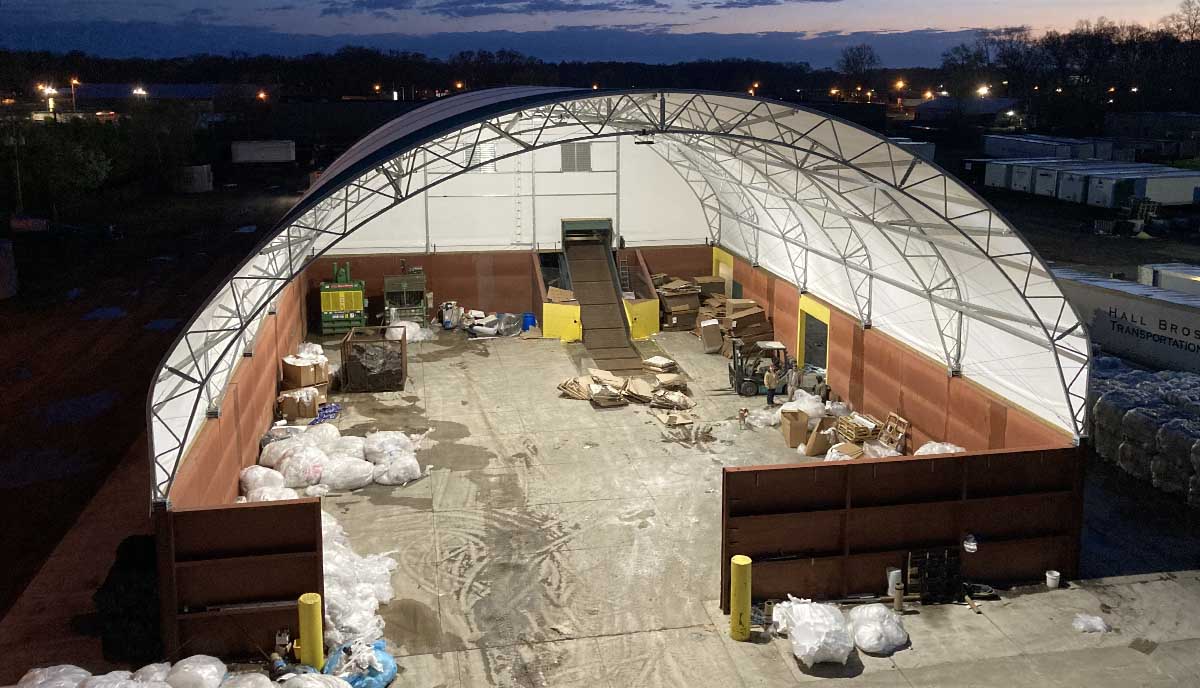
Strategic sourcing involves identifying and evaluating the best vendors for a given task. It involves many steps from market research and benchmarking to finding the right partners. The best vendor for the task is not enough. Strategic sourcing also requires that you consider return on investment. This includes determining the time and investment required to establish a new company and the savings that can be made over the long term.
Market research
Market research agencies are able to unlock the potential of your business by identifying new markets, demographics, and other opportunities. They can also help you create concrete business strategies that are supported with data. These agencies perform different types of research, including primary research (focus groups), secondary research (review of published sources and identifying relevant publications), and data acquisition (data mining).
