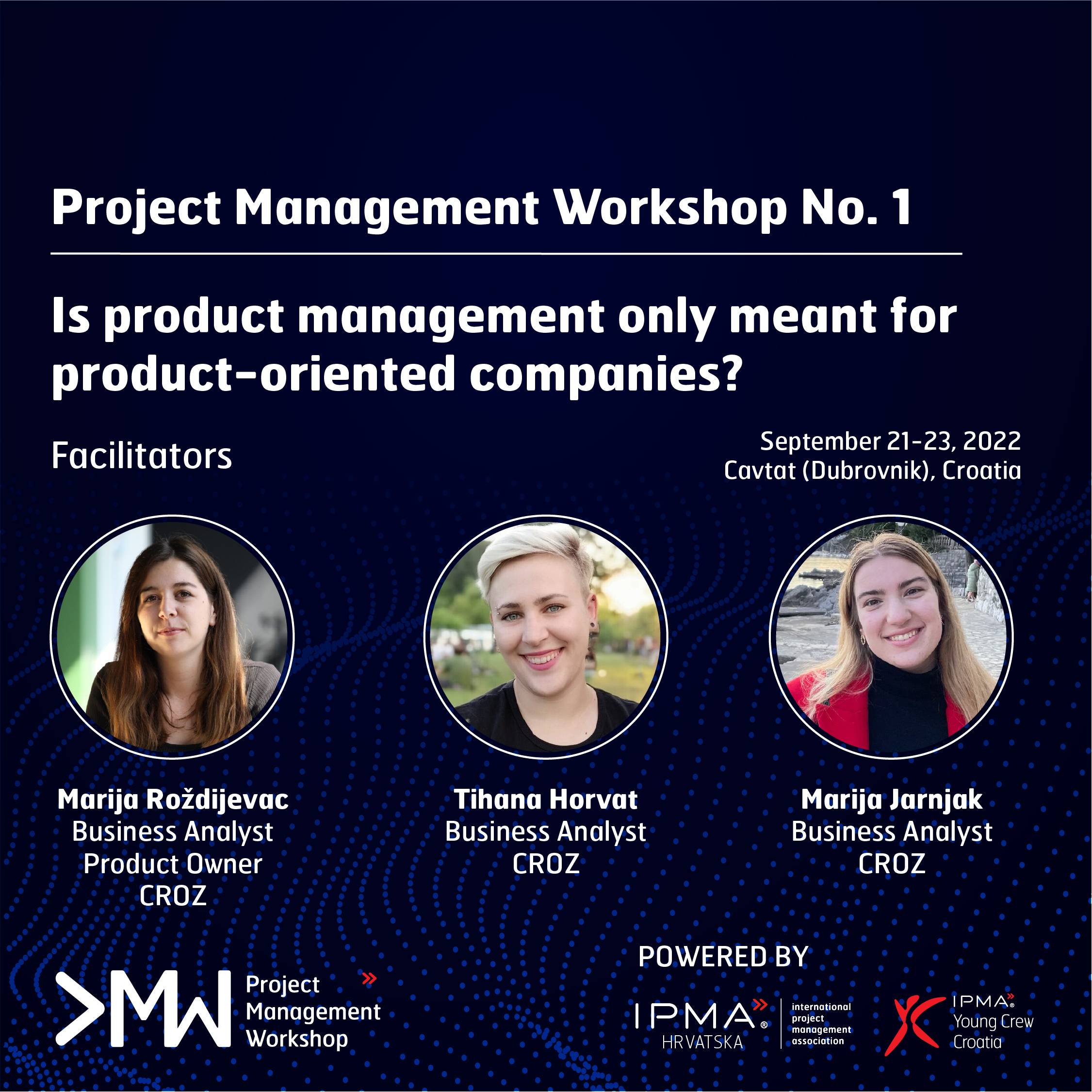
Engineering a building is an important task. There are many types working in the construction sector. There are four types of engineers: Civil engineers, structural engineers, electrical engineers and fire protection engineers. These engineers create construction plans and supervise their execution. They often collaborate with other engineers or manual labor. Engineers are often asked to suggest alternative ways to generate power as clients demand energy-efficient buildings. One common method is to use solar energy.
