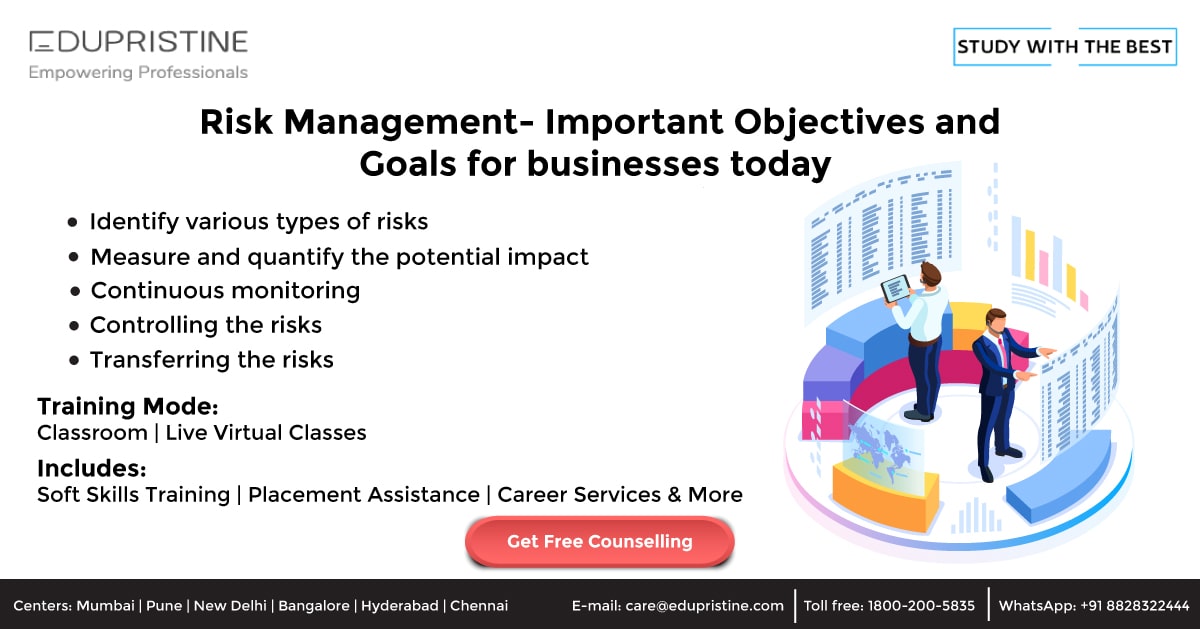
Defining the role of middle management
The role of middle management in a company is to connect top-level management with lower-level employees. They translate the strategy developed by the executive team into achievable department goals. They also collect data and present results to the executive group. They have a wide range of responsibilities, including overseeing the work and decisions made about allocations of resources.
In the federal government, middle management has similar or greater supervisory responsibilities than front-line managers. Their duties include setting up policies and guidelines that will govern the work performed by lower-level staff.
Mid-managers face many challenges
Middle managers often face a conflicting set of roles, which can lead to frustration. Managers have to manage subordinates and report to the higher-ups. However, they also have to enforce policies that aren’t theirs. Direct reports might object to these policies. Technology can be a great tool for middle managers to solve this problem. PwC, for instance, can identify digital training opportunities and direct managers to more that 300 courses.
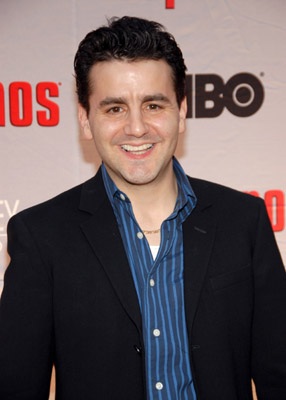
The middle managers need to be able understand all parties and establish a relationship of trust between them. It can be difficult as they may have to manage multiple stakeholders and their time. As a result, they need to prioritize their tasks and ensure that all needs are met.
Tools for middle managers to collaborate
The role of middle managers is crucial in any organization. They are responsible for keeping track of project progress and moving information between teams. But communication is more difficult when working remotely. There are many tools out there that will help middle managers collaborate better.
Managers in the middle often have to deal with a lot meetings. It can take up 35% of their time. Their time is limited and they don't have the ability to do any other work. Video communication also increases their cognitive load. This can cause burnout.
Communication skills
The success of middle managers depends on their communication skills. These professionals play a demanding role. They must work in close collaboration with both senior management and the frontline workers. The ability to communicate effectively can improve trust and engagement with colleagues, as well as their performance and influence.