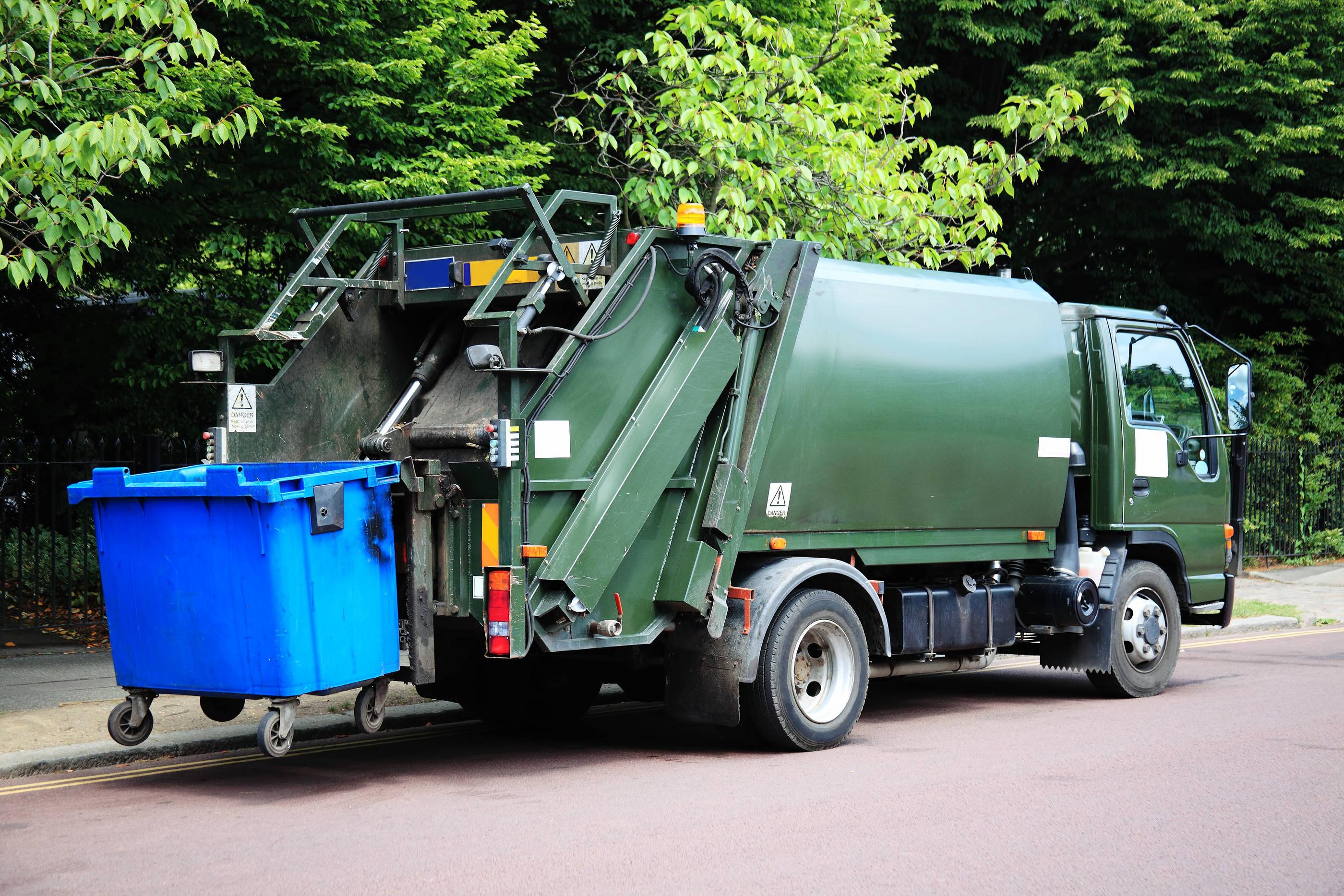
Forecasting
Forecasting is an important aspect of strategic sourcing. Forecasting can be used to help businesses predict demand. This can allow for shorter lead times, and improve customer trust. Forecasting is also able to eliminate the need for safety stock. This is an excess inventory that is kept in reserve for unforeseen demand. This saves storage space and time.
Establishing partnerships
Strategic sourcing requires the creation of partnerships with suppliers capable of fulfilling a particular requirement. These partnerships need to be developed in a collaborative manner. It is essential that there be mutual trust and alignment of goals. It also requires a dedicated resource to ensure that a successful partnership will result in better business outcomes.
Identifying the best partner
It is a crucial first step in any strategic sourcing project to identify the best partner. It is critical to communicate with suppliers and understand their capabilities gaps before finalizing a strategic sourcing contract. After a team of strategic sourcing professionals has chosen its perfect partner, they need to communicate their next steps with suppliers and follow their recommendations.