Civil engineers
Civil engineers are professionals involved in the construction of projects. They design, plan, and build projects. Additionally, they test finished products to ensure that everything is working as it should. They often spend the majority of their time on site dealing with numerous challenges and keeping up with project progress. Their goal is to make a structure that is both safe and sustainable. Civil engineers are in high demand, and many people seek a career in this field.
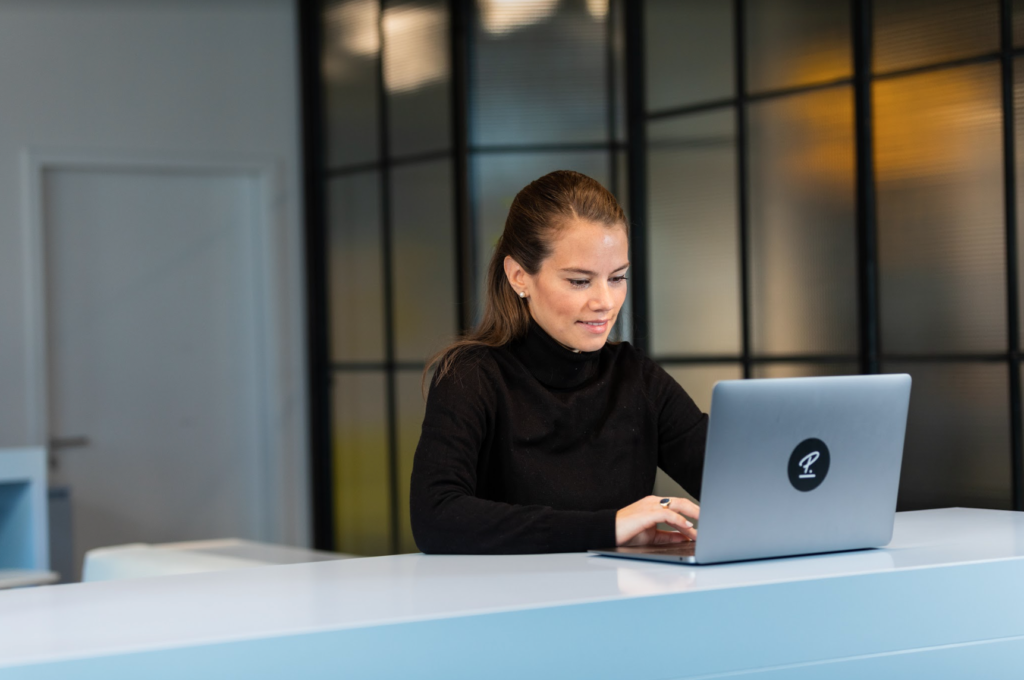
Structural engineers
From one project to the next, structural engineers play a variety of roles in construction. The role involves the analysis of the basic components of a building and liaising with other members of the project. It involves evaluating and inspecting the work done by contractors. The evaluation of foundation properties and conditions may be part of this role. To ensure that a building is constructed properly, structural engineers can also use computer-aided engineering (CAD).
Electricians
The job of an electrical engineer on a construction site is crucial in ensuring maximum safety. They make sure that electrical appliances are safe to be used by workers and that no exposed connections are made. They make sure that high-risk areas are not available. This job also requires extensive time management and communication skills. Electrical engineers have to master all the technical and soft skills needed to keep a construction site safe. They also have to be knowledgeable about electrical safety regulations and codes.
Fire protection engineers
Fire protection engineers have to be familiar with the building's chemistry and materials. They need to be able to recognize the interplay between fire suppression chemicals and fire. They should also be in close contact with legal entities and the public. This means they must know how to present findings and create court documents. A Master of Science degree, however, is highly desirable. Research in academia requires only a doctorate. There are many accredited schools for fire protection engineering.