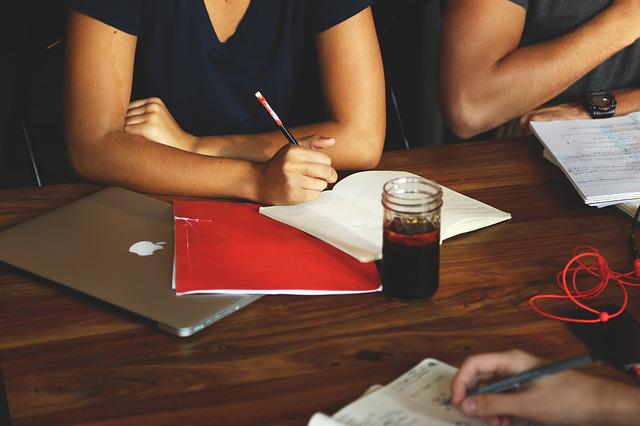
Communication skills in middle managers are crucial in every field. Middle managers have direct contact with their employees, which is not the case for senior administrators. Effective communication is essential for middle managers. To avoid miscommunications and errors, middle managers need to be able communicate clearly and effectively.
FAQ
What role should a manager play within a company
Different industries have different roles for managers.
A manager is generally responsible for overseeing the day to day operations of a company.
He/she is responsible for ensuring that the company meets all its financial obligations and produces the goods or services customers want.
He/she ensures that employees follow the rules and regulations and adhere to quality standards.
He/she designs new products or services and manages marketing campaigns.
What is TQM exactly?
The industrial revolution saw the realization that prices alone were not sufficient to sustain manufacturing companies. This led to the birth of quality. They needed to improve the quality and efficiency of their products if they were to be competitive.
Management developed Total Quality Management to address the need for improvement. It focused on all aspects of an organisation's performance. It included continuous improvement, employee involvement and customer satisfaction.
What is Six Sigma?
Six Sigma uses statistics to measure problems, find root causes, fix them, and learn from past mistakes.
The first step to solving the problem is to identify it.
Next, data is collected and analyzed to identify trends and patterns.
Then corrective actions are taken to solve the problem.
The data are then reanalyzed to see if the problem is solved.
This cycle will continue until the problem is solved.
Why is Six Sigma so popular?
Six Sigma is easy and can deliver significant results. It also provides a framework for measuring improvements and helps companies focus on what matters most.
Statistics
- The average salary for financial advisors in 2021 is around $60,000 per year, with the top 10% of the profession making more than $111,000 per year. (wgu.edu)
- As of 2020, personal bankers or tellers make an average of $32,620 per year, according to the BLS. (wgu.edu)
- Your choice in Step 5 may very likely be the same or similar to the alternative you placed at the top of your list at the end of Step 4. (umassd.edu)
- UpCounsel accepts only the top 5 percent of lawyers on its site. (upcounsel.com)
- The profession is expected to grow 7% by 2028, a bit faster than the national average. (wgu.edu)
External Links
How To
What is Lean Manufacturing?
Lean Manufacturing is a method to reduce waste and increase efficiency using structured methods. They were developed by Toyota Motor Corporation in Japan during the 1980s. The primary goal was to make products with lower costs and maintain high quality. Lean manufacturing eliminates unnecessary steps and activities from a production process. It consists of five basic elements: pull systems, continuous improvement, just-in-time, kaizen (continuous change), and 5S. Pull systems are able to produce exactly what the customer requires without extra work. Continuous improvement is the continuous improvement of existing processes. Just-in time refers to components and materials being delivered right at the place they are needed. Kaizen means continuous improvement. Kaizen involves making small changes and improving continuously. Finally, 5S stands for sort, set in order, shine, standardize, and sustain. These five elements are used together to ensure the best possible results.
Lean Production System
Six key concepts are the basis of lean production:
-
Flow is about moving material and information as near as customers can.
-
Value stream mapping is the ability to divide a process into smaller tasks, and then create a flowchart that shows the entire process.
-
Five S's, Sort, Set in Order, Shine. Standardize. and Sustain.
-
Kanban - visual cues such as stickers or colored tape can be used to track inventory.
-
Theory of constraints - identify bottlenecks in the process and eliminate them using lean tools like kanban boards;
-
Just-intime - Order components and materials at your location right on the spot.
-
Continuous improvement - incremental improvements are made to the process, not a complete overhaul.