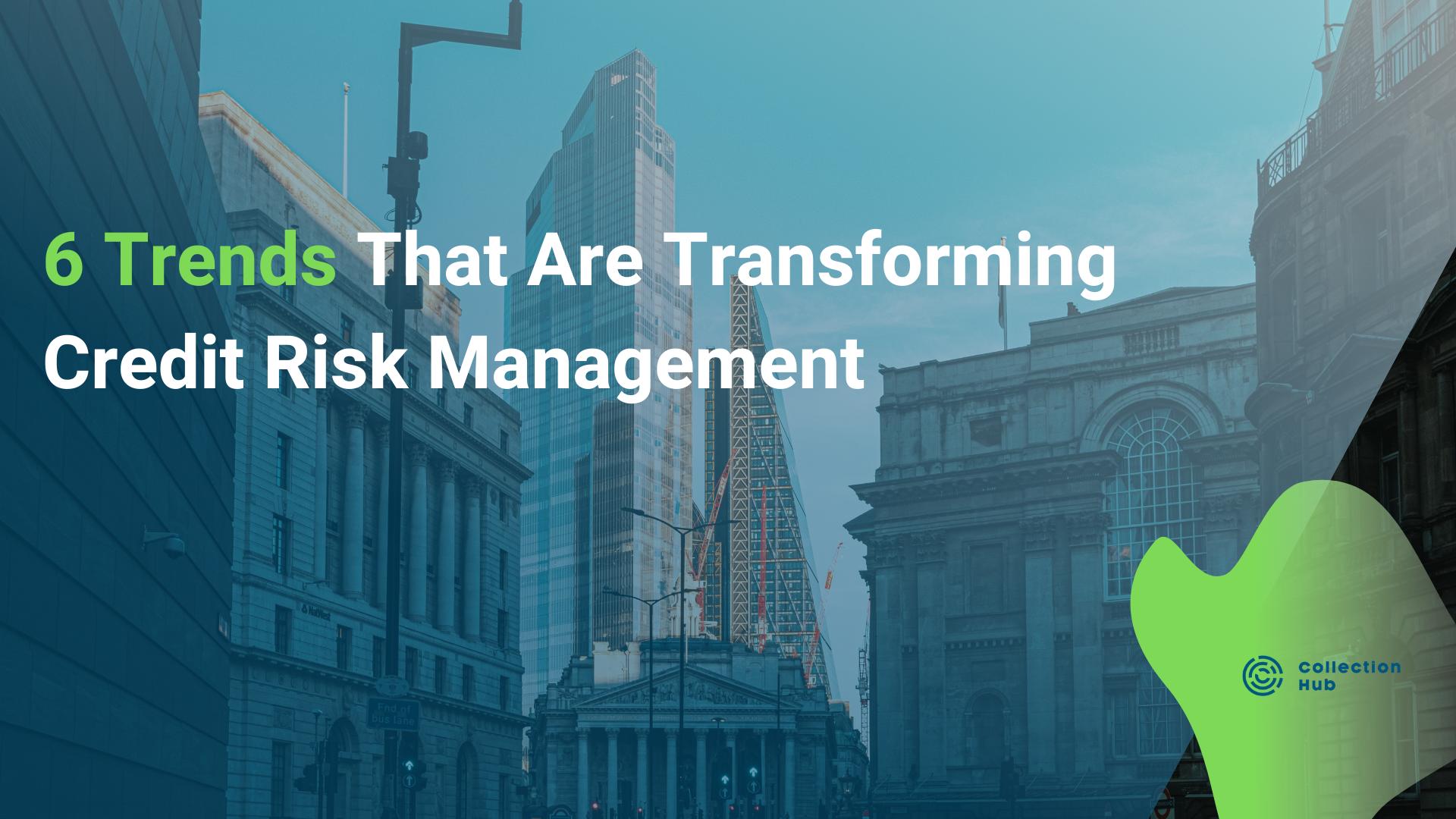
A company must adhere to 14 elements in order to be considered a PSM Program. These elements include process hazard analyses and permissible exposure limits. These requirements are critical for the effectiveness and efficiency of a PSM programme. Compliance will be achieved if the company adheres to these elements. The following sections will detail these elements and how they should be applied to your company.
