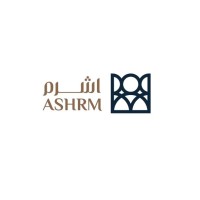
Athena Pro Core a comprehensive plant nutrition program that provides a solid foundation for all stages. This solution is compatible for most dosing devices and provides strong nutrition to plants at all stages. You can manage your application using the mobile app. If you have any questions, you can contact the customer service team.
Athena Pro Core integrates with all dosing platforms
Athena Pro Core is an effective base nutrition supplement. It contains essential microelements as well as nutrients that are essential for plant growth. Its proprietary blend contains small amounts of each element in order to make a uniform and effective mixture for any reservoir. It can be used for mixing stock tank mixtures and is compatible all dosing systems. You can use it with Athena Pro Grow, or Athena Pro Bloom to ensure optimal plant nutrition.
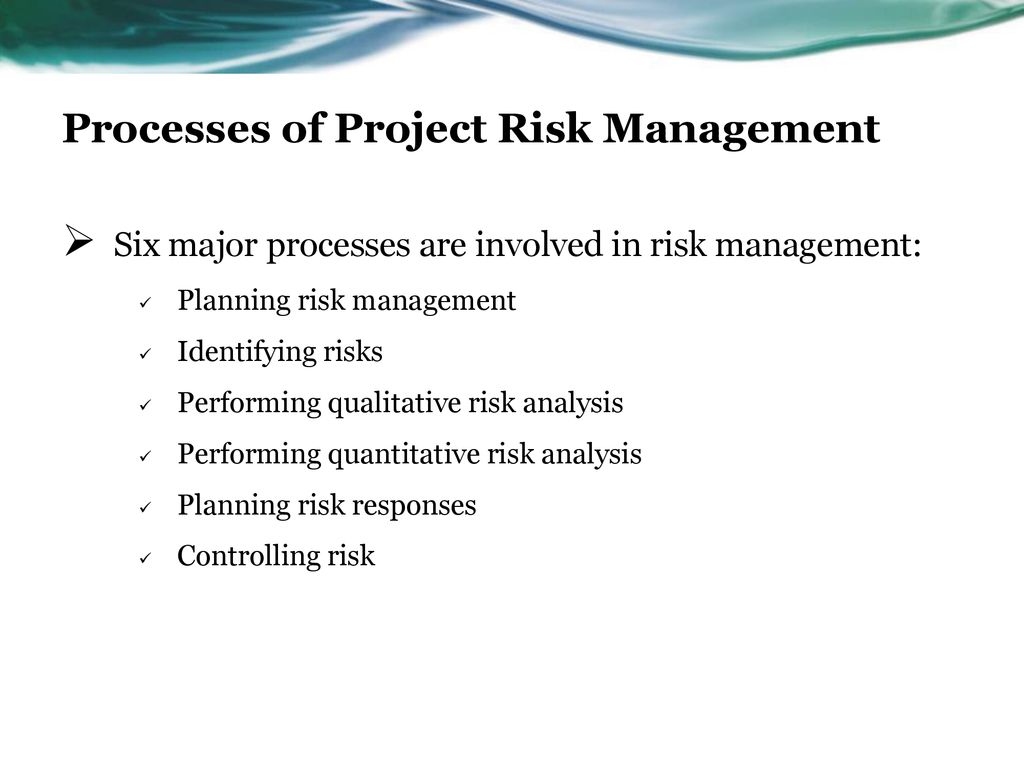
Athena Pro Core provides a strong base nutrition for all stages in plant growth
Athena Pro Core a highly concentrated fertilizer delivers the necessary microelements as well as nutrients to support plant growth. It is ideal for use in stock tanks and is compatible with most dosing systems. Its 100% solubility means it won’t clog irrigation systems and don’t leave sediment behind in reservoirs. Athena Pro Core should not be used alone, but in conjunction with Athena Pro Grow.
Athena Pro Core provides a focus assessment for Ohio's Learning Standards.
2004 saw Ohio legislators pass Senate Bill 2. This created a state Educator Standards Board. It developed the Ohio Learning Standards. To evaluate teachers according to the standards, the bill mandated the creation a Ohio Teacher Evaluation System. The purpose of this legislation is to improve teacher performance. The state of Ohio aims to achieve this goal through a comprehensive evaluation system that considers teacher strengths and weaknesses and supports their growth as educators.
Athena Pro Core, a mobile app, is available
Athena Pro Core provides a strong base nutrition for plant health and microelements for optimal plant growth. It is compatible for most dosing system types and 100% soluble. Therefore, it won't clog irrigation pipes or create sediment in reservoirs. It is best to use it in conjunction with Athena Pro Grow. It comes in both dry and concentrated forms.
Athena Pro Core integrates seamlessly with ERP software
Integrating Athena Pro Core into an ERP program such as QuickBooks is possible through the software's integrated electronic document management. This allows you to manage many documents such as claims, invoices, and other information. It also features a user interface that you can customize to suit your needs. You can view all pending tasks and assign them different employees.
