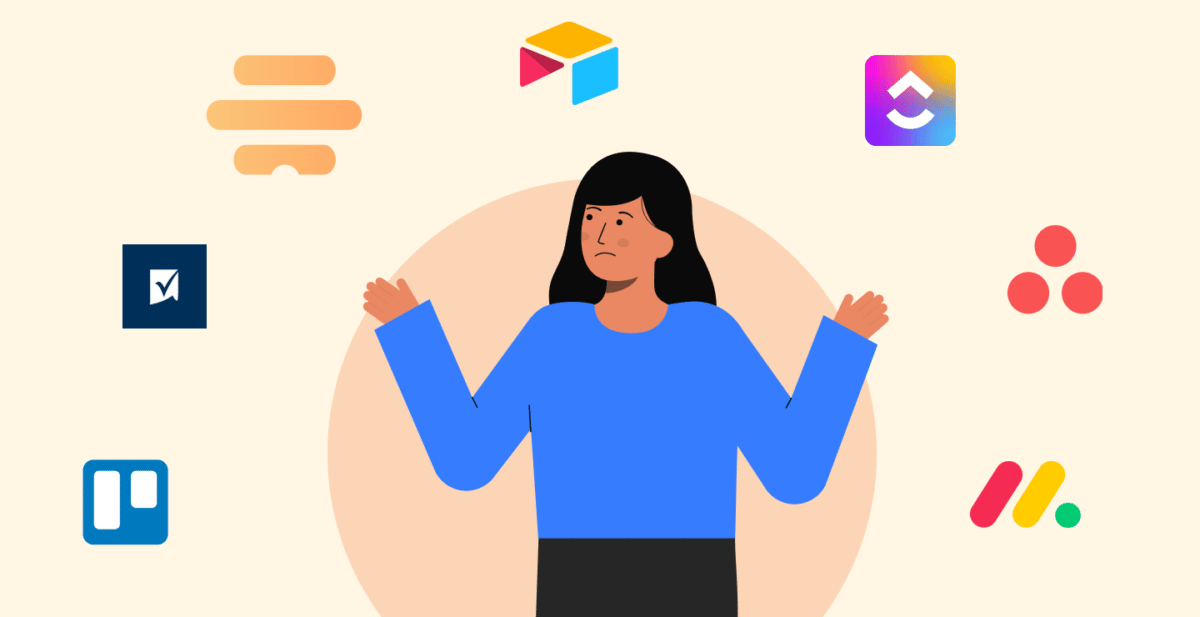
A common failure in managing risk is the lack of transparency. This was clearly demonstrated by the scandal surrounding coronavirus-related deaths. Data silos and a lack of data are other issues. Additionally, risk was not considered in the design of processes. Risk managers tend to settle for data they can access and ignore risks that could have negative consequences. This is a common problem and one that can be difficult to fix.
Negative risks
Managers can use five key risk management strategies to deal with threats and negative risks. These strategies depend on the kind of risk and the exposure level. They also depend on the probability of occurrence and the impact the risk will have on the project objectives. These strategies, which are the most effective, are used when risk is considered critical. When the risk is less critical, the transfer and accept strategy can be used.
Positive and negative risks affect people, processes, technology, and resources. If managed properly, even positive risks can produce positive results. A positive risk could result in a project being completed earlier than expected, or a higher return on investment. Negative risks can occur in any situation, and a negative risk may be avoided by implementing the right risk management practices. These risks pose problems and can cause delays and impact on project schedules, budgets, and schedules.
