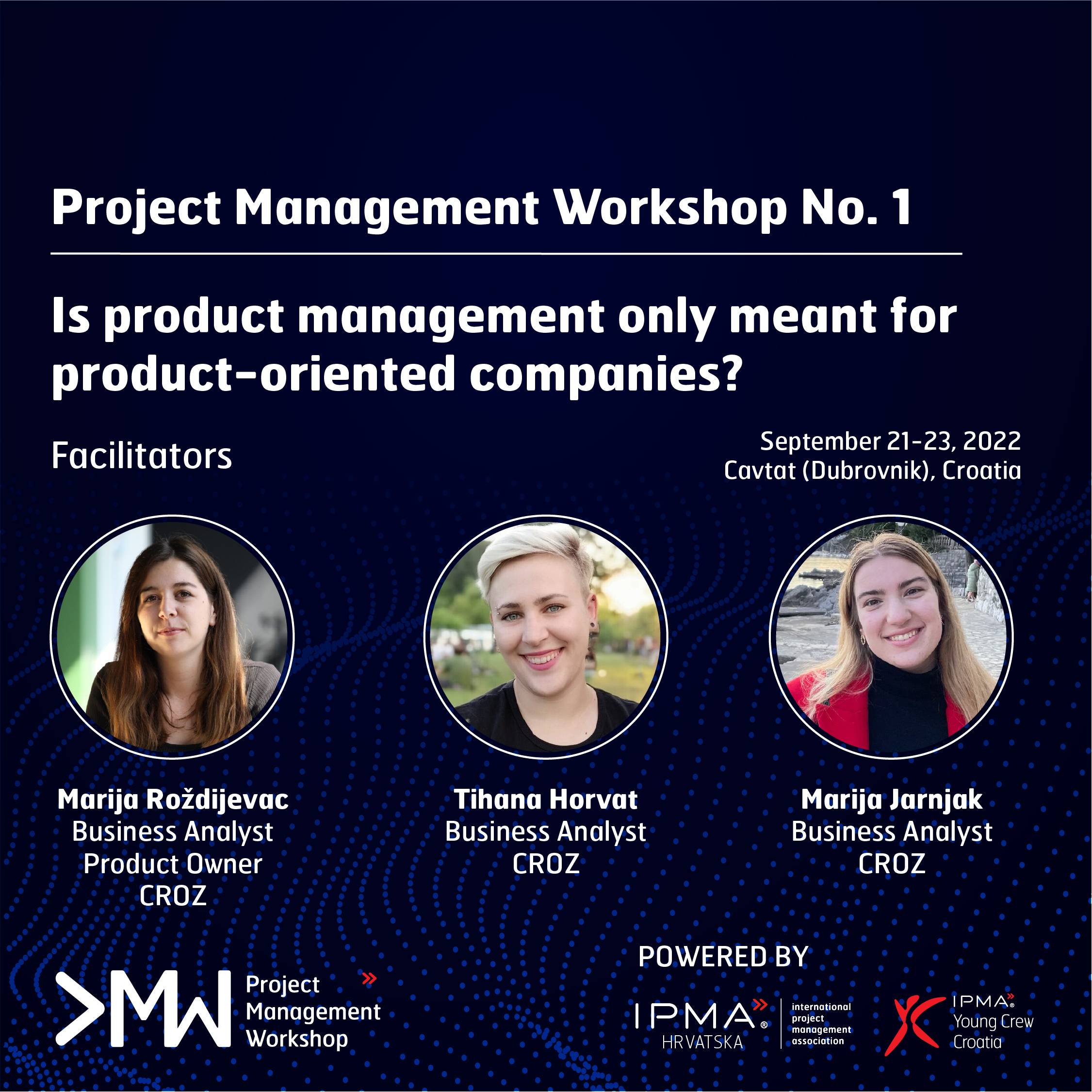
You have come to the right spot if you are looking for a career in construction administration. Continue reading to find out more about this career, including the requirements for education and the salary range. Next, you will learn how to prepare yourself for the interview. Are you thinking of applying for a job as a construction manager? The first step is to choose what type construction project you want.
Job description
A job description for construction management should clearly state the duties and responsibilities of this position. These professionals work closely with engineers, architects and other professionals to ensure that projects are completed on-time and within budget. Some managers supervise multiple projects at once, ensuring that all aspects of the project are completed in a timely manner. Their job is to maximize the project's overall value.
