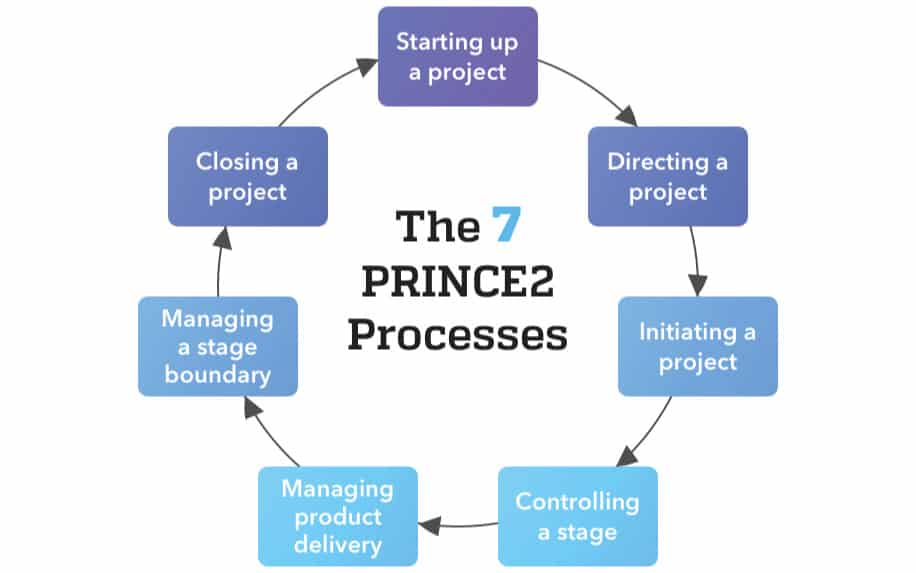
It is possible to achieve the desired results using a continuous improvements methodology. This method involves iterative design processes over multiple generations. It is also known under the name Lean Six Sigma. This article will discuss one variation of the PDSA technique based on SIPOC analysis. Its application is discussed within an engineering design workshop.
Lean Six Sigma
Lean Six Sigma (or Continuous Improvement) is a methodology that helps to make processes simpler and more predictable. Lean Six Sigma reduces errors which in turn lowers the likelihood of process failures. The method uses statistical process control methods (SPC) to improve process performance and control variables. It can be used to improve any product or service. Throughout the process, the company must define measurable characteristics and rely on data to guide changes.
PDSA
The PDSA continuous improvement methodology uses a continuous loop of process design, analysis, and action to improve a business process. The study step of PDSA is the first phase. This evaluates the effectiveness of an experimental improvement compared to the planned results. This step also helps the team determine whether the improvement has been a measurable success or not. The team will often conduct analysis and use control charts to determine if there is any special cause variation.
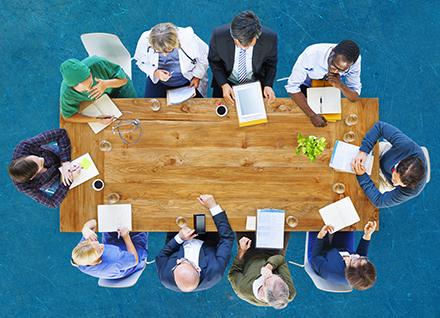
Variation of PDSA
PDSA (Personal Development and Support) is a method of continuous improvement and problem-solving, with a clearly defined focus and measurable targets. The process starts with careful planning. After that, the next step is to take effective action. Every idea is then evaluated for sustainability and feasibility. The project team makes sure that any improvement is sustainable by measuring the results.
PDSA based SIPOC analysis
SIPOC analysis provides a powerful tool for optimizing business processes. It is an easy-to-use method of categorizing data under 5 categories. SIPOC charts can help teams better understand each other's processes by providing a high quality overview. They can also help you focus your discussions.
PDSA based DMAIC
Continuous improvement methodologies that follow the DMAIC process are useful for organizations seeking to improve their processes. These simple methods can be used to help organizations identify inefficient processes and eliminate them. They also provide measurable and long-lasting results. These tools can help organizations track which changes have the most impact and which ones are not. It can be difficult for them to implement effective controls.
PDSA based in kanban board
Kanban boards have many benefits. Kanban boards allow you to visualize your work, assign tasks to other team members, and include attachments, images, or videos for each task. They also allow you to control the amount of work that is completed and when it is finished.
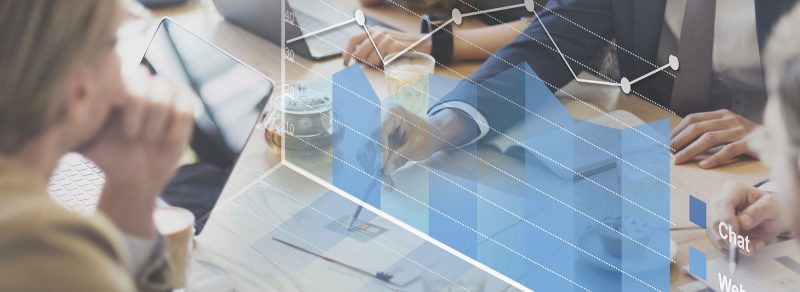
Kaizen based SIPOC analysis
The SIPOC model can be used as a powerful framework and concept in process improvement efforts. It is useful in helping to establish the boundaries of a process, collect relevant information, and make it clear and easy to understand. It is particularly useful during the Define phase in DMAIC methodologies. This tool is used to identify process variations that impact KVIPs or key performance indicators. It is also useful for teams and other stakeholders to plan improvements to improve processes.