Analyses of Process Hazards
An essential element of any safety management program is the process hazard analysis. It helps to identify possible hazards and determine the consequences of failure. This analysis should be performed by an experienced team. It will also include information about human factors and past incidents. The analysis must be reviewed every five years after it is completed. As part of a safety management program, the process of hazard analysis must also be implemented.
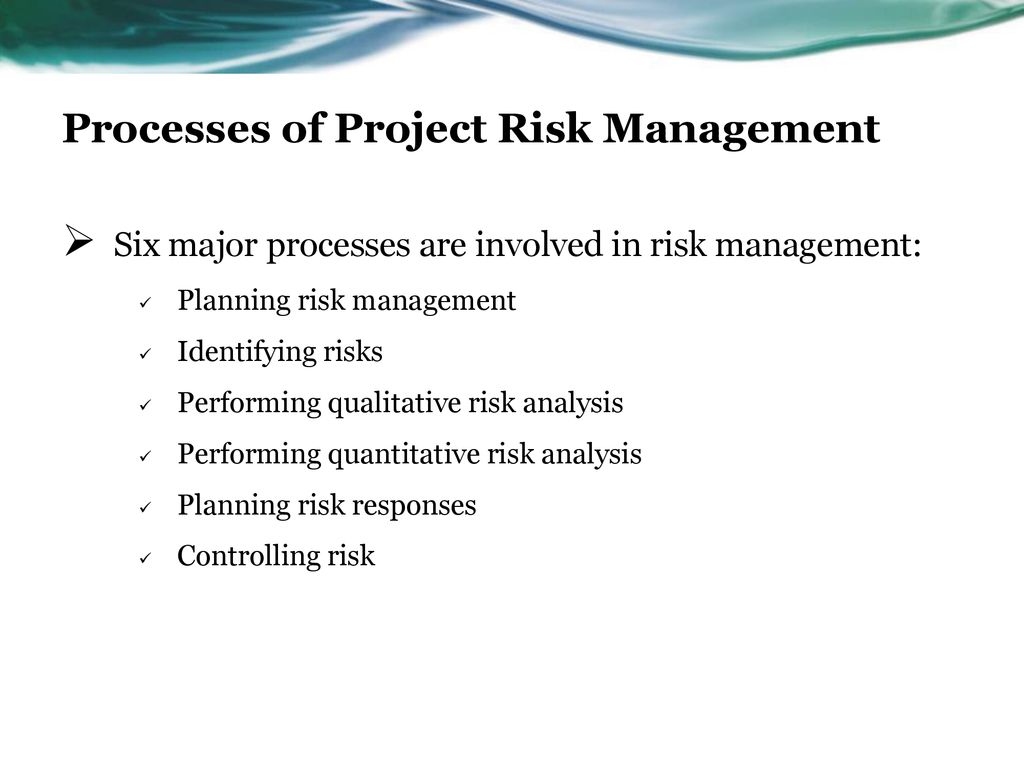
Permissible exposure limits
OSHA Process Safety Management is a set standard for hazardous chemical, gas, or liquid processes. The standard is applicable to businesses who produce or process dangerous chemicals. It does not cover hydrocarbon fuels used exclusively for workplace use, retail or well drilling. It also does not apply for facilities that are usually unoccupied or far away.
Physical data
PSM involves the assessment and management of hazardous products and materials. This involves knowing how to safely transport, store, and handle hazardous substances. This will result in less product waste and fewer workplace injuries. It facilitates decision-making and helps organizations prioritize safety and health. PSM is a vital part of a safe workplace. It can help companies prevent costly medical emergencies and save money.
Data on corrosivity
The PSM standard sets out requirements for how chemicals and other substances should be stored and handled. The PSM includes requirements for emergency actions plans and permit systems. It also requires periodic compliance audits. PSM-compliant work environments will prevent injuries and damage, regardless of whether hazardous substances were used in the production processes.
Thermal stability data
OSHA has established a standard for the collection and reporting of PSM thermal stability data. Researchers will be more aware of possible hazards and less likely to accidentally release. It will be reviewed frequently and revised to address the tasks of new research projects. It will be made available to all employees. It includes information about toxicity, reactivity and physical properties.