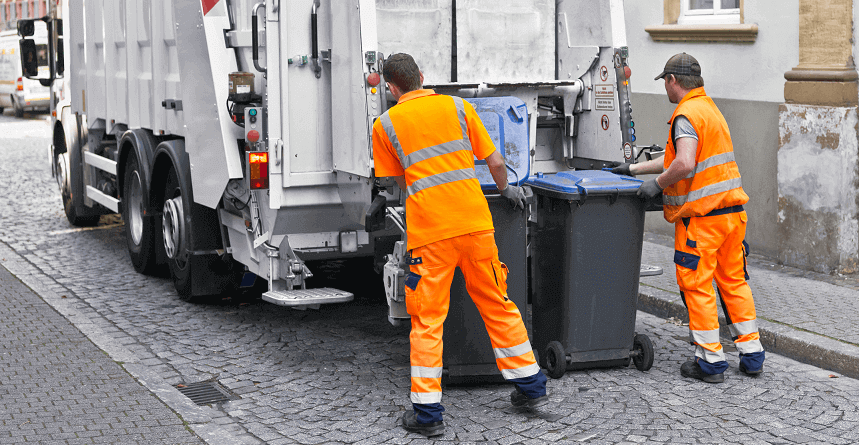
Communication
Communication is key to risk management. Whether it is through a formal document or a social media post, a professional's communication must be open and honest. Communication professionals can reduce the chance of misunderstanding the risk. Hurricane Harvey is a simple example of how to communicate risk. In 2017, Hurricane Harvey was a devastating hurricane that threatened Houston. Officials used social media, local and national media to inform residents of the danger to evacuate. It is important for professionals to point people to trustworthy sources to obtain information.
Poor communication is a major risk when managing projects. Poor communication can be fatal to a project. Communication can boost employee engagement as well as reduce miscommunications. Project managers should consider activities that increase communication in their project management risk assessments. Once the risk assessment has been completed, project managers are able to take steps to reduce it. This includes using a communication risk assessment tool and including stakeholders in the process.
Consultation
As part of the risk management process, an organisation must involve all stakeholders in the project. The stakeholders can range from internal and external partners to stakeholders that are not directly involved in the project. To ensure that all stakeholders are fully informed about the risks and expectations, it's important to include them in the risk management process. All stakeholders must be involved in the risk assessment, management and project team meetings to ensure adequate consultation. Here are some tips for ensuring that the consultation process involves all key stakeholders.
Risk management consultants will assist in prioritizing risks. This is crucial because the highest-risk risks need more immediate attention, while a lower-risk risk will need a more modest remediation strategy. Consultations can help organizations prioritize risks and create a risk management plan that best suits their needs. Consulting can help organizations identify risks and develop an action plan. This will improve risk management.
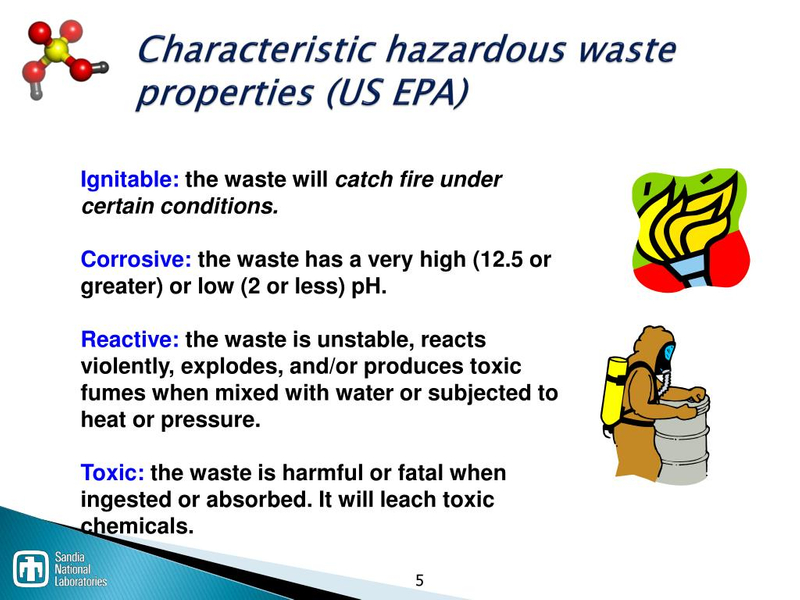
Top-down
There are obvious advantages and disadvantages to top-down management of risk. First, it requires a lot of time, effort, and expertise to set up. It can be very individualized, so what one manager may have learned in one industry may not work for another. It can be a powerful risk management tool. Although it is not widely used, it is growing in popularity. Here are some more reasons.