Cost analysis
Strategic sourcing is incomplete without cost analysis. This allows companies to see the profit margins of their suppliers and helps them determine if they can cut costs by selecting a cheaper supplier. It can also compare the prices for components and assembled products. The results can be used to inform procurement teams about which components and assemblies they should buy or manufacture.
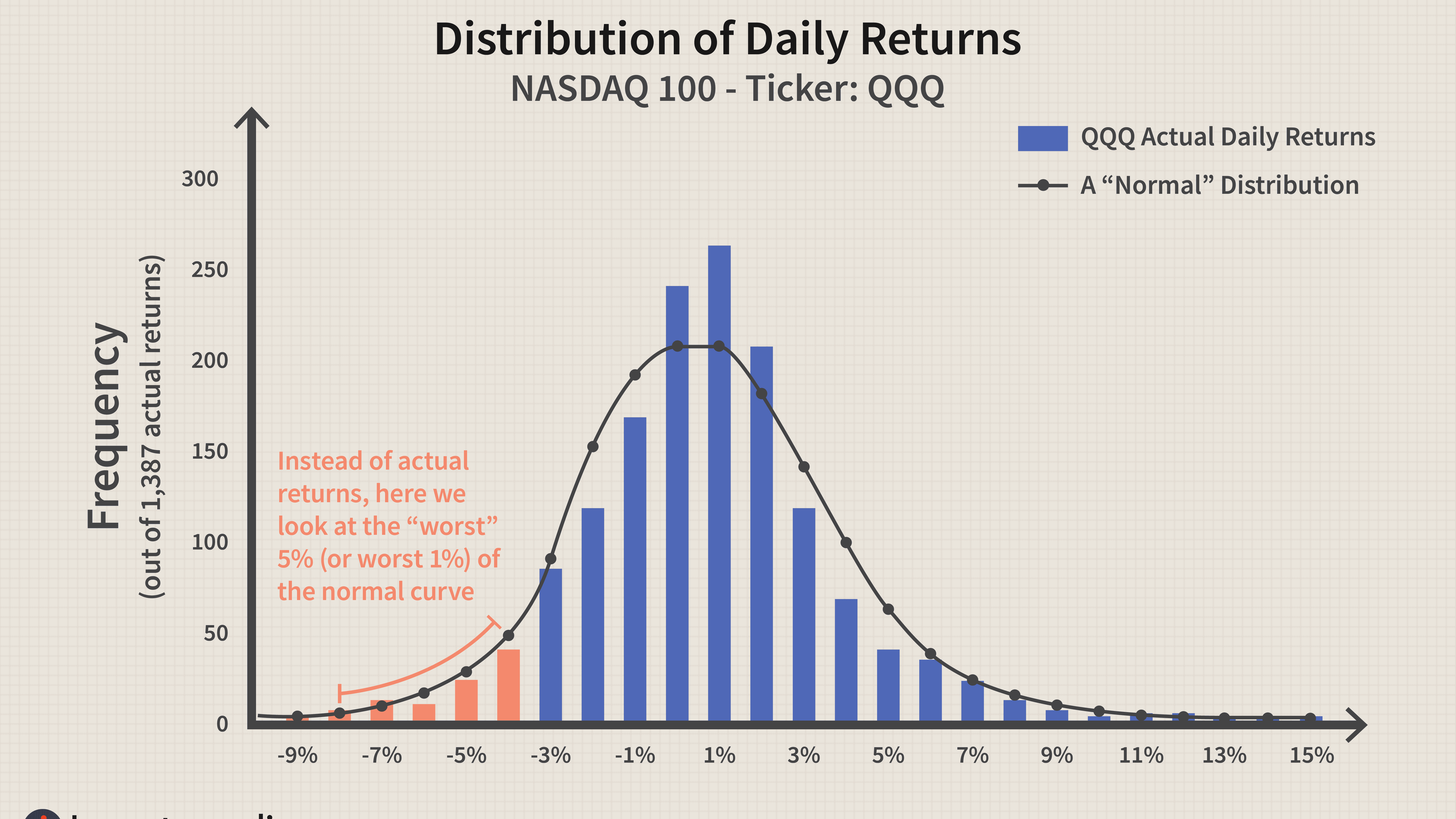
RFP technology
RFP technology is an important part of strategic sourcing. Companies can streamline their supplier evaluations and processes with the help of RFP technology. By automating their evaluations, companies can save time as well as money. A RFP software program is a great way to reduce the time required to select suppliers. It allows companies to create vendor profiles that allow them to track changes and keep up with the latest developments.
