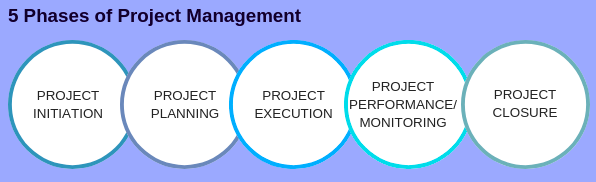
A project manager can be described as a professional who manages projects. They are responsible in planning, procurement, as well as execution. They are also responsible for establishing the project's scope, starting point, and end date. Although these tasks can be difficult, project managers are highly valued by their unique skills and are often highly respected in the workplace.
Establishing a company culture
Understanding how to communicate with an organization's culture is key to creating a company culture as project managers. This will ensure consistency in project managing and allow the new employee to integrate into the company. There are many kinds of corporate cultures.
The pace of a project's completion and its effectiveness can be affected by organizational culture. An organization's culture should be able to differentiate itself from the competition and improve communication among its employees. Culture is often defined as the behaviors and shared values that employees display in the workplace. These shared values may be influenced in part by the company's past and management.
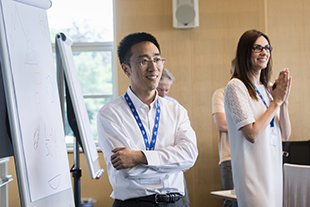
Motivation of team members
Motivation is an important aspect of managing a team. It is possible for tasks to be delayed if members of the team aren't motivated. It is possible to boost morale, and improve performance by following just a few steps. First, learn about the needs of your team members. This knowledge will help you position your teammates for maximum performance.
Once you identify the motivational needs of your team, you can foster a positive environment by creating one. Recognize and reward your team members for their efforts. This will help you become the champion for your team and allow each member to receive a certain amount of recognition. This can go a long way in motivating team members, so don't wait until problems arise. It takes a lot of teamwork and collaboration to motivate team members.
Setting deadlines
Effective time management requires that you set deadlines. There is only so much time in a day. If you don't keep track of it, you might miss important tasks or pile up your to-do lists. Alternatively, you can be lenient by not setting deadlines at all. Here are some ways to set realistic deadlines.
b. Make sure to communicate clearly with your team. All members of your team should be able to communicate clearly about the project's deadlines as well as expectations for success. At the same time, your team members should communicate with you about the resources they need to accomplish the task. Also, you need to be open about any obstacles or problems that might arise throughout the project. This will allow you to stay motivated and achieve the results you desire.
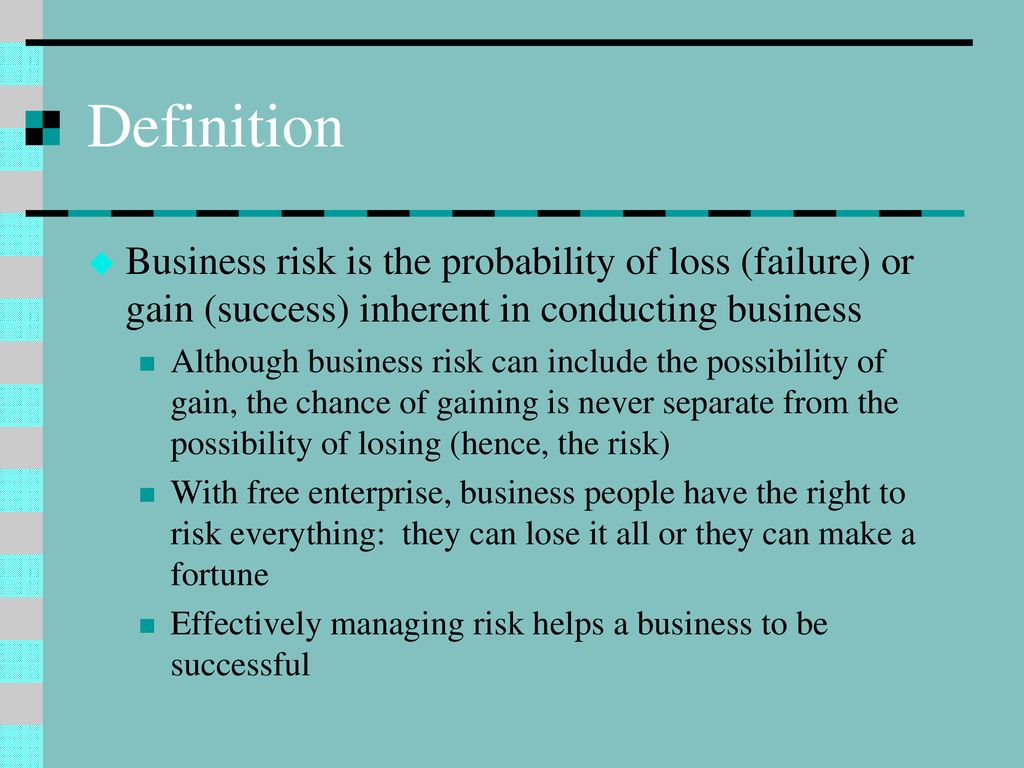
Managing resources
Resource management is an important aspect of project management. This can help you to manage your team's availability and anticipate deadlines. A good resource management strategy can help you gauge your team's ability and prevent burnout. Your business and your team will both benefit from a well-designed resource management plan.
