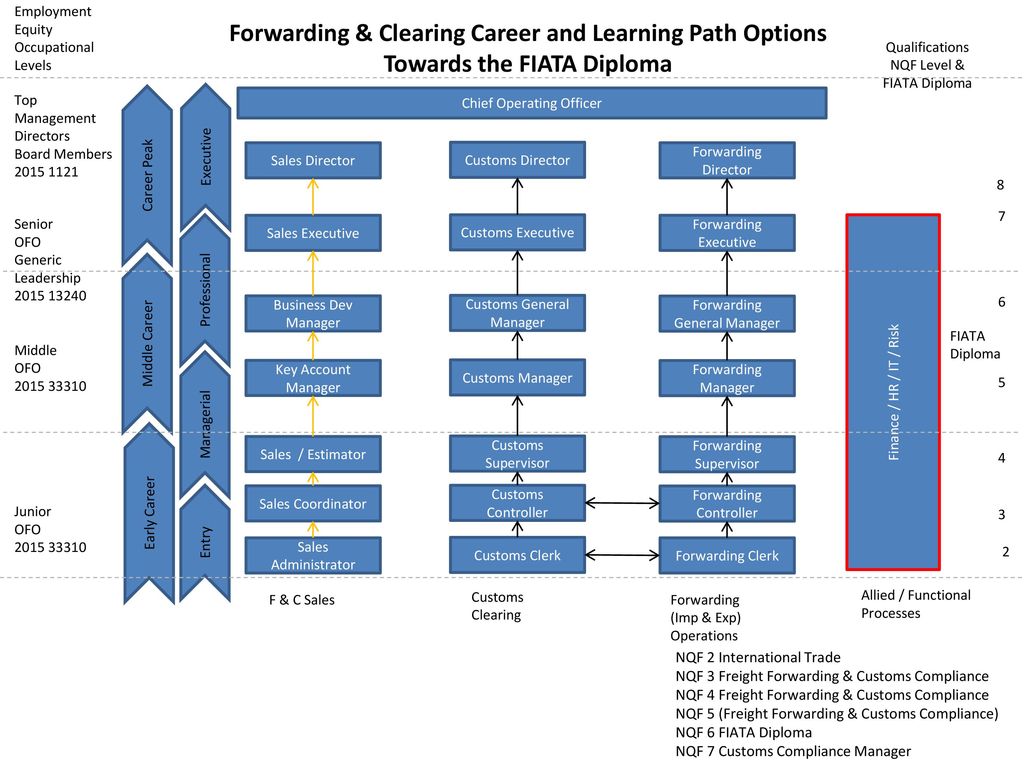
The inherent directionality of supply network networks is not captured by a business flow metric. A supply network is often composed of many levels and dependencies. Furthermore, a business flows metric doesn't capture the inherent directionality within information flows within a network. These are the issues that must be considered when developing a digital supply system.
Sustainability
Multinational corporations must ensure that supply networks are sustainable. Many companies have made sustainability their top priority and committed to using sustainable suppliers. Businesses face serious risks because many suppliers at lower levels don't adhere to sustainability standards. This article examines the supply chains of three multinational companies and provides best practices for businesses to overcome this problem. These include setting long term sustainability goals and including suppliers of lower tier in the sustainability strategy.
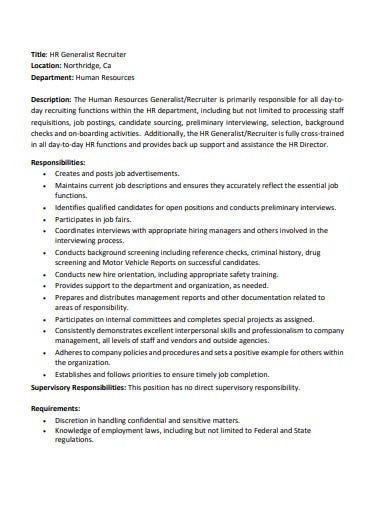
Companies should set goals and measure progress to show improvement in their supply chains. They must also involve all stakeholders in the supply chain, including internal staff who drive change and consumers. The goal should not be to prove the benefits to business of sustainable supply networks but to create the governance and organizational structures necessary to ensure that the sustainability efforts are a success.
Vertical disintegration of supply chains
The potential for vertical disintegration within supply chains can have several consequences for companies. Apart from the potential for greater costs and losses, it can also lead to changes in organisational structures and hierarchies. To increase their overall competitiveness and reduce their participation in upstream or downstream activities, some companies may consider this option. However, this approach is not always appropriate and should only be implemented in specific circumstances.
Vertical integration's main drawback is its limitation of flexibility. This is because vertical integration makes it conform to certain trends within a segment. A retailer might find it difficult to adopt a new technology when its competitors have already done so. To keep up with its competition, the parent company would need to invest in new technology. Integration can be complicated by rapidly changing technologies. It can also be expensive for companies to integrate different technologies in different parts of their supply chain.
Performance implications of a digital supply network
Digital supply chains can have many benefits. They are more efficient, resilient, and cost-savings. On the downside, they can also increase cybersecurity risks. However, there are many options companies have to minimize these risks. Let's take a closer look at some. These methods use data analytics. With this technology, businesses can gain insight into customer expectations and improve their products and services. Companies can also predict potential problems by incorporating data from many sources and make better decisions.
