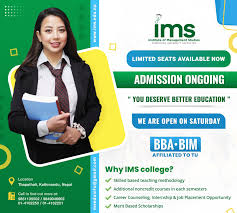
There are many kinds of management. Top-down management is one type. Top-down management emphasizes hierarchy and punishment for employees who do not follow orders. To keep employees happy, this type management relies on intimidation and fear. Other types of management emphasize the importance of empathy. Both types of management are equally effective. You can contact me if you have any questions regarding management! I would be happy to answer any questions you may have and help find you a job that suits your needs.
Management Principles
The basic principle of management is to develop a cause-and-effect relationship between action and its consequences. Effective management strategies will allow you to establish a link between the actions you take and the desired outcomes. The principles of management are generally universal and apply to all types of organisations, no matter how large or small. We will be discussing some of these principles and how they apply to different types organizations in the following article. Continue reading for more information.
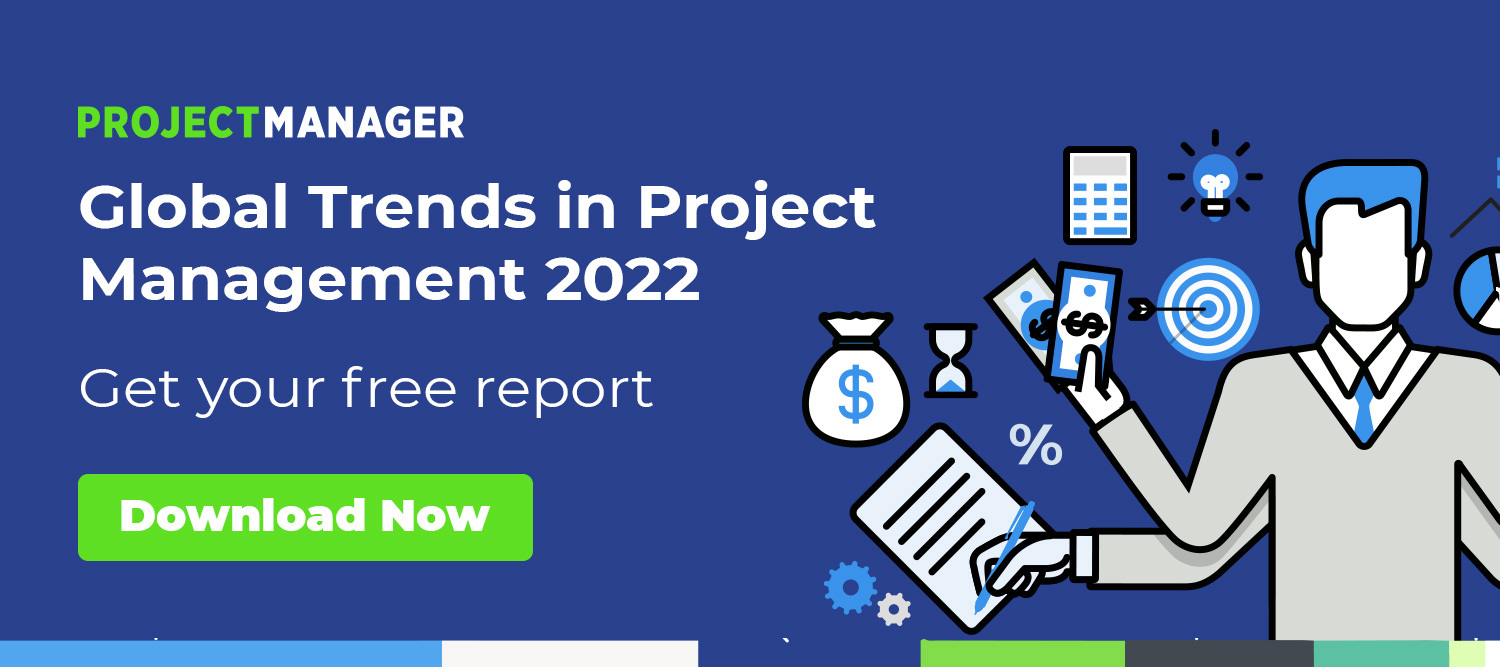
Management functions
Management's main functions are planning, organizing people, staffing and leading. The level of an organization will determine how much time managers spend on each area. Also, planning and organizing are not the same as leading and controlling, both of which are continuous processes. Organization includes the creation of a plan and allocation of resources in the most efficient way. Ultimately, the goal of management is to reach the destination without experiencing any problems.