Resource management is crucial to a project's success. It helps you fulfill your commitments and ensures client satisfaction. It also helps you improve team performance, engagement, and productivity. It's crucial to know how budget and resources should be allocated. The best resource management strategies will ensure that billable resources are used efficiently and effectively.
FAQ
Why does it sometimes seem so hard to make good business decisions
Businesses are complex systems, and they have many moving parts. Their leaders must manage multiple priorities, as well as dealing with uncertainty.
Understanding how these factors impact the whole system is key to making informed decisions.
You must first consider what each piece of the system does and why. Next, consider how each piece interacts with the others.
You need to ask yourself if your previous actions have led you to make unfounded assumptions. If they don't, you may want to reconsider them.
Asking for assistance from someone else is a good idea if you are still having trouble. You might find their perspective is different from yours and they may have insight that can help you find the solution.
How do we create a company culture that is productive?
A culture of respect and value within a company is key to a productive culture.
It is based on three principles:
-
Everyone has something to contribute
-
People are treated fairly
-
Individuals and groups can have mutual respect
These values are reflected in the way people behave. They will treat others with kindness and consideration.
They will respect the opinions of others.
They can also be a source of inspiration for others.
In addition, the company culture encourages open communication and collaboration.
People can freely express their opinions without fear or reprisal.
They are aware that mistakes can be accepted if they are treated honestly.
Finally, the company culture encourages honesty as well as integrity.
Everyone knows that they must always tell the truth.
Everyone understands there are rules that they must follow.
And no one expects special treatment or favors.
What role does a manager play in a company?
The role of a manager varies from one industry to another.
A manager generally manages the day to-day operations in a company.
He/she ensures that the company meets its financial obligations and produces goods or services that customers want.
He/she ensures that employees follow the rules and regulations and adhere to quality standards.
He/she is responsible for the development of new products and services, as well as overseeing marketing campaigns.
What is the difference between project and program?
A project is temporary, while a program lasts forever.
A project usually has a specific goal and deadline.
It is often done in a team that reports to another.
A program usually has a set of goals and objectives.
It is often implemented by one person.
What does "project management" mean?
Management is the act of managing activities in order to complete a project.
We help you define the scope of your project, identify the requirements, prepare the budget, organize the team, plan the work, monitor progress and evaluate the results before closing down the project.
How can a manager improve his/her managerial skills?
Through demonstrating good management skills at every opportunity
Managers need to monitor their subordinates' performance.
You must quickly take action if your subordinate fails to perform.
You should be able to identify what needs improvement and how to improve things.
What is the main difference between Six Sigma Six Sigma TQM and Six Sigma Six Sigma?
The key difference between the two quality management tools is that while six-sigma focuses its efforts on eliminating defects, total quality management (TQM), focuses more on improving processes and reducing cost.
Six Sigma is a methodology for continuous improvement. This approach emphasizes eliminating defects through statistical methods like control charts, Pareto analysis, and p-charts.
This method has the goal to reduce variation of product output. This is done by identifying and correcting the root causes of problems.
Total quality management includes monitoring and measuring all aspects of an organization's performance. It also includes the training of employees to improve performance.
It is often used to increase productivity.
Statistics
- Hire the top business lawyers and save up to 60% on legal fees (upcounsel.com)
- The BLS says that financial services jobs like banking are expected to grow 4% by 2030, about as fast as the national average. (wgu.edu)
- The average salary for financial advisors in 2021 is around $60,000 per year, with the top 10% of the profession making more than $111,000 per year. (wgu.edu)
- This field is expected to grow about 7% by 2028, a bit faster than the national average for job growth. (wgu.edu)
- Your choice in Step 5 may very likely be the same or similar to the alternative you placed at the top of your list at the end of Step 4. (umassd.edu)
External Links
How To
What is Lean Manufacturing?
Lean Manufacturing is a method to reduce waste and increase efficiency using structured methods. They were created by Toyota Motor Corporation in Japan in the 1980s. The main goal was to produce products at lower costs while maintaining quality. Lean manufacturing emphasizes removing unnecessary steps from the production process. It consists of five basic elements: pull systems, continuous improvement, just-in-time, kaizen (continuous change), and 5S. It is a system that produces only the product the customer requests without additional work. Continuous improvement refers to continuously improving existing processes. Just-in–time refers when components or materials are delivered immediately to their intended destination. Kaizen means continuous improvement, which is achieved by implementing small changes continuously. Five-S stands for sort. It is also the acronym for shine, standardize (standardize), and sustain. These five elements are combined to give you the best possible results.
The Lean Production System
Six key concepts form the foundation of the lean production system:
-
Flow - focuses on moving information and materials as close to customers as possible.
-
Value stream mapping - break down each stage of a process into discrete tasks and create a flowchart of the entire process;
-
Five S's: Sort, Shine Standardize, Sustain, Set In Order, Shine and Shine
-
Kanban – visual signals like colored tape, stickers or other visual cues are used to keep track inventory.
-
Theory of constraints - identify bottlenecks in the process and eliminate them using lean tools like kanban boards;
-
Just-intime - Order components and materials at your location right on the spot.
-
Continuous improvement: Make incremental improvements to the process instead of overhauling it completely.