It is crucial to use top-down methods of risk management in the initial phases. The benefits of risk management at this stage are the greatest. Previous projects' experience can easily be applied. Top-down risk analysis, which incorporates evidence-based models and techniques that have been used in previous projects, can be a great way to improve management accountability. Top-down risk management techniques are a great way to reduce project risk if they are used correctly. Managers and teams can use them to meet their financial obligations.
FAQ
What are the main four functions of management
Management is responsible for organizing, managing, directing and controlling people, resources, and other activities. It includes the development of policies and procedures as well as setting goals.
Management is the ability to direct, coordinate, control, motivate, supervise, train, and evaluate an organization's efforts towards achieving its goals.
Management has four primary functions:
Planning - This is the process of deciding what should be done.
Organizing - Organizing involves deciding how things should be done.
Direction - This is the art of getting people to follow your instructions.
Controlling – Controlling is the process of ensuring that tasks are completed according to plan.
What is TQM and how can it help you?
The industrial revolution was when companies realized that they couldn't compete on price alone. This is what sparked the quality movement. They needed to improve quality and efficiency if they were going to remain competitive.
In response to this need for improvement, management developed Total Quality Management (TQM), which focused on improving all aspects of an organization's performance. It included continuous improvement and employee involvement as well as customer satisfaction.
What does it mean to say "project management"
We mean managing the activities involved in carrying out a project.
Our services include the definition of the scope, identifying requirements, preparing a budget, organizing project teams, scheduling work, monitoring progress and evaluating the results before closing the project.
What are management principles?
Management Concepts are the principles and practices managers use to manage people and resources. They cover topics like job descriptions (job descriptions), performance evaluations, training programmes, employee motivation and compensation systems.
Statistics
- This field is expected to grow about 7% by 2028, a bit faster than the national average for job growth. (wgu.edu)
- The BLS says that financial services jobs like banking are expected to grow 4% by 2030, about as fast as the national average. (wgu.edu)
- The average salary for financial advisors in 2021 is around $60,000 per year, with the top 10% of the profession making more than $111,000 per year. (wgu.edu)
- Our program is 100% engineered for your success. (online.uc.edu)
- UpCounsel accepts only the top 5 percent of lawyers on its site. (upcounsel.com)
External Links
How To
How can Lean Manufacturing be done?
Lean Manufacturing uses structured methods to reduce waste, increase efficiency and reduce waste. These processes were created by Toyota Motor Corporation, Japan in the 1980s. The main goal was to produce products at lower costs while maintaining quality. Lean manufacturing eliminates unnecessary steps and activities from a production process. It includes five main elements: pull systems (continuous improvement), continuous improvement (just-in-time), kaizen (5S), and continuous change (continuous changes). Pull systems are able to produce exactly what the customer requires without extra work. Continuous improvement involves constantly improving upon existing processes. Just-intime refers the time components and materials arrive at the exact place where they are needed. Kaizen is continuous improvement. This can be achieved by making small, incremental changes every day. Finally, 5S stands for sort, set in order, shine, standardize, and sustain. These five elements are combined to give you the best possible results.
Lean Production System
Six key concepts make up the lean manufacturing system.
-
Flow - focus on moving material and information as close to customers as possible;
-
Value stream mapping - break down each stage of a process into discrete tasks and create a flowchart of the entire process;
-
Five S's – Sort, Put In Order Shine, Standardize and Sustain
-
Kanban: Use visual signals such stickers, colored tape, or any other visual cues, to keep track your inventory.
-
Theory of Constraints - Identify bottlenecks in the process, and eliminate them using lean tools such kanban boards.
-
Just-in-time - deliver components and materials directly to the point of use;
-
Continuous improvement is making incremental improvements to your process, rather than trying to overhaul it all at once.