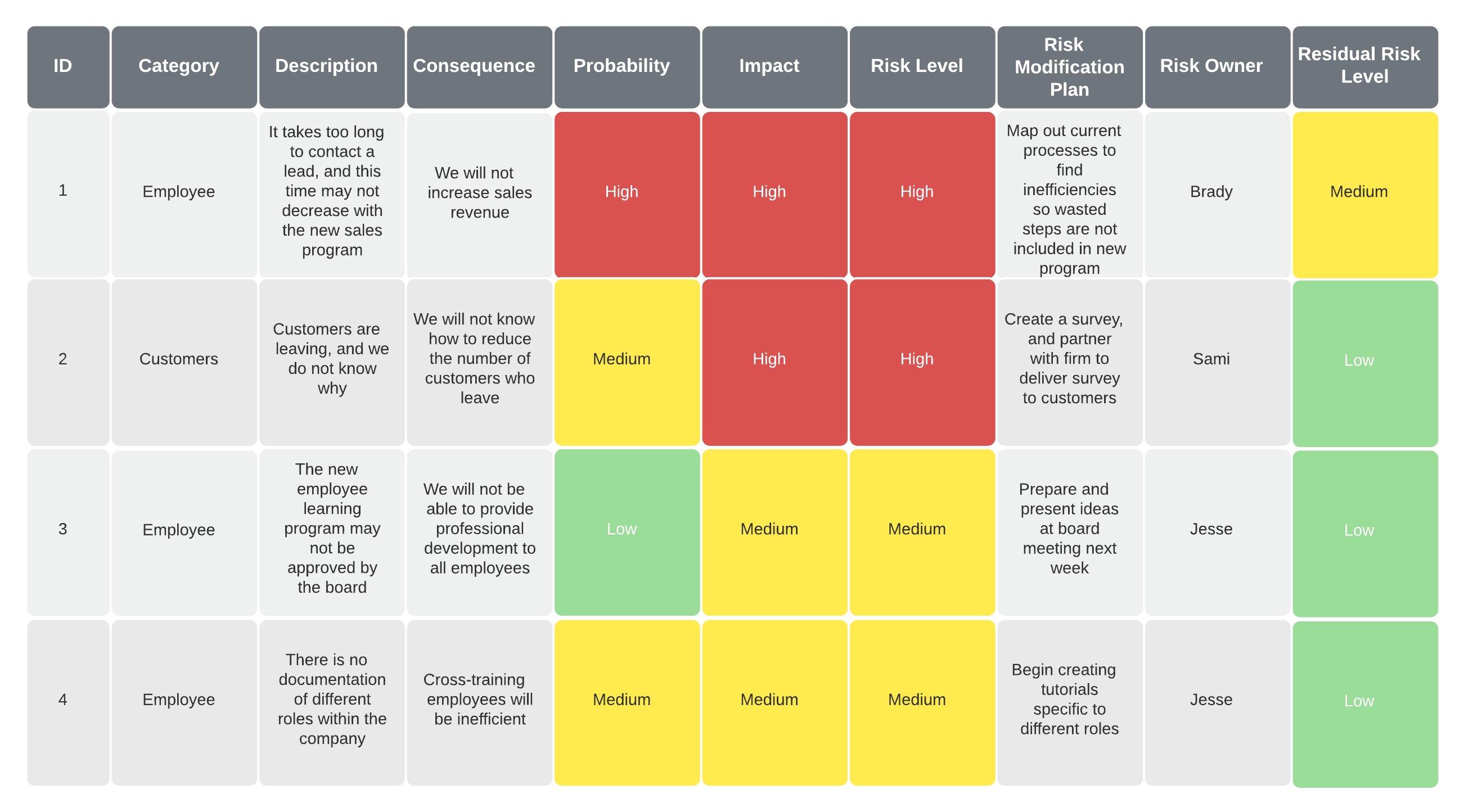
Employees should be involved in the change process. Ask your employees to participate in the change process. The employees should be informed of any important decisions that could affect them. Employees get time to consider and evaluate new ideas. Participation by employees in the change process will make them more open to the possibilities. It's also beneficial for employees to be involved in the planning and implementation. This article will cover the four phases of employee change.