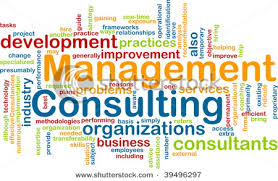
Employee participation clause
Process Safety Management (PSM), is a systematic and analytical approach to preventing process accidents due to highly hazardous chemicals (HHC). It is an important step in improving process safety and must be implemented at all levels, including maintenance and production. It contains 14 elements that should be implemented, including employee participation clauses. Below are some examples of these elements, along with their requirements.
FAQ
Six Sigma is so popular.
Six Sigma is easy and can deliver significant results. It also provides a framework for measuring improvements and helps companies focus on what matters most.
Why is it so important for companies that they use project management techniques
Project management techniques are used to ensure that projects run smoothly and meet deadlines.
Because most businesses depend heavily on project work to produce goods or services,
These projects require companies to be efficient and effective managers.
Companies that do not manage their projects effectively risk losing time, money, or reputation.
What are some common mistakes managers make when managing people?
Sometimes, managers make their job more difficult than it is.
They might not give enough support and delegate the right responsibilities to their staff.
Additionally, many managers lack communication skills that are necessary to motivate and direct their teams.
Some managers create unrealistic expectations for their teams.
Some managers may try to solve every problem themselves instead of delegating responsibility to others.
What are management concepts, you ask?
Management concepts are the fundamental principles and practices that managers use when managing people and their resources. They include such topics as human resource policies, job descriptions, performance evaluations, training programs, employee motivation, compensation systems, organizational structure, and many others.
What's the difference between Six Sigma and TQM?
The main difference between these two quality-management tools is that six-sigma concentrates on eliminating defects while total QM (TQM), focuses upon improving processes and reducing expenses.
Six Sigma can be described as a strategy for continuous improvement. This method emphasizes eliminating defects using statistical methods such p-charts, control charts, and Pareto analysis.
The goal of this method is to reduce variation in product output. This is accomplished by identifying the root cause of problems and fixing them.
Total quality management involves measuring and monitoring all aspects of the organization. It also involves training employees to improve performance.
It is often used to increase productivity.
Statistics
- The BLS says that financial services jobs like banking are expected to grow 4% by 2030, about as fast as the national average. (wgu.edu)
- UpCounsel accepts only the top 5 percent of lawyers on its site. (upcounsel.com)
- As of 2020, personal bankers or tellers make an average of $32,620 per year, according to the BLS. (wgu.edu)
- 100% of the courses are offered online, and no campus visits are required — a big time-saver for you. (online.uc.edu)
- Hire the top business lawyers and save up to 60% on legal fees (upcounsel.com)
External Links
How To
How is Lean Manufacturing done?
Lean Manufacturing techniques are used to reduce waste while increasing efficiency by using structured methods. They were created in Japan by Toyota Motor Corporation during the 1980s. It was designed to produce high-quality products at lower prices while maintaining their quality. Lean manufacturing seeks to eliminate unnecessary steps and activities in the production process. It is composed of five fundamental elements: continuous improvement; pull systems, continuous improvements, just-in–time, kaizen, continuous change, and 5S. Pull systems are able to produce exactly what the customer requires without extra work. Continuous improvement means continuously improving on existing processes. Just-in-time is when components and other materials are delivered at their destination in a timely manner. Kaizen means continuous improvement, which is achieved by implementing small changes continuously. The 5S acronym stands for sort in order, shine standardize and maintain. These five elements can be combined to achieve the best possible results.
Lean Production System
The lean production system is based on six key concepts:
-
Flow - focuses on moving information and materials as close to customers as possible.
-
Value stream mapping is the ability to divide a process into smaller tasks, and then create a flowchart that shows the entire process.
-
Five S's - Sort, Set In Order, Shine, Standardize, and Sustain;
-
Kanban - use visual signals such as colored tape, stickers, or other visual cues to keep track of inventory;
-
Theory of constraints: Identify bottlenecks and use lean tools such as kanban boards to eliminate them.
-
Just-in Time - Send components and material directly to the point-of-use;
-
Continuous improvement: Make incremental improvements to the process instead of overhauling it completely.