Technology has an impact on management
Technology has had a tremendous impact on business management. In the early 1900s, a French mining engineer, Henri Fayol, described a scientific method for managing a business. Fayol suggested six essential functions that management should perform. These functions are applicable to almost every department within most companies. The introduction of computer hardware and software revolutionized the way work is organized and directed. Many managers remain the same, but the new technology and processes have fundamentally changed the way that they work.
Management is more effective when empathy is valued
While empathy may be viewed as a simple way to connect with others and feel emotions, it also has real-world benefits that organizations can benefit from. Empathy is closely linked with organizational and social success. Some of the definitions for empathy are now less accurate, as people are more distant from and less interested in other people's lives. It can be difficult to feel empathy in such a context. This article will help you to cultivate empathy in your organization.
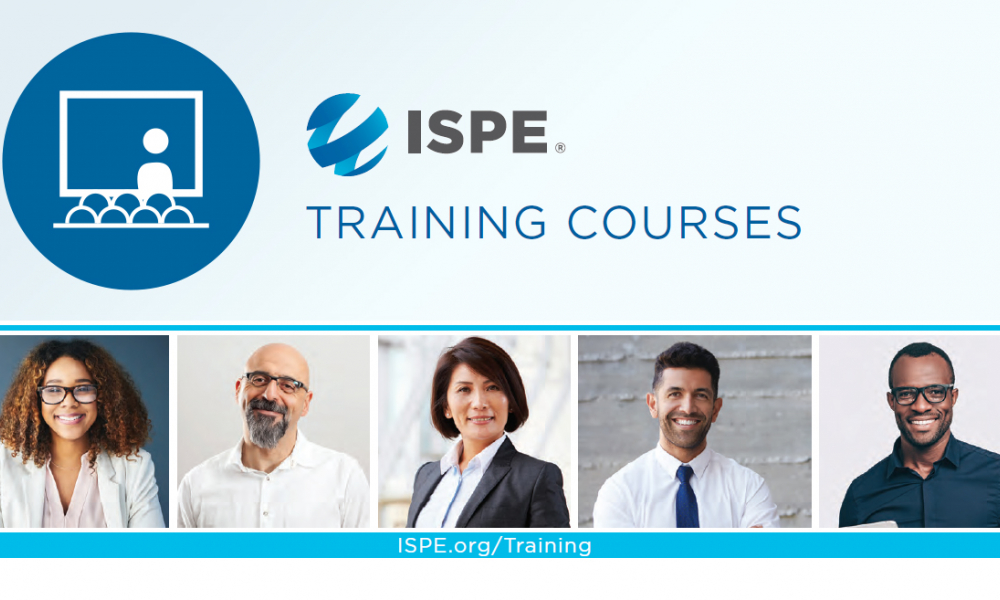
Management errors can result in high prices
Poor management can lead to lost productivity. In a Gallup report, the cost of a single disgruntled employee costs $360 billion a year. Disengagement costs another expense. Both these costs are huge for the business. In addition to the lost productivity, poor management also affects the bottom line in other ways. Here are five ways poor management can cost businesses money.
FAQ
Six Sigma is so popular.
Six Sigma is easy to implement and can produce significant results. It provides a framework that allows for improvement and helps companies concentrate on what really matters.
How can a manager motivate employees?