Four phases for employee change
The separation is the first phase of the process. This is a process that takes place in the 0 to three months prior to the employee leaving the company. Either the employee, or the company, can initiate the separation process. The timing of the separation process will vary from company to company. However, most companies require employees not to inform their employers less than two weeks before they plan to leave. The company is better equipped to deal with the situation.
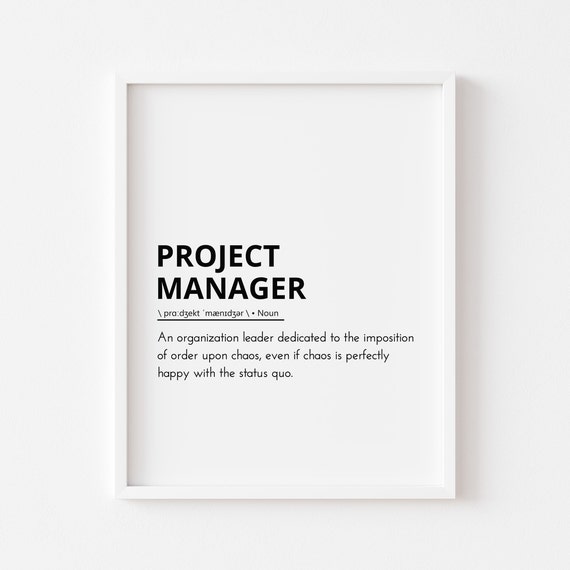
Communication
Communication is key to a successful change management program. Communicating the changes to employees in a way that encourages them to adopt new working methods is crucial. The communication process must be based on understanding the changes and the employees' needs. It should involve regular and consistent communication. It is also important that you communicate effectively with different audiences so that your message reaches everyone.
Empowerment
Technology and team-building activities are great ways to encourage engagement and develop employees. If you make your employees feel appreciated, connected, and valued by their coworkers, it will encourage a more collaborative environment. Additionally, you can establish mentoring circles, idea swaps, or other ways to connect with other departments. Employees feel empowered and are more likely solve problems and contribute positively to the company’s success. How can you encourage your employees to take part?
Communicate upfront
Communication upfront is the key to successful change management. Explain to the employee the change and the implications. To make sure employees are on board with the new direction, they need to be clear about what is happening. Communicate the changes clearly and in a simple way to avoid misunderstandings. To communicate the right message, target different audiences. Communication about new leadership is important, for example, if you're restructuring a department. Communicate with all departments when you're restructuring the company.