FAQ
What role does a manager have in a company's success?
There are many roles that a manager can play in different industries.
Managers generally oversee the day-today operations of a business.
He/she will ensure that the company fulfills its financial obligations.
He/she ensures employees adhere to all regulations and quality standards.
He/she plans and oversees marketing campaigns.
How do you manage your employees effectively?
Effectively managing employees means making sure they are productive and happy.
This also involves setting clear expectations and monitoring their performance.
Managers must set clear goals for their employees and themselves to achieve this goal.
They need to communicate clearly and openly with staff members. They also need to make sure that they discipline and reward the best performers.
They also need to keep records of their team's activities. These include:
-
What did we accomplish?
-
How much work was put in?
-
Who did it, anyway?
-
Was it done?
-
Why was this done?
This information can be used to monitor performance and evaluate results.
What is the difference in leadership and management?
Leadership is about influence. Management is about controlling others.
A leader inspires his followers while a manager directs the workers.
A leader motivates people to achieve success; a manager keeps workers on task.
A leader develops people; a manager manages people.
What are management concepts, you ask?
Management concepts are the fundamental principles and practices that managers use when managing people and their resources. They include such topics as human resource policies, job descriptions, performance evaluations, training programs, employee motivation, compensation systems, organizational structure, and many others.
Statistics
- As of 2020, personal bankers or tellers make an average of $32,620 per year, according to the BLS. (wgu.edu)
- UpCounsel accepts only the top 5 percent of lawyers on its site. (upcounsel.com)
- The average salary for financial advisors in 2021 is around $60,000 per year, with the top 10% of the profession making more than $111,000 per year. (wgu.edu)
- 100% of the courses are offered online, and no campus visits are required — a big time-saver for you. (online.uc.edu)
- This field is expected to grow about 7% by 2028, a bit faster than the national average for job growth. (wgu.edu)
External Links
How To
What is Lean Manufacturing?
Lean Manufacturing is a method to reduce waste and increase efficiency using structured methods. They were created by Toyota Motor Corporation in Japan in the 1980s. It was designed to produce high-quality products at lower prices while maintaining their quality. Lean manufacturing seeks to eliminate unnecessary steps and activities in the production process. It includes five main elements: pull systems (continuous improvement), continuous improvement (just-in-time), kaizen (5S), and continuous change (continuous changes). Pull systems are able to produce exactly what the customer requires without extra work. Continuous improvement means continuously improving on existing processes. Just-in-time refers to when components and materials are delivered directly to the point where they are needed. Kaizen means continuous improvement, which is achieved by implementing small changes continuously. Fifth, the 5S stand for sort, set up in order to shine, standardize, maintain, and standardize. These five elements are used together to ensure the best possible results.
Lean Production System
Six key concepts are the basis of lean production:
-
Flow is about moving material and information as near as customers can.
-
Value stream mapping- This allows you to break down each step of a process and create a flowchart detailing the entire process.
-
Five S's - Sort, Set In Order, Shine, Standardize, and Sustain;
-
Kanban – visual signals like colored tape, stickers or other visual cues are used to keep track inventory.
-
Theory of constraints - identify bottlenecks during the process and eliminate them with lean tools like Kanban boards.
-
Just-in Time - Send components and material directly to the point-of-use;
-
Continuous improvement - incremental improvements are made to the process, not a complete overhaul.