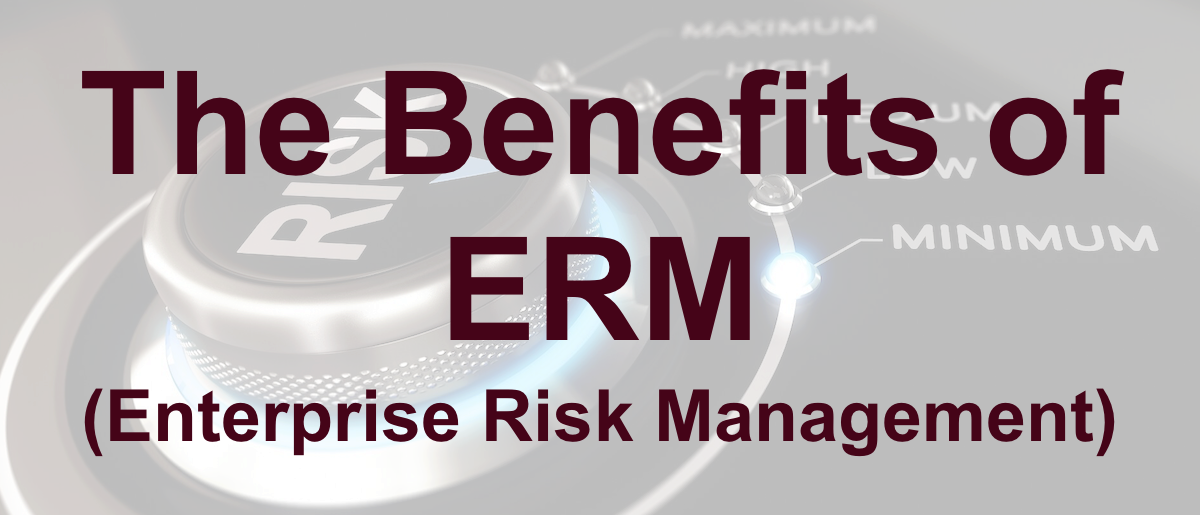
A manufacturing business owner will know how important it can be to shorten cycle times. A longer cycle time means that a process takes more time to complete. Here are some tips to reduce your cycle times:
Process time
Process time cycle times are an important manufacturing KPI. They are used by teams to determine when jobs should be started and finished, as well as their delivery capabilities. It is simple to calculate cycle time and it can be expressed using a variety different units. Many manufacturing analytics systems incorporate cycle time calculations. Here is an example cycle time breakdown
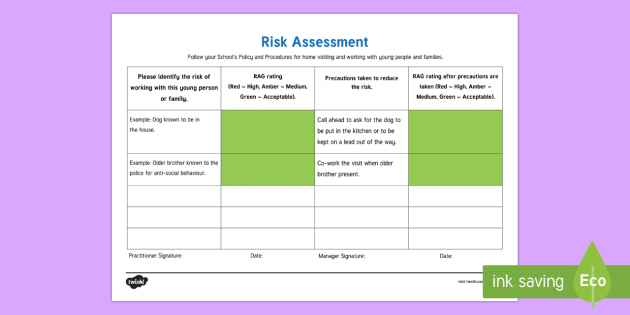
It is important to find out which steps are too slow when analysing process time. These steps can lead to bottlenecks that slow down other steps. In a perfect world, all process steps would work at the same speed, with no idle time or work-in-process (WIP). A process manager can determine if there are areas that need improvement and make the necessary changes to improve their processes.
Order processing time
It is crucial that you know the cycle time of an order before processing it. This will help you determine how long it takes to fulfill it. This will ensure your business remains competitive and stays ahead of the competition. Calculating the cycle times is as simple as calculating how long it takes for a task to be completed, not including any waiting periods. The shipping time for the item once it's made should also be considered. It may be necessary to modify your order processing if you have a long cycle time.
Whether your organization processes thousands or millions of orders each year, calculating cycle times is vital. This can be used to identify areas that your company can improve or cut costs. You can also give a realistic timeline to customers by knowing the time it takes. The cycle time formula uses the relationship between lead and takt. This formula will give you an accurate indication of how long customers will wait before they receive their orders.
