste may be combined into one request. The form can be submitted online. After submitting your request online, you'll receive a CCR Number and Dangerous Waste Label for your waste container. Once you have the information, you can print the label and transfer it to your waste container's label.
Chemical waste can be any substance or mixture of chemicals that is no longer used. These materials may be liquid, gaseous, or solid. It is important to collect chemical waste in order to avoid being charged with pollution.
Storage
It is vital to ensure proper storage of chemical waste to avoid contamination. To do this, it is important that wastes are separated according to their hazard classification. The wastes should be stored in compatible containers. For example, hydrofluoric Acid-containing chemicals should not go in glass or metal containers. For liquids-containing wastes, containers should be designed for liquids. Small containers that can hold large amounts of liquids should be moved to larger containers.
In addition, containers should be tightly sealed. All containers must be sealed securely. Glassware contaminated with lead must be stored in a puncture-proof container. Also, the containers should be marked hazardous waste.
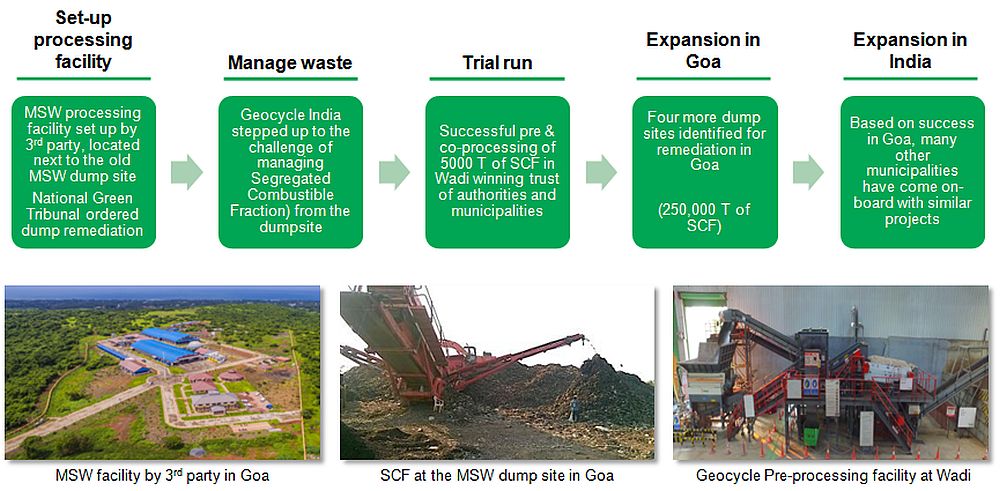
Disposal
Knowing the correct disposal procedure is essential if your company produces hazardous materials. The Texas Commission on Environmental Quality is responsible for regulating hazardous wastes. If improperly disposed of, you could face substantial fines as well legal action. This type waste should be properly managed by a hazardous waste management company.
Chemical waste refers to the disposal of chemicals that are no longer in use. These wastes come in many forms. Some of these wastes are hazardous while others are safe. Chemical waste can either be hazardous for the entire household or just one. For a chemical to be considered hazardous, it must demonstrate four characteristics. They could be radioactive or toxic and flammable. For safe disposal, some chemicals should be kept in containers.
FAQ
What are some common management mistakes?
Managers sometimes make their own job harder than necessary.
They may not delegate enough responsibilities to staff and fail to give them adequate support.
Managers often lack the communication skills necessary to motivate and guide their teams.
Managers set unrealistic expectations and make it difficult for their team.
Managers may choose to solve every problem all by themselves, instead of delegating to others.
What does "project management" mean?
It refers to the management of activities related to a project.
Our services include the definition of the scope, identifying requirements, preparing a budget, organizing project teams, scheduling work, monitoring progress and evaluating the results before closing the project.
What are the three main management styles you can use?
These are the three most common management styles: participative (authoritarian), laissez-faire (leavez-faire), and authoritarian. Each style has strengths and flaws. Which style do you prefer? Why?
Autoritarian - The leader sets direction and expects everyone else to follow it. This style works best if the organization is large and stable.