Motivation refers to the desire or need to succeed.
Enjoyable activities can motivate you.
You can also get motivated by seeing your contribution to the success or the improvement of the organization.
For example, if you want to become a doctor, you'll probably find it more motivating to see patients than to study medicine books all day.
Another source of motivation is within.
You might feel a strong sense for responsibility and want to help others.
You might even enjoy the work.
If you feel unmotivated, ask yourself why.
Then try to think about ways to change your situation to be more motivated.
What is the difference between TQM and Six Sigma?
The main difference between these two quality management tools is that six sigma focuses on eliminating defects while total quality management (TQM) focuses on improving processes and reducing costs.
Six Sigma is an approach for continuous improvement. It emphasizes the elimination and improvement of defects using statistical methods, such as control charts, P-charts and Pareto analysis.
This method attempts to reduce variations in product output. This is done by identifying root causes and rectifying them.
Total quality management includes monitoring and measuring all aspects of an organization's performance. This includes training employees to improve their performance.
It is commonly used as a strategy for increasing productivity.
How does Six Sigma work?
Six Sigma uses statistics to measure problems, find root causes, fix them, and learn from past mistakes.
The first step in solving a problem is to identify it.
The next step is to collect data and analyze it in order to identify trends or patterns.
Then corrective actions are taken to solve the problem.
Finally, data is reanalyzed to determine whether the problem has been eliminated.
This continues until you solve the problem.
What are the 4 main functions of management?
Management is responsible to plan, organize, direct, and control people and resources. It also includes developing policies and procedures and setting goals.
Management is the ability to direct, coordinate, control, motivate, supervise, train, and evaluate an organization's efforts towards achieving its goals.
The following are the four core functions of management
Planning - Planning involves determining what needs to be done.
Organizing is the act of deciding how things should go.
Directing - Directing means getting people to follow instructions.
Controlling - This is the ability to control people and ensure that they do their jobs according to plan.
Statistics
- The BLS says that financial services jobs like banking are expected to grow 4% by 2030, about as fast as the national average. (wgu.edu)
- 100% of the courses are offered online, and no campus visits are required — a big time-saver for you. (online.uc.edu)
- Hire the top business lawyers and save up to 60% on legal fees (upcounsel.com)
- The average salary for financial advisors in 2021 is around $60,000 per year, with the top 10% of the profession making more than $111,000 per year. (wgu.edu)
- UpCounsel accepts only the top 5 percent of lawyers on its site. (upcounsel.com)
External Links
How To
What is Lean Manufacturing?
Lean Manufacturing is a method to reduce waste and increase efficiency using structured methods. They were created in Japan by Toyota Motor Corporation during the 1980s. The goal was to produce quality products at lower cost. Lean manufacturing is about eliminating redundant steps and activities from the manufacturing process. It includes five main elements: pull systems (continuous improvement), continuous improvement (just-in-time), kaizen (5S), and continuous change (continuous changes). Pull systems allow customers to get exactly what they want without having to do extra work. Continuous improvement is the continuous improvement of existing processes. Just-intime refers the time components and materials arrive at the exact place where they are needed. Kaizen means continuous improvement, which is achieved by implementing small changes continuously. Last but not least, 5S is for sort. These five elements are combined to give you the best possible results.
Lean Production System
Six key concepts make up the lean manufacturing system.
-
Flow - focuses on moving information and materials as close to customers as possible.
-
Value stream mapping - Break down each stage in a process into distinct tasks and create an overview of the whole process.
-
Five S's, Sort, Set in Order, Shine. Standardize. and Sustain.
-
Kanban – visual signals like colored tape, stickers or other visual cues are used to keep track inventory.
-
Theory of constraints: identify bottlenecks in your process and eliminate them using lean tools, such as kanban board.
-
Just-intime - Order components and materials at your location right on the spot.
-
Continuous improvement - make incremental improvements to the process rather than overhauling it all at once.