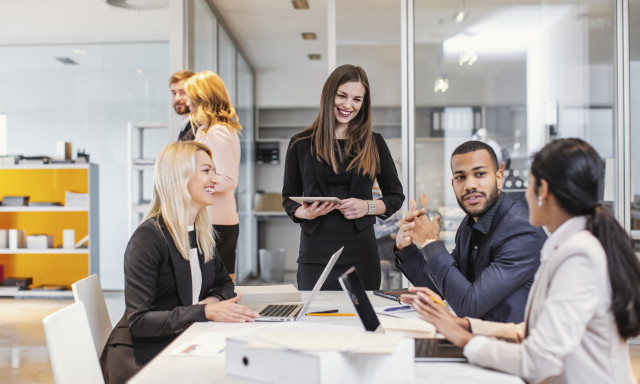
You've likely heard the term manager, regardless of whether you are a manager. This word is used to describe someone who leads, controls, or influences others. It's also a synonym for the word "leader." Managers are crucial in today’s business world for their ability and skill to communicate. Managers must be able communicate with their team members and set goals. Management is not a one-size-fits all solution.
Synonyms
You will need a database that contains synonyms for all words that have similar meanings in order to be able to identify them. You should use synonyms with caution as they can lead to unexpected results. These results could be confusing. Many people use synonyms incorrectly and then try to fix the problem by changing settings. If you are one of these users, the following tips can help you to use synonyms correctly.

Synonyms are applied to all index replicas by default. To avoid this, you need to uncheck the checkbox for this behavior. Similarly, synonyms that are used for plural and singular words should be avoided. They don't guarantee the same results. Once you've made the changes, you can now use the synonym to manage to synonym. The system will save a copy of the synonym to your database.
Management: Meaning
The dictionary definition for manage is to supervise, direct, or control an affair. This definition is very broad and can include anything from goldfish to managing finances at college. In the business world, managing people can mean overseeing the work of others or coping with the stress of a new situation. A manager is someone who has the skills and knowledge to manage people and ensure that they reach their goals.
There are many synonyms for the word manage, including direct and conduit. Manage is used to describe the process of managing or manipulating an individual or group to achieve a specified goal. Control can be defined as the control of or restraining group behavior. These terms are often used in conjunction. This can make it easier for you to see how the two words relate. You don't have to know the exact meaning of a particular word? These examples will help you.
Management as a separate process
Management has been used to denote a range of functions, processes, or strategies that can be applied for a variety purposes. This complex process focuses on organizing, planning, and controlling a group of resources. This process involves various methods to achieve a defined purpose, including human, material, and financial resources. Terry's definitions include all activities necessary for achieving the company's objectives. It stresses the importance of the human component, which gives it its unique character as a social process.
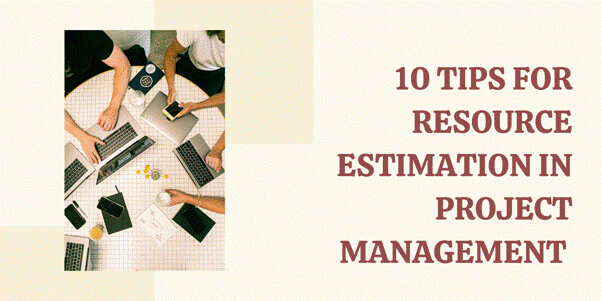
Management is the social process that plans, organizes, commands, coordinates, controls, and directs efforts. Non-managers contribute directly and are self-directed to achieve the goals of the organization. This definition of management demonstrates how difficult it is for people to be managed. Management is the process of organizing, planning, staffing and leading the efforts of individuals within an organization.
FAQ
What are management theories?
Management concepts are the fundamental principles and practices that managers use when managing people and their resources. They cover topics like job descriptions (job descriptions), performance evaluations, training programmes, employee motivation and compensation systems.
What are the four major functions of Management?
Management is responsible for organizing, managing, directing and controlling people, resources, and other activities. It also includes developing policies and procedures and setting goals.
Management helps an organization achieve its objectives by providing direction, coordination, control, leadership, motivation, supervision, training, and evaluation.
The four main functions of management are:
Planning - Planning refers to deciding what is needed.
Organizing: Organizing refers to deciding how things should work.
Direction - This is the art of getting people to follow your instructions.
Controlling - This is the ability to control people and ensure that they do their jobs according to plan.
What is TQM, exactly?
The industrial revolution was when companies realized that they couldn't compete on price alone. This is what sparked the quality movement. If they wanted to stay competitive, they needed to improve their quality and efficiency.
Management developed Total Quality Management to address the need for improvement. It focused on all aspects of an organisation's performance. It included continuous improvement and employee involvement as well as customer satisfaction.
What is the difference of a program and project?
A project is temporary, while a program lasts forever.
A project typically has a defined goal and deadline.
This is often done by a group of people who report to one another.
A program usually has a set of goals and objectives.
It is usually done by one person.
What is the difference of leadership and management?
Leadership is about influencing others. Management is about controlling others.
A leader inspires his followers while a manager directs the workers.
A leader motivates people and keeps them on task.
A leader develops people; a manager manages people.
Statistics
- The average salary for financial advisors in 2021 is around $60,000 per year, with the top 10% of the profession making more than $111,000 per year. (wgu.edu)
- UpCounsel accepts only the top 5 percent of lawyers on its site. (upcounsel.com)
- Hire the top business lawyers and save up to 60% on legal fees (upcounsel.com)
- Your choice in Step 5 may very likely be the same or similar to the alternative you placed at the top of your list at the end of Step 4. (umassd.edu)
- As of 2020, personal bankers or tellers make an average of $32,620 per year, according to the BLS. (wgu.edu)
External Links
How To
What is Lean Manufacturing?
Lean Manufacturing methods are used to reduce waste through structured processes. These processes were created by Toyota Motor Corporation, Japan in the 1980s. The goal was to produce quality products at lower cost. Lean manufacturing focuses on eliminating unnecessary steps and activities from the production process. It is composed of five fundamental elements: continuous improvement; pull systems, continuous improvements, just-in–time, kaizen, continuous change, and 5S. Pull systems allow customers to get exactly what they want without having to do extra work. Continuous improvement is constantly improving upon existing processes. Just-in-time is when components and other materials are delivered at their destination in a timely manner. Kaizen stands for continuous improvement. Kaizen can be described as a process of making small improvements continuously. Five-S stands for sort. It is also the acronym for shine, standardize (standardize), and sustain. These five elements are used together to ensure the best possible results.
The Lean Production System
Six key concepts are the basis of lean production:
-
Flow - focuses on moving information and materials as close to customers as possible.
-
Value stream mapping - Break down each stage in a process into distinct tasks and create an overview of the whole process.
-
Five S's, Sort, Set in Order, Shine. Standardize. and Sustain.
-
Kanban – visual signals like colored tape, stickers or other visual cues are used to keep track inventory.
-
Theory of constraints: identify bottlenecks in your process and eliminate them using lean tools, such as kanban board.
-
Just-in-time delivery - Deliver components and materials right to your point of use.
-
Continuous improvement - incremental improvements are made to the process, not a complete overhaul.