
While it can be difficult to accept safety as part of a culture, it can be possible. We will now discuss how to begin the process of creating safety culture. Depending on the organization, there will be different steps. It is important to create a safe environment. Focus groups can help you achieve this. You can also ask stakeholders and employees for their feedback during the focus groups. This will help ensure that the culture is well-designed.
Embracing safety as a culture
Safety culture is about focusing on employees and understanding that everyone has a responsibility for safety. This approach involves extensive training and education. This requires support at all levels. It is important to embrace safety as a part of a company's culture. How can you do that? How can you make a culture of safety valued? Here are some ideas:
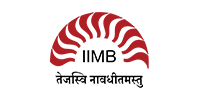
A culture shift is the solution to workplace safety issues. They will take responsibility for the safety process by changing how they think about it. Everyone can be a safety leader if they embrace safety as part of the culture. Safety management systems should teach employees how to coach and lead others in order for this type of culture to be created. Employees must also be committed to safety.
The safety culture of the analytical stage
Effective safety culture encourages employees to report possible safety hazards. Trust is crucial for this. Employees must feel that reporting problems will not cause them to lose their jobs or be punished in any way. It is important that senior management adopts a nonreprisal policy to ensure confidential treatment of all information. Employees must also feel secure that their information will be handled promptly.
The analysis stage of safety culture includes recognizing and analyzing existing problems, and then reporting back the results to the reporting party. These processes include corrective-action programs and root causes analysis. These tools allow you to determine the root causes of injuries and provide safe care. This stage is critical for creating safety culture. It is important to identify safety culture's values and attitudes.
Focus groups help to establish a safety culture
It takes flexibility and a strategy to create a safety culture. Employees should feel secure sharing their concerns and suggestions about workplace safety. To facilitate this, employees should feel comfortable sharing their concerns anonymously through a whistleblowing process. Instead of punishing people for pointing to problems, focus on positive reinforcement. Positive reinforcement fosters trust and morale as well as encourages employee engagement. Safety culture creation is a long-term effort, but the rewards will be well worth it.
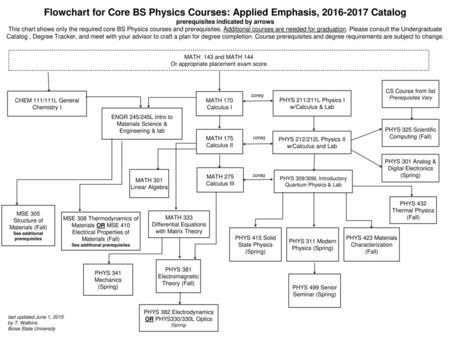
Companies must first recognize their limiting beliefs in order to create a safe culture. Once they have identified these mindsets, they must orchestrate mind-set shifts. They must create trust and a positive atmosphere that encourages employees to report incidents and near misses. This will make it easier for employees to see that reporting near misses and incidents is rewarding. This will ultimately lead to more safety-conscious behavior.
FAQ
How do we build a culture that is successful in our company?
A successful company culture is one that makes people feel valued and respected.
It is founded on three basic principles:
-
Everyone has something valuable to contribute
-
People are treated with respect
-
Individuals and groups can have mutual respect
These values are reflected in the way people behave. They will show consideration and courtesy to others.
They will listen to other people's opinions respectfully.
And they will encourage others to share ideas and feelings.
A company culture encourages collaboration and communication.
People are free to speak out without fear of reprisal.
They know that they will not be judged if they make mistakes, as long as the matter is dealt with honestly.
The company culture encourages honesty and integrity.
Everyone knows that they must always tell truth.
Everyone recognizes that rules and regulations are important to follow.
And no one expects special treatment or favors.
How does a manager learn to manage?
Through demonstrating good management skills at every opportunity
Managers must continuously monitor the performance levels of their subordinates.
If you notice your subordinate isn't performing up to par, you must take action quickly.
You should be able pinpoint what needs to improve and how to fix it.
What is TQM and how can it help you?
When manufacturing companies realized that price was not enough to compete, the industrial revolution brought about the quality movement. To remain competitive, they had to improve quality as well as efficiency.
In response to this need for improvement, management developed Total Quality Management (TQM), which focused on improving all aspects of an organization's performance. It involved continuous improvement, employee participation, and customer satisfaction.
What's the difference between Six Sigma and TQM?
The main difference between these two quality-management tools is that six-sigma concentrates on eliminating defects while total QM (TQM), focuses upon improving processes and reducing expenses.
Six Sigma is an approach for continuous improvement. This method emphasizes eliminating defects using statistical methods such p-charts, control charts, and Pareto analysis.
This method attempts to reduce variations in product output. This is achieved by identifying and addressing the root causes of problems.
Total quality management includes monitoring and measuring all aspects of an organization's performance. It also includes training employees to improve performance.
It is often used as a strategy to increase productivity.
Why is Six Sigma so popular?
Six Sigma is easy to use and can lead to significant improvements. Six Sigma also gives companies a framework for measuring improvement and helps them focus on what is most important.
What kind of people use Six Sigma
Six sigma is a common concept for people who have worked in statistics or operations research. But anyone can benefit from it.
It requires high levels of commitment and leadership skills to be successful.
What are some common management mistakes?
Managers can make their jobs more difficult than necessary.
They may not be able to delegate enough responsibility to staff or provide adequate support.
Additionally, many managers lack communication skills that are necessary to motivate and direct their teams.
Some managers create unrealistic expectations for their teams.
Managers may attempt to solve all problems themselves, rather than delegating it to others.
Statistics
- The average salary for financial advisors in 2021 is around $60,000 per year, with the top 10% of the profession making more than $111,000 per year. (wgu.edu)
- This field is expected to grow about 7% by 2028, a bit faster than the national average for job growth. (wgu.edu)
- As of 2020, personal bankers or tellers make an average of $32,620 per year, according to the BLS. (wgu.edu)
- UpCounsel accepts only the top 5 percent of lawyers on its site. (upcounsel.com)
- Hire the top business lawyers and save up to 60% on legal fees (upcounsel.com)
External Links
How To
How can I obtain my Six Sigma license
Six Sigma is an effective quality management tool that can improve processes and increase productivity. It is a process that helps businesses achieve consistent results in their operations. The name is derived from the Greek word "sigmas", which means "six". Motorola created this process in 1986. Motorola realized they needed to standardize the manufacturing processes to produce products faster and cheaper. There were many people doing the work and they had difficulty achieving consistency. To resolve this issue, they used statistical tools like Pareto analysis and control charts. After this, they would apply these techniques to every part of the operation. This would allow them to make any necessary changes. To get Six Sigma certified, there are three key steps. Finding out if the certification is available for you is the first step. You will need to complete some classes before you can start taking the tests. After you have passed the classes, you can start taking the exams. You'll need to go back and review all the information you received in class. After that, you can take the test. You will be certified if you pass the test. Finally, your certifications will be added to your resume.