You should have a clear job description for construction managers that includes key details like working hours and location. Many potential managers are interested in remote work and travel opportunities. Highlight the benefits that make your position a unique construction manager. The best job descriptions end with a call to action that directs applicants to apply for the job. They should be well-written and emphasize the unique benefits and requirements for the position.
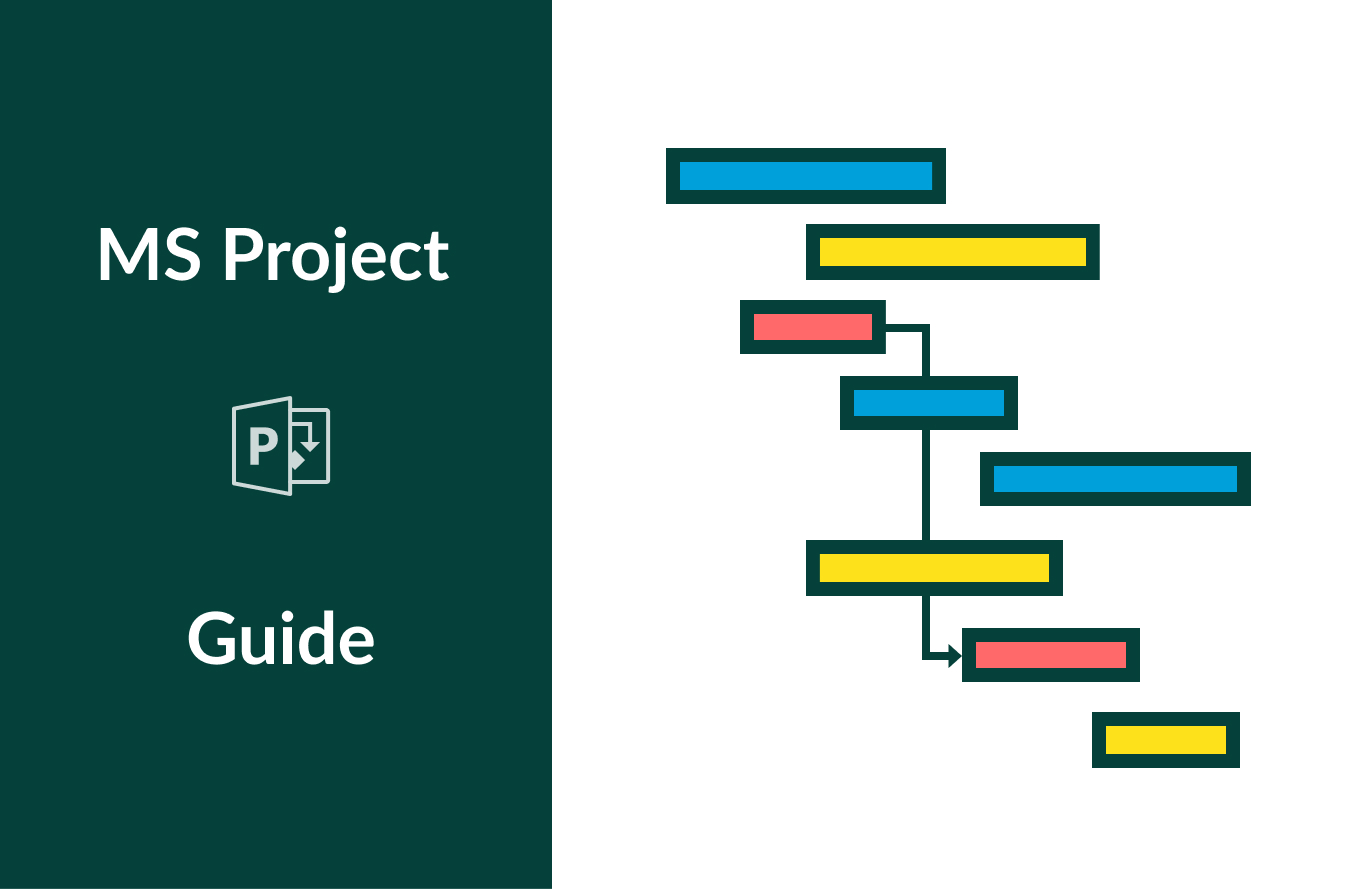
Education required
If you're interested in a career as a construction manager, you've probably been wondering what kind of education you'll need. Construction management is a top-level service that utilizes project management skills to coordinate the design, planning and construction phases of a job. This field requires you to work with a team that includes professionals who will ensure each step is done correctly and to client's satisfaction.