PDSA based upon PDSA Variation
PDSA is a continuous improvement method that uses continuous comparisons of actual and expected results. The PDSA method measures the actual results of improvement experiments against the expected results. The reality of implementation is then compared to the plan. The team then analyzes the data to determine whether the experiment produced measurable improvements. This data is usually categorized using a chart called a "control chart", to help distinguish between expected variations and special causes.
FAQ
How to manage employees effectively?
Achieving employee happiness and productivity is key to managing them effectively.
This includes setting clear expectations for their behavior and tracking their performance.
Managers need clear goals to be able to accomplish this.
They need to communicate clearly and openly with staff members. They should also ensure that they both reward high performers and discipline those who are not performing to their standards.
They should also keep records of all activities within their team. These include:
-
What did we accomplish?
-
How much work were you able to accomplish?
-
Who did it?
-
How did it get done?
-
Why was it done?
This data can be used to evaluate and monitor performance.
How can we create a culture of success in our company?
A successful company culture is one that makes people feel valued and respected.
It is based on three principles:
-
Everyone has something valuable to contribute
-
People are treated fairly
-
There is mutual respect between individuals and groups
These values reflect in how people behave. They will treat others with kindness and consideration.
They will listen to other people's opinions respectfully.
And they will encourage others to share ideas and feelings.
A company culture encourages collaboration and communication.
People feel comfortable expressing their opinions freely without fear of reprisal.
They know mistakes will be accepted as long as they are dealt with honestly.
Finally, the company culture encourages honesty as well as integrity.
Everyone knows that they must always tell the truth.
Everyone is aware that rules and regulations apply to them.
People don't expect special treatment or favors.
What does the term "project management” mean?
This refers to managing all activities that are involved in a project's execution.
We help you define the scope of your project, identify the requirements, prepare the budget, organize the team, plan the work, monitor progress and evaluate the results before closing down the project.
What is the difference of a program and project?
A program is permanent while a project can be temporary.
A project has usually a specified goal and a time limit.
It is often performed by a team of people, who report back on someone else.
A program will usually have a set number of goals and objectives.
It is often done by one person.
What role should a manager play within a company
Each industry has a different role for a manager.
A manager is generally responsible for overseeing the day to day operations of a company.
He/she makes sure that the company meets its financial obligations, and that it produces goods or services that customers desire.
He/she ensures employees adhere to all regulations and quality standards.
He/she plans new products and services and oversees marketing campaigns.
Statistics
- Our program is 100% engineered for your success. (online.uc.edu)
- As of 2020, personal bankers or tellers make an average of $32,620 per year, according to the BLS. (wgu.edu)
- Hire the top business lawyers and save up to 60% on legal fees (upcounsel.com)
- The profession is expected to grow 7% by 2028, a bit faster than the national average. (wgu.edu)
- The average salary for financial advisors in 2021 is around $60,000 per year, with the top 10% of the profession making more than $111,000 per year. (wgu.edu)
External Links
How To
How do you implement a Quality Management Plan (QMP)?
Quality Management Plan (QMP), which was introduced in ISO 9001:2008, provides a systematic approach to improving processes, products, and services through continual improvement. It is about how to continually measure, analyze, control, improve, and maintain customer satisfaction.
QMP is a standard way to improve business performance. The QMP aims to improve the process of production, service delivery, and customer relationship. QMPs should cover all three dimensions - Products, Processes, and Services. When the QMP includes only one aspect, it is called a "Process" QMP. If the QMP is focused on a product/service, it's called a QMP. And when the QMP concentrates on Customer Relationships, it is called "Customer" QMP.
Scope, Strategy and the Implementation of a QMP are the two major elements. These elements are as follows:
Scope: This defines what the QMP will cover and its duration. If your organization wishes to implement a QMP lasting six months, the scope will determine the activities during the first six month.
Strategy: This is the description of the steps taken to achieve goals.
A typical QMP is composed of five phases: Planning Design, Development, Implementation and Maintenance. Here are the details for each phase.
Planning: This stage is where the QMP objectives are identified and prioritized. To get to know the expectations and requirements, all stakeholders are consulted. Once the objectives and priorities have been identified, it is time to plan the strategy to achieve them.
Design: This stage involves the creation of the vision, mission, strategies and tactics necessary to implement the QMP successfully. These strategies are put into action by developing detailed plans and procedures.
Development: The development team is responsible for building the resources and capabilities necessary to implement the QMP effectively.
Implementation: This refers to the actual implementation or the use of the strategies planned.
Maintenance: It is an ongoing process that maintains the QMP over time.
Additional items must be included in QMP.
Stakeholder Involvement: Stakeholders are important for the success of the QMP. They should be involved in planning, design, development and implementation of the QMP.
Project Initiation: The initiation of any project requires a clear understanding of the problem statement and the solution. This means that the initiator should know why they want something done and what they hope for from the end result.
Time frame: It is crucial to know the time frame for the QMP. The simplest version can be used if the QMP is only being implemented for a short time. However, if you have a long-term commitment, you may require more elaborate versions.
Cost Estimation: Another important component of the QMP is cost estimation. You can't plan without knowing how much money it will cost. Therefore, cost estimation is essential before starting the QMP.
QMPs are not just a written document. They should be a living document. It can change as the company grows or changes. It should therefore be reviewed frequently to ensure that the organization's needs are met.