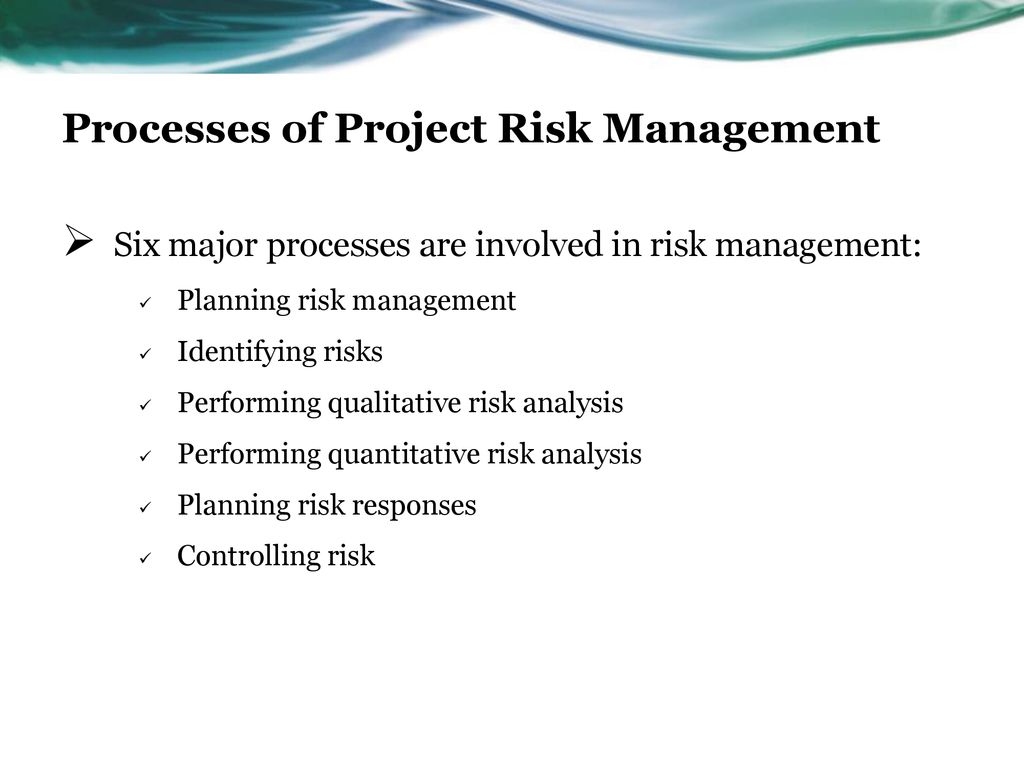
Engineers in the environment
The construction industry is both the largest end-user of natural resources and the greatest source of pollution. Environmental engineers have the responsibility of making sure that the industry is more sustainable and performs better. Environmental engineers can optimize construction sites while minimizing environmental impacts by using innovative design and life cycle assessments. Environmental engineers can help change outdated practices into environmentally friendly methods. Their knowledge will make or break the construction industry's future. These are some of the most important roles that environmental engineers play.
FAQ
How can we create a culture of success in our company?
Successful company culture is one where people feel valued and respected.
It is based on three principles:
-
Everyone has something to contribute
-
People are treated fairly
-
People and groups should respect each other.
These values can be seen in the behavior of people. For example, they will treat others with courtesy and consideration.
They will be respectful of the opinions of other people.
These people will inspire others to share thoughts and feelings.
Additionally, the company culture encourages open communication as well as collaboration.
People are free to speak out without fear of reprisal.
They know mistakes will be accepted as long as they are dealt with honestly.
The company culture promotes honesty, integrity, and fairness.
Everyone knows that they must always tell the truth.
Everyone understands there are rules that they must follow.
And no one expects special treatment or favors.
What is a fundamental management tool for decision-making?
A decision matrix is a simple but powerful tool for helping managers make decisions. It allows them to think through all possible options.
A decision matrix is a way to organize alternatives into rows and columns. It is easy to see how each option affects the other options.
In this example, there are four possible options represented by boxes on the left-hand side of the matrix. Each box represents a different option. The top row shows the status quo (the current situation), and the bottom row shows what would happen if nothing was done at all.