Product production times
If you have a new product or service, it is important to optimize your production time cycle times. This will enable you to bring your product to market more quickly and save money. Not only will you save on labor costs, but your cycle time can be cut by improving processes, removing unnecessary steps and increasing productivity. You can cut down on the time it takes to produce a product. This will reduce the amount of money you spend on labor, equipment and utilities. This can help increase your earnings.
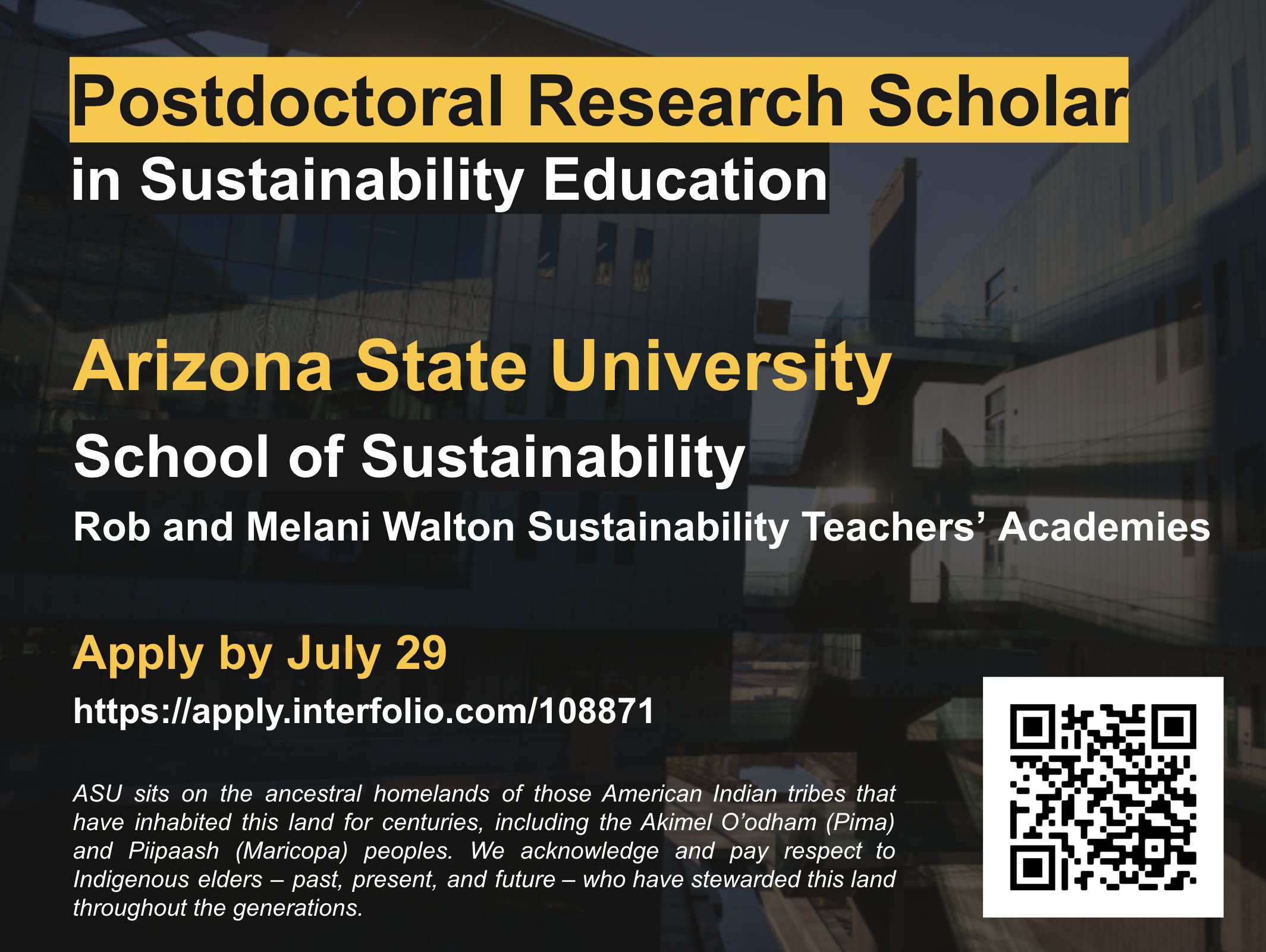
Once you've analyzed how much your product or service costs, you'll be able to create a more accurate estimate of the overall cost. You'll be able to estimate the costs of materials, labor, and delivery. You can then price the product accordingly. It's a great way of ensuring that your costs are within a reasonable range by using a cycle time calculator. This calculator can help you plan ahead and ensure your project runs smoothly.