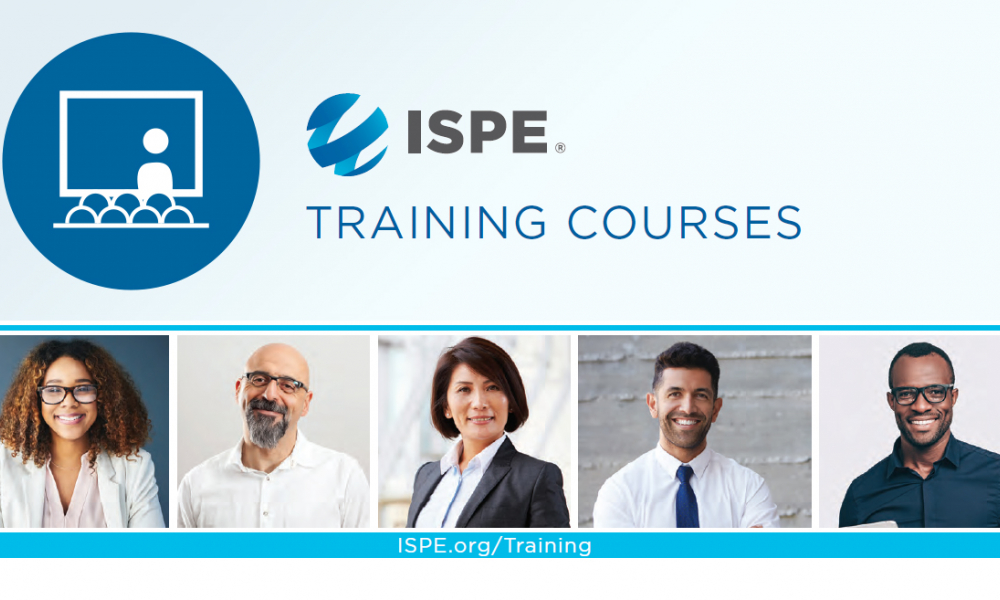
Create a supportive work environment
It is essential to create a supportive workplace environment that allows employees to make changes. This is key to employee satisfaction. It also improves the bottom line. Employees are people, and motivating employees to achieve their goals can help them reach their full potential. Support, on the other hand, goes beyond motivation, and is more about the overall health of the employee. Therefore, it is essential to understand what motivates people and how to best support them.
FAQ
What is Six Sigma?
It is a way to improve quality that places emphasis on customer service and continuous learning. This is an approach to quality improvement that uses statistical techniques to eliminate defects.
Motorola created Six Sigma as part of their efforts to improve manufacturing processes in 1986.
The idea quickly spread in the industry. Many organizations today use six-sigma methods to improve product design and production, delivery and customer service.
What are management concepts, you ask?
Management concepts are the fundamental principles and practices that managers use when managing people and their resources. They cover topics like job descriptions (job descriptions), performance evaluations, training programmes, employee motivation and compensation systems.
Six Sigma is so popular.
Six Sigma is simple to implement and can yield significant results. Six Sigma provides a framework to measure improvements and allows companies to focus on the most important things.
Statistics
- Your choice in Step 5 may very likely be the same or similar to the alternative you placed at the top of your list at the end of Step 4. (umassd.edu)
- The BLS says that financial services jobs like banking are expected to grow 4% by 2030, about as fast as the national average. (wgu.edu)
- Hire the top business lawyers and save up to 60% on legal fees (upcounsel.com)
- UpCounsel accepts only the top 5 percent of lawyers on its site. (upcounsel.com)
- The profession is expected to grow 7% by 2028, a bit faster than the national average. (wgu.edu)
External Links
How To
How do I do the Kaizen Method?
Kaizen means continuous improvement. This Japanese term refers to the Japanese philosophy of continuous improvement that emphasizes incremental improvements and constant improvement. It is a process where people come together to improve their processes.
Kaizen is one the most important methods of Lean Manufacturing. Employees responsible for the production line should identify potential problems in the manufacturing process and work together to resolve them. This increases the quality of products and reduces the cost.
Kaizen is a way to raise awareness about what's happening around you. It is important to correct any problems immediately if they are discovered. If someone spots a problem while at work, they should immediately report it to their manager.
Kaizen has a set of basic principles that we all follow. Start with the end product, and then move to the beginning. To improve our factory, for example, we need to fix the machines that produce the final product. First, we fix machines that produce components. Next, we fix machines that produce raw material. Finally, we repair the workers who are directly involved with these machines.
This is known as "kaizen", because it emphasizes improving each step. After we're done with the factory, it's time to go back and fix the problem.
How to measure kaizen's effectiveness in your business is essential to implement it. There are several ways that you can tell if your kaizen system is working. One way is to examine the amount of defects on the final products. Another way is to check how much productivity has grown since kaizen was implemented.
If you want to find out if your kaizen is actually working, ask yourself why. Is it because the law required it or because you want to save money. Did you really think that it would help you achieve success?
Suppose you answered yes to any of these questions, congratulations! You are ready to start kaizen.