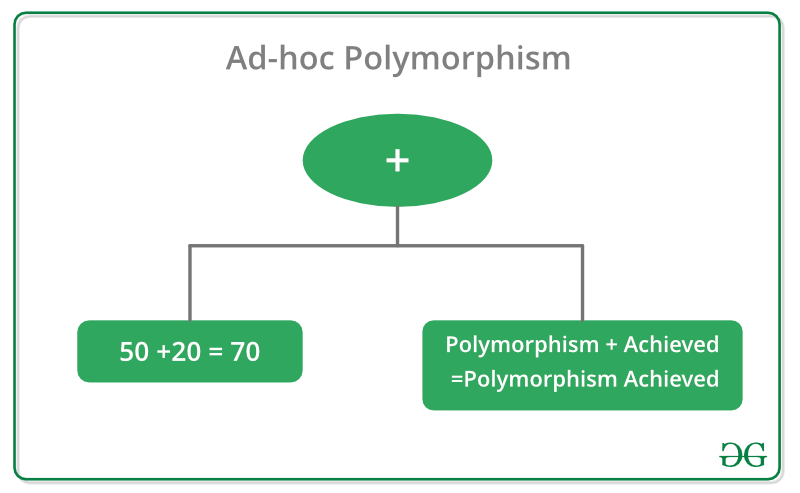
Your existing supply chain should be assessed before you can implement digitalization. This will help you identify and mitigate any risks or issues, as well any potential complications. Then, you can develop an action plan to minimize any risks. Collaboration with your partners is crucial once you have an idea of what you want from the digital supply chain. This will ensure that all stakeholders are satisfied with the digital supply chain.
FAQ
What are the five management process?
These five stages are: planning, execution monitoring, review and evaluation.
Setting goals for the future is part of planning. Planning involves defining your goals and how to get there.
Execution is the actual execution of the plans. These plans must be adhered to by everyone.
Monitoring is checking on progress towards achieving your objectives. Monitoring should include regular reviews of performance against goals and budgets.
At the end of every year, reviews take place. They provide an opportunity to assess whether everything went well during the year. If not then, you can make changes to improve your performance next year.
After the annual review, evaluation takes place. It helps identify which aspects worked well and which didn't. It provides feedback about how people perform.
How can a manager motivate his/her staff?
Motivation refers to the desire to perform well.
You can get motivated by doing something enjoyable.
You can also be motivated by the idea of making a difference to the success and growth of your organization.
You might find it more rewarding to treat patients than to study medical books if you plan to become a doctor.
A different type of motivation comes directly from the inside.
You may feel strongly that you are responsible to help others.
You may even find it enjoyable to work hard.
If you don't feel motivated, ask yourself why.
Next, think of ways you can improve your motivation.
What is TQM, exactly?
The industrial revolution was when companies realized that they couldn't compete on price alone. This is what sparked the quality movement. To remain competitive, they had to improve quality as well as efficiency.
Management developed Total Quality Management to address the need for improvement. It focused on all aspects of an organisation's performance. It included continuous improvement, employee involvement and customer satisfaction.
How can a manager improve his/her managerial skills?
It is important to have good management skills.
Managers must continuously monitor the performance levels of their subordinates.
You should immediately take action if you see that your subordinate is not performing as well as you would like.
It is important to be able identify areas that need improvement and what can be done to improve them.
What is the difference between project and program?
A project is temporary; a program is permanent.
Projects usually have a goal and a deadline.
It is usually done by a group that reports back to another person.
A program will usually have a set number of goals and objectives.
It is typically done by one person.
What is Six Sigma?
Six Sigma uses statistical analysis for problems to be found, measured, analyzed root causes, corrected, and learned from.
The first step to solving the problem is to identify it.
The data is then analyzed and collected to identify trends.
Then corrective actions are taken to solve the problem.
Finally, the data are reanalyzed in order to determine if it has been resolved.
This continues until the problem has been solved.
What does it mean to say "project management"
It refers to the management of activities related to a project.
We help you define the scope of your project, identify the requirements, prepare the budget, organize the team, plan the work, monitor progress and evaluate the results before closing down the project.
Statistics
- 100% of the courses are offered online, and no campus visits are required — a big time-saver for you. (online.uc.edu)
- This field is expected to grow about 7% by 2028, a bit faster than the national average for job growth. (wgu.edu)
- UpCounsel accepts only the top 5 percent of lawyers on its site. (upcounsel.com)
- As of 2020, personal bankers or tellers make an average of $32,620 per year, according to the BLS. (wgu.edu)
- The profession is expected to grow 7% by 2028, a bit faster than the national average. (wgu.edu)
External Links
How To
How is Lean Manufacturing done?
Lean Manufacturing is a method to reduce waste and increase efficiency using structured methods. These processes were created by Toyota Motor Corporation, Japan in the 1980s. The goal was to produce quality products at lower cost. Lean manufacturing emphasizes removing unnecessary steps from the production process. It consists of five basic elements: pull systems, continuous improvement, just-in-time, kaizen (continuous change), and 5S. It is a system that produces only the product the customer requests without additional work. Continuous improvement refers to continuously improving existing processes. Just-intime refers the time components and materials arrive at the exact place where they are needed. Kaizen stands for continuous improvement. Kaizen can be described as a process of making small improvements continuously. Five-S stands for sort. It is also the acronym for shine, standardize (standardize), and sustain. These five elements can be combined to achieve the best possible results.
Lean Production System
Six key concepts make up the lean manufacturing system.
-
Flow is about moving material and information as near as customers can.
-
Value stream mapping - Break down each stage in a process into distinct tasks and create an overview of the whole process.
-
Five S's: Sort, Shine Standardize, Sustain, Set In Order, Shine and Shine
-
Kanban - visual cues such as stickers or colored tape can be used to track inventory.
-
Theory of constraints: Identify bottlenecks and use lean tools such as kanban boards to eliminate them.
-
Just-in-time - deliver components and materials directly to the point of use;
-
Continuous improvement - Make incremental improvements rather than overhauling the entire process.