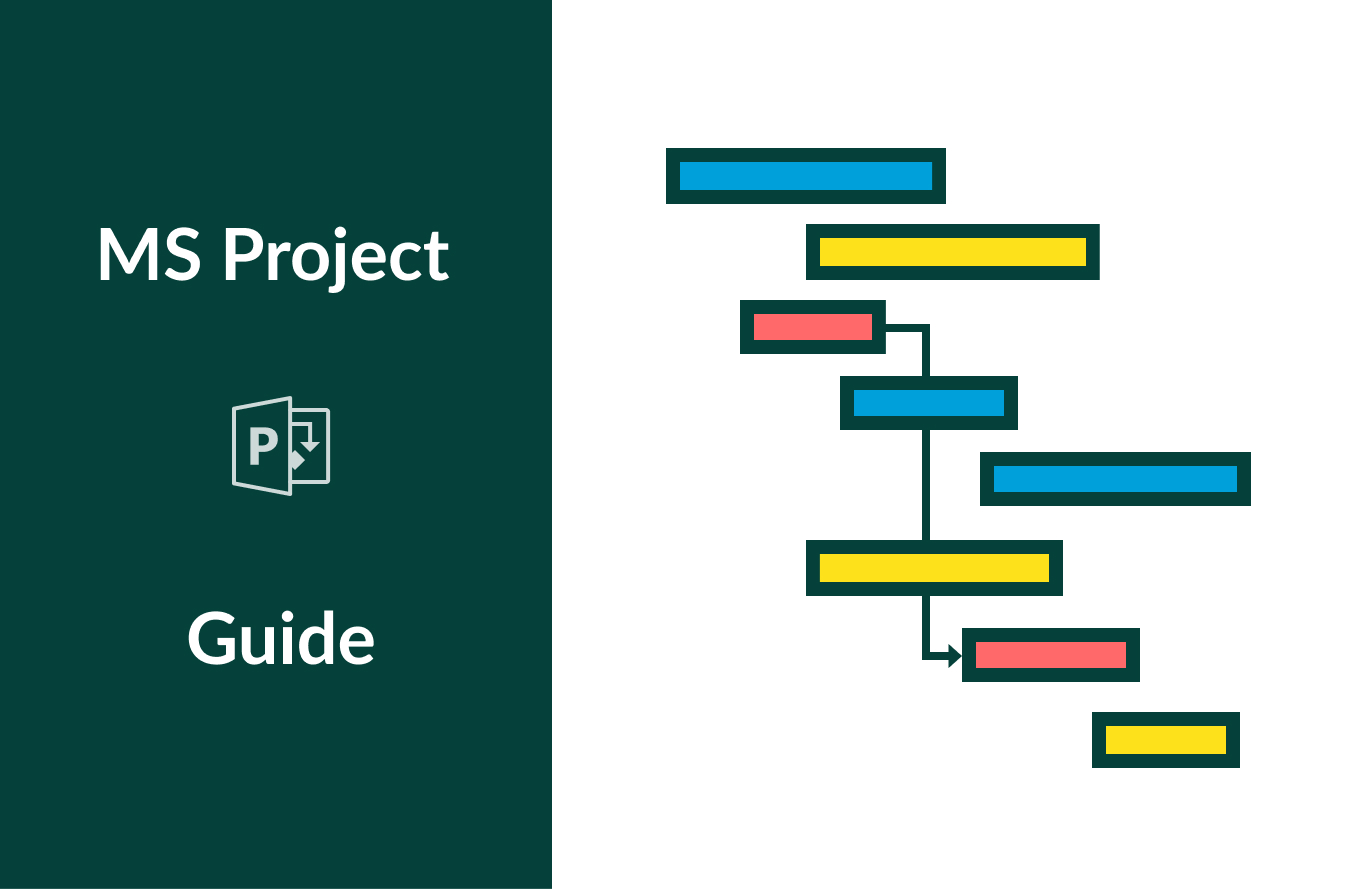
Athena Pro Core is enterprise-grade security
Athena's smart-card platform has been certified and accredited worldwide by the leading security standards bodies. It has been tested rigorously to ensure that it conforms to the security standards of leading US, European and Brazilian organisations. Athena's solutions have been designed to be flexible and cost-effective.
FAQ
How can we create a successful company culture?
A successful company culture is one that makes people feel valued and respected.
It's built on three fundamental principles:
-
Everybody has something of value to share
-
People are treated fairly
-
Individuals and groups can have mutual respect
These values reflect in how people behave. They will show consideration and courtesy to others.
They will listen to other people's opinions respectfully.
They can also be a source of inspiration for others.
A company culture encourages collaboration and communication.
People can freely express their opinions without fear or reprisal.
They know that they will not be judged if they make mistakes, as long as the matter is dealt with honestly.
Finally, the company culture promotes integrity and honesty.
Everyone understands that the truth is always best.
Everyone is aware that rules and regulations apply to them.
Nobody expects to be treated differently or given favors.