There are many entry points into the field of construction management, but a bachelor's in a related field is required for most positions. Undergraduate degrees in engineering and architecture are especially helpful for the field because they give graduates an in-depth understanding of the design process. LSU Online offers an option for an online bachelor's in construction management. This program prepares you for entry-level jobs and further studies in the field. The program will teach you about project control, design and methods as well how to estimate costs and build codes and standards. The certification exam will also cover management and safety aspects.
Career outlook
The job prospects for construction managers will improve as the economy continues to improve. According to the Bureau of Labor Statistics, employment opportunities for construction management professionals will increase by 8 percent over the next decade. This increase will be driven by a number of factors, including population growth, business growth, and new sustainability campaigns. For the foreseeable future, the construction industry will be an important part of the economy. Norwich University, one of the few online colleges offering this degree, offers a Master's program to prepare you for this exciting field.
The growth of construction activity is a strong driver of the job outlook for construction managers. The Bureau of Labor Statistics estimates a ten percent increase in jobs between 2016 and 2026, which is enough to fill a large number of open positions. Many construction managers could find more work with a high retirement rate. Building technologies are getting more complex and require higher levels of supervision. This job is ideal for those with advanced skills and education.
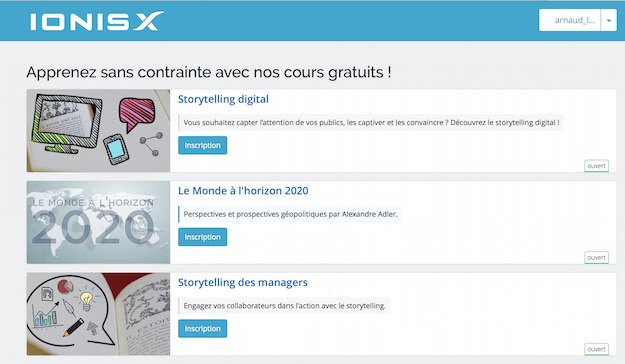
Salary
A description of a job in construction management describes the technical and professional aspects. These professionals supervise construction as well as overseeing design and planning. As such, they have a specialized understanding of these three areas, and their salary will depend on their level of experience and their level of education. These tips will help you to make your job hunt easier. Read on to learn more about the career outlook and salary ranges of construction management professionals.
Experience and education are the main factors that determine salaries for construction management. The average salary for construction managers was $74,950 in July 2017. With experience, you might be able get a job as soon as you apply. The sector has great growth potential as it is growing in both the corporate and industrial sectors. While home building has slowed, it will pick up again. It cannot be outsourced so it is fairly secure.
FAQ
How do you effectively manage employees?
Effectively managing employees requires that you ensure their happiness and productivity.
This includes setting clear expectations for their behavior and tracking their performance.
Managers need clear goals to be able to accomplish this.
They need to communicate clearly and openly with staff members. And they need to ensure that they reward good performance and discipline poor performers.
They should also keep records of all activities within their team. These include:
-
What was achieved?
-
How much work did you put in?
-
Who did it, anyway?
-
When it was done?
-
Why?
This information can be used for monitoring performance and evaluating results.
What are the most important management skills?
Any business owner needs to be able to manage people, finances, resources and time. These skills include the ability manage people, finances and resources as well as other factors.
When you need to manage people, set goals, lead teams, motivate them, solve problems, develop policies and procedures and manage change, management skills are essential.
There are so many managerial tasks!
Which kind of people use Six Sigma
Six-sigma will be well-known to anyone who has worked in operations research or statistics. Anyone involved in business can benefit.
Because it requires a high level of commitment, only those with strong leadership skills will make an effort necessary to implement it successfully.
What is a simple management tool that aids in decision-making and decision making?
A decision matrix is an easy but powerful tool to aid managers in making informed decisions. It helps them think systematically about all the options available to them.