Laissez-faire - The leader allows each individual to decide for him/herself. This style works best when the organization is small and dynamic.
Participative – Leaders are open to suggestions and ideas from everyone. This style is most effective in smaller organizations, where everyone feels valued.
What does Six Sigma mean?
Six Sigma uses statistical analysis to find problems, measure them, analyze root causes, correct problems, and learn from experience.
The first step in solving a problem is to identify it.
Next, data are collected and analyzed in order to identify patterns and trends.
Next, corrective steps are taken to fix the problem.
Finally, data will be reanalyzed to determine if there is an issue.
This continues until you solve the problem.
How does a manager develop his/her management skills?
You can improve your management skills by practicing them at all times.
Managers should monitor the performance and progress of their subordinates.
You must quickly take action if your subordinate fails to perform.
You should be able pinpoint what needs to improve and how to fix it.
What are the steps in the decision-making process in management?
Managers have to make complex decisions. It involves many elements, including analysis, strategy. planning. implementation. measurement. evaluation. feedback.
It is important to remember that people are human beings, just like you. They make mistakes. There is always room to improve, especially if your first priority is to yourself.
We explain in this video how the Management decision-making process works. We discuss the different types of decisions and why they are important, every manager should know how to navigate them. These topics are covered in this course:
How do we create a company culture that is productive?
A culture of respect and value within a company is key to a productive culture.
It's based on three main principles:
-
Everybody has something to offer.
-
People are treated fairly
-
It is possible to have mutual respect between groups and individuals
These values can be seen in the behavior of people. For example, they will treat others with courtesy and consideration.
They will respect other people's opinions.
They can also be a source of inspiration for others.
In addition, the company culture encourages open communication and collaboration.
People feel free to express their views openly without fear of reprisal.
They know that they will not be judged if they make mistakes, as long as the matter is dealt with honestly.
Finally, the company culture promotes integrity and honesty.
Everyone knows that they must always tell the truth.
Everyone understands there are rules that they must follow.
No one is entitled to any special treatment or favors.
Statistics
- The average salary for financial advisors in 2021 is around $60,000 per year, with the top 10% of the profession making more than $111,000 per year. (wgu.edu)
- Our program is 100% engineered for your success. (online.uc.edu)
- The profession is expected to grow 7% by 2028, a bit faster than the national average. (wgu.edu)
- 100% of the courses are offered online, and no campus visits are required — a big time-saver for you. (online.uc.edu)
- This field is expected to grow about 7% by 2028, a bit faster than the national average for job growth. (wgu.edu)
External Links
How To
What is Lean Manufacturing?
Lean Manufacturing processes are used to reduce waste and improve efficiency through structured methods. These processes were created by Toyota Motor Corporation, Japan in the 1980s. The aim was to produce better quality products at lower costs. Lean manufacturing focuses on eliminating unnecessary steps and activities from the production process. It includes five main elements: pull systems (continuous improvement), continuous improvement (just-in-time), kaizen (5S), and continuous change (continuous changes). Pull systems allow customers to get exactly what they want without having to do extra work. Continuous improvement means continuously improving on existing processes. Just-in–time refers when components or materials are delivered immediately to their intended destination. Kaizen is continuous improvement. This can be achieved by making small, incremental changes every day. Five-S stands for sort. It is also the acronym for shine, standardize (standardize), and sustain. These five elements can be combined to achieve the best possible results.
The Lean Production System
The lean production system is based on six key concepts:
-
Flow - focuses on moving information and materials as close to customers as possible.
-
Value stream mapping - Break down each stage in a process into distinct tasks and create an overview of the whole process.
-
Five S's: Sort, Shine Standardize, Sustain, Set In Order, Shine and Shine
-
Kanban - visual cues such as stickers or colored tape can be used to track inventory.
-
Theory of constraints: identify bottlenecks in your process and eliminate them using lean tools, such as kanban board.
-
Just-in-time delivery - Deliver components and materials right to your point of use.
-
Continuous improvement - Make incremental improvements rather than overhauling the entire process.