What is a basic management tool that can be used for decision-making?
A decision matrix is a simple but powerful tool for helping managers make decisions. It helps them to think strategically about all options.
A decision matrix is a way to organize alternatives into rows and columns. This makes it easy to see how each alternative affects other choices.
In this example, there are four possible options represented by boxes on the left-hand side of the matrix. Each box represents a different option. The top row shows the status quo (the current situation), and the bottom row shows what would happen if nothing was done at all.
The effect of Option 1 can be seen in the middle column. It would increase sales by $2 million to 3 million in this instance.
The results of choosing Option 2 and 3 can be seen in the columns below. These are both positive changes that increase sales by $1million and $500,000. However, these also involve negative consequences. Option 2, for example, increases the cost by $100 000 while Option 3 decreases profits by $200 000.
The final column shows the results for Option 4. This will result in sales falling by $1,000,000
The best part of using a decision-matrix is that it doesn't require you to know which numbers belong where. Simply look at the cells to instantly determine if one choice is better than the other.
The matrix has already done all of the work. It is as simple as comparing the numbers within the relevant cells.
Here's an example showing how you might use a Decision Matrix in your business.
Advertising is a decision that you make. If you do, you'll be able to increase your revenue by $5 thousand per month. However, this will mean that you'll have additional expenses of $10,000.
By looking at the cell just below "Advertising", the net result can be calculated as $15 thousand. Advertising is worth more than its cost.
How does Six Sigma work?
Six Sigma uses statistical analyses to locate problems, measure them, analyze root cause, fix problems and learn from the experience.
The first step in solving a problem is to identify it.
Next, data will be collected and analyzed to determine trends and patterns.
Then corrective actions are taken to solve the problem.
The data are then reanalyzed to see if the problem is solved.
This continues until the problem has been solved.
It can sometimes seem difficult to make business decisions.
Complex systems are often complex and have many moving parts. Their leaders must manage multiple priorities, as well as dealing with uncertainty.
Understanding how these factors impact the whole system is key to making informed decisions.
To do this, you must think carefully about what each part of the system does and why. It's important to also consider how they interact with each other.
You need to ask yourself if your previous actions have led you to make unfounded assumptions. If not, you might want to revisit them.
Asking for assistance from someone else is a good idea if you are still having trouble. They may see things differently from you and have insights that could help you find a solution.
What is the main difference between Six Sigma Six Sigma TQM and Six Sigma Six Sigma?
The key difference between the two quality management tools is that while six-sigma focuses its efforts on eliminating defects, total quality management (TQM), focuses more on improving processes and reducing cost.
Six Sigma stands for continuous improvement. It emphasizes the elimination of defects by using statistical methods such as control charts, p-charts, and Pareto analysis.
This method seeks to decrease variation in product output. This is accomplished through identifying and correcting root causes.
Total quality management involves measuring and monitoring all aspects of the organization. It also includes the training of employees to improve performance.
It is frequently used as an approach to increasing productivity.
Statistics
- UpCounsel accepts only the top 5 percent of lawyers on its site. (upcounsel.com)
- Your choice in Step 5 may very likely be the same or similar to the alternative you placed at the top of your list at the end of Step 4. (umassd.edu)
- 100% of the courses are offered online, and no campus visits are required — a big time-saver for you. (online.uc.edu)
- The average salary for financial advisors in 2021 is around $60,000 per year, with the top 10% of the profession making more than $111,000 per year. (wgu.edu)
- The BLS says that financial services jobs like banking are expected to grow 4% by 2030, about as fast as the national average. (wgu.edu)
External Links
How To
What is Lean Manufacturing?
Lean Manufacturing methods are used to reduce waste through structured processes. They were created by Toyota Motor Corporation in Japan in the 1980s. The aim was to produce better quality products at lower costs. Lean manufacturing eliminates unnecessary steps and activities from a production process. It consists of five basic elements: pull systems, continuous improvement, just-in-time, kaizen (continuous change), and 5S. It is a system that produces only the product the customer requests without additional work. Continuous improvement refers to continuously improving existing processes. Just-intime refers the time components and materials arrive at the exact place where they are needed. Kaizen means continuous improvement. Kaizen involves making small changes and improving continuously. Five-S stands for sort. It is also the acronym for shine, standardize (standardize), and sustain. These five elements can be combined to achieve the best possible results.
Lean Production System
Six key concepts are the basis of lean production:
-
Flow - focus on moving material and information as close to customers as possible;
-
Value stream mapping: This is a way to break down each stage into separate tasks and create a flowchart for the entire process.
-
Five S's: Sort, Shine Standardize, Sustain, Set In Order, Shine and Shine
-
Kanban is a visual system that uses visual cues like stickers, colored tape or stickers to keep track and monitor inventory.
-
Theory of constraints - identify bottlenecks in the process and eliminate them using lean tools like kanban boards;
-
Just-in time - Get components and materials delivered right at the point of usage;
-
Continuous improvement - Make incremental improvements rather than overhauling the entire process.