A decision matrix is a way to organize alternatives into rows and columns. This allows one to see how each alternative impacts other options.
In this example, there are four possible options represented by boxes on the left-hand side of the matrix. Each box represents an option. The top row shows the status quo (the current situation), and the bottom row shows what would happen if nothing was done at all.
The effect of choosing Option 1 can be seen in column middle. In this case, it would mean increasing sales from $2 million to $3 million.
The next two columns show the effects of choosing Options 2 and 3. These are good changes, they increase sales by $1million or $500,000. But, they also have some negative consequences. Option 2, for example, increases the cost by $100 000 while Option 3 decreases profits by $200 000.
The final column shows results of choosing Option 4. This would result in a reduction of sales of $1 million.
The best thing about using a decision matrix is that you don't need to remember which numbers go where. The best thing about a decision matrix is that you can simply look at the cells, and immediately know whether one option is better or not.
This is because the matrix has done all the hard work. It's as easy as comparing numbers in the appropriate cells.
Here is an example how you might use the decision matrix in your company.
You want to decide whether or not to invest more money into advertising. By doing so, you can increase your revenue by $5 000 per month. However, additional expenses of $10 000 per month will be incurred.
By looking at the cell just below "Advertising", the net result can be calculated as $15 thousand. Advertising is worth much more than the investment cost.
What is the difference in Six Sigma and TQM?
The main difference between these two quality management tools is that six sigma focuses on eliminating defects while total quality management (TQM) focuses on improving processes and reducing costs.
Six Sigma can be described as a strategy for continuous improvement. It emphasizes the elimination or minimization of defects through statistical methods such control charts and p charts.
This method aims to reduce variation in product production. This is accomplished by identifying the root cause of problems and fixing them.
Total quality management is the measurement and monitoring of all aspects within an organization. Training employees is also part of total quality management.
It is commonly used as a strategy for increasing productivity.
What is TQM and how can it help you?
The industrial revolution saw the realization that prices alone were not sufficient to sustain manufacturing companies. This led to the birth of quality. If they wanted to stay competitive, they needed to improve their quality and efficiency.
Management developed Total Quality Management to address the need for improvement. It focused on all aspects of an organisation's performance. It included continual improvement processes, employee involvement, customer satisfaction, and customer satisfaction.
Statistics
- Hire the top business lawyers and save up to 60% on legal fees (upcounsel.com)
- Your choice in Step 5 may very likely be the same or similar to the alternative you placed at the top of your list at the end of Step 4. (umassd.edu)
- Our program is 100% engineered for your success. (online.uc.edu)
- 100% of the courses are offered online, and no campus visits are required — a big time-saver for you. (online.uc.edu)
- As of 2020, personal bankers or tellers make an average of $32,620 per year, according to the BLS. (wgu.edu)
External Links
How To
How can you use the Kaizen method?
Kaizen means continuous improvement. This Japanese term refers to the Japanese philosophy of continuous improvement that emphasizes incremental improvements and constant improvement. It is a process where people come together to improve their processes.
Kaizen is one method that Lean Manufacturing uses to its greatest advantage. This concept requires employees to identify and solve problems during manufacturing before they become major issues. This improves the quality of products, while reducing the cost.
Kaizen is a way to raise awareness about what's happening around you. So that there is no problem, you should immediately correct it if something goes wrong. If someone spots a problem while at work, they should immediately report it to their manager.
Kaizen has a set of basic principles that we all follow. Start with the end product, and then move to the beginning. For example, if we want to improve our factory, we first fix the machines that produce the final product. Then, we fix the machines that produce components and then the ones that produce raw materials. Then we fix the workers, who directly work with these machines.
This approach is called 'kaizen' because it focuses on improving everything steps by step. Once the factory is fixed, we return to the original site and work our way back until we get there.
It is important to understand how to measure the effectiveness and implementation of kaizen in your company. There are many ways you can determine if kaizen has been implemented well. Another way to determine if kaizen is working well is to look at the quality of the products. Another way is determining how much productivity increased after implementing kaizen.
If you want to find out if your kaizen is actually working, ask yourself why. Did you do it because it was legal or to save money? It was a way to save money or help you succeed.
Let's say you answered yes or all of these questions. Congratulations! You're ready to start kaizen.