The effect of selecting Option 1 is shown in the middle column. It would translate into an increase in sales from $2million to $3million.
The following columns illustrate the impact of Options 2 and 3. These are good changes, they increase sales by $1million or $500,000. These changes can also have negative effects. Option 2 increases costs by $100 thousand, while Option 3 decreases profits to $200 thousand.
The last column shows you the results of Option 4. This would result in a reduction of sales of $1 million.
A decision matrix has the advantage that you don’t have to remember where numbers belong. You can just glance at the cells and see immediately if one given choice is better.
The matrix already does all the work. It is as simple as comparing the numbers within the relevant cells.
Here is an example of how a decision matrix might be used in your business.
Decide whether you want to invest more in advertising. You'll be able increase your monthly revenue by $5000 if you do. However, this will mean that you'll have additional expenses of $10,000.
You can calculate the net result of investing in advertising by looking at the cell directly below the one that says "Advertising." That number is $15 thousand. Advertising is a worthwhile investment because it has a higher return than the costs.
Why is Six Sigma so popular?
Six Sigma is easy and can deliver significant results. It can also be used to help companies identify and focus on the most important aspects of their business.
Why is it so hard to make smart business decisions?
Complex systems and many moving parts make up businesses. The people who run them must juggle multiple priorities at once while also dealing with uncertainty and complexity.
It is important to understand the effects of these factors on the system in order to make informed decisions.
You must first consider what each piece of the system does and why. It is important to then consider how the individual pieces relate to each other.
Ask yourself if there are hidden assumptions that have influenced your behavior. If you don't have any, it may be time to revisit them.
Try asking for help from another person if you're still stuck. You may be able to see things from a different perspective than you are and gain insight that can help you find a solution.
What is TQM exactly?
The industrial revolution led to the birth and growth of the quality movement. Manufacturing companies realized they couldn't compete solely on price. To remain competitive, they had to improve quality as well as efficiency.
In response to this need for improvement, management developed Total Quality Management (TQM), which focused on improving all aspects of an organization's performance. It included continuous improvement processes, employee involvement, and customer satisfaction.
Statistics
- 100% of the courses are offered online, and no campus visits are required — a big time-saver for you. (online.uc.edu)
- Hire the top business lawyers and save up to 60% on legal fees (upcounsel.com)
- UpCounsel accepts only the top 5 percent of lawyers on its site. (upcounsel.com)
- The BLS says that financial services jobs like banking are expected to grow 4% by 2030, about as fast as the national average. (wgu.edu)
- Your choice in Step 5 may very likely be the same or similar to the alternative you placed at the top of your list at the end of Step 4. (umassd.edu)
External Links
How To
What is Lean Manufacturing?
Lean Manufacturing uses structured methods to reduce waste, increase efficiency and reduce waste. They were created by Toyota Motor Corporation in Japan in the 1980s. The primary goal was to make products with lower costs and maintain high quality. Lean manufacturing eliminates unnecessary steps and activities from a production process. It is composed of five fundamental elements: continuous improvement; pull systems, continuous improvements, just-in–time, kaizen, continuous change, and 5S. Pull systems are able to produce exactly what the customer requires without extra work. Continuous improvement means continuously improving on existing processes. Just-intime refers the time components and materials arrive at the exact place where they are needed. Kaizen means continuous improvement. Kaizen involves making small changes and improving continuously. The 5S acronym stands for sort in order, shine standardize and maintain. These five elements work together to produce the best results.
Lean Production System
Six key concepts are the basis of lean production:
-
Flow: The goal is to move material and information as close as possible from customers.
-
Value stream mapping is the ability to divide a process into smaller tasks, and then create a flowchart that shows the entire process.
-
Five S’s - Sorted, In Order. Shine. Standardize. And Sustain.
-
Kanban - use visual signals such as colored tape, stickers, or other visual cues to keep track of inventory;
-
Theory of constraints - identify bottlenecks in the process and eliminate them using lean tools like kanban boards;
-
Just-in time - Get components and materials delivered right at the point of usage;
-
Continuous improvement - Make incremental improvements rather than overhauling the entire process.