FAQ
What are the steps of the management decision-making process?
The decision-making process for managers is complex and multifaceted. It involves many elements, including analysis, strategy. planning. implementation. measurement. evaluation. feedback.
When managing people, the most important thing to remember is that they are just human beings like you and make mistakes. You can always improve your performance, provided you are willing to make the effort.
This video will explain how decision-making works in Management. We'll discuss the different types and reasons they are important. Managers should also know how to navigate them. These topics are covered in this course:
How can we create a culture of success in our company?
A positive company culture creates a sense of belonging and respect in its people.
It's built on three fundamental principles:
-
Everyone has something to contribute
-
People are treated fairly
-
People and groups should respect each other.
These values can be seen in the behavior of people. They will treat others with consideration and courtesy.
They will be respectful of the opinions of other people.
They encourage others to express their feelings and ideas.
Additionally, the company culture encourages open communication as well as collaboration.
People can freely express their opinions without fear or reprisal.
They are aware that mistakes can be accepted if they are treated honestly.
Finally, the company culture encourages honesty as well as integrity.
Everyone understands that the truth is always best.
Everyone recognizes that rules and regulations are important to follow.
And no one expects special treatment or favors.
What is TQM?
When manufacturing companies realized that price was not enough to compete, the industrial revolution brought about the quality movement. If they wanted to stay competitive, they needed to improve their quality and efficiency.
In response to this need for improvement, management developed Total Quality Management (TQM), which focused on improving all aspects of an organization's performance. It included continuous improvement and employee involvement as well as customer satisfaction.
What's the difference between a program and a project?
A project is temporary; a program is permanent.
Projects usually have a goal and a deadline.
It is often carried out by a team of people who report back to someone else.
A program often has a set goals and objectives.
It is often done by one person.
What is Kaizen and how can it help you?
Kaizen refers to a Japanese term that stands for "continuous improvements." It is a philosophy which encourages employees in continuously improving their work environment.
Kaizen is founded on the belief of everyone being able to do their job well.
Six Sigma is so beloved.
Six Sigma can be implemented quickly and produce impressive results. Six Sigma provides a framework to measure improvements and allows companies to focus on the most important things.
What are the most common errors made by managers?
Managers can make their jobs more difficult than necessary.
They may not delegate enough responsibilities and not provide sufficient support.
Many managers lack the communication skills to motivate and lead their employees.
Managers can set unrealistic expectations for their employees.
Managers might try to solve every problem by themselves rather than delegating the responsibility.
Statistics
- The BLS says that financial services jobs like banking are expected to grow 4% by 2030, about as fast as the national average. (wgu.edu)
- UpCounsel accepts only the top 5 percent of lawyers on its site. (upcounsel.com)
- The average salary for financial advisors in 2021 is around $60,000 per year, with the top 10% of the profession making more than $111,000 per year. (wgu.edu)
- This field is expected to grow about 7% by 2028, a bit faster than the national average for job growth. (wgu.edu)
- The profession is expected to grow 7% by 2028, a bit faster than the national average. (wgu.edu)
External Links
How To
How do I get my Six Sigma license?
Six Sigma can be used to improve quality and efficiency. Six Sigma is a method that helps companies get consistent results from their operations. Named after the Greek word for "sigmas", the name refers to the first two letters. This process was developed at Motorola in 1986. Motorola recognized the need to standardize manufacturing processes in order to produce better products at a lower cost. They had been having problems with consistency because of the many different people who were doing the work. They decided to use statistical tools like control charts and Pareto analysis to solve the problem. After this, they would apply these techniques to every part of the operation. This would allow them to make any necessary changes. There are three main steps to follow when trying to get your Six Sigma certification. First, you need to determine if your qualifications are valid. You will need to complete some classes before you can start taking the tests. Once you've passed those classes, you'll start taking the tests. The class material will be reviewed. Next, you'll be ready for the test. If you pass, then you will become certified. Finally, your certifications will be added to your resume.