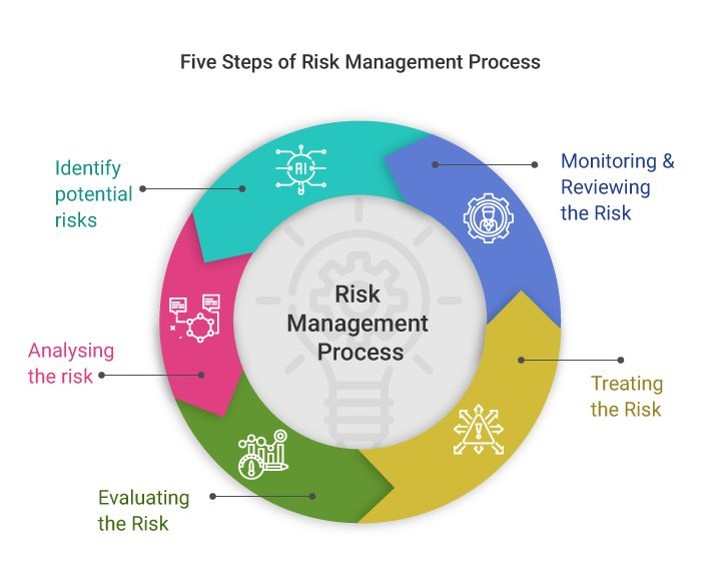
It is important to accept risk when running a business. The idea behind balancing the unknown and known risks to a business is to achieve a balanced approach. The risks are natural causes, aggressive competitor, credit risk and legal obligations. There is also uncertainty in the financial market. These risks will have a significant impact on a business's success, so it is important to understand how to deal with them.
Avoiding risks
To reduce risks, it is essential to combine technology with policies and procedures. Employee training can be an integral part in risk management. By acknowledging and minimizing risks, organizations can reduce the cost of project failure. It can be hard and time-consuming to avoid risk.
Enterprise executives should implement policies and technology to mitigate risks. Enterprise executives will accept the most common risk: one that has minimal financial impact, little potential and is low in cost. But, this type of risk is often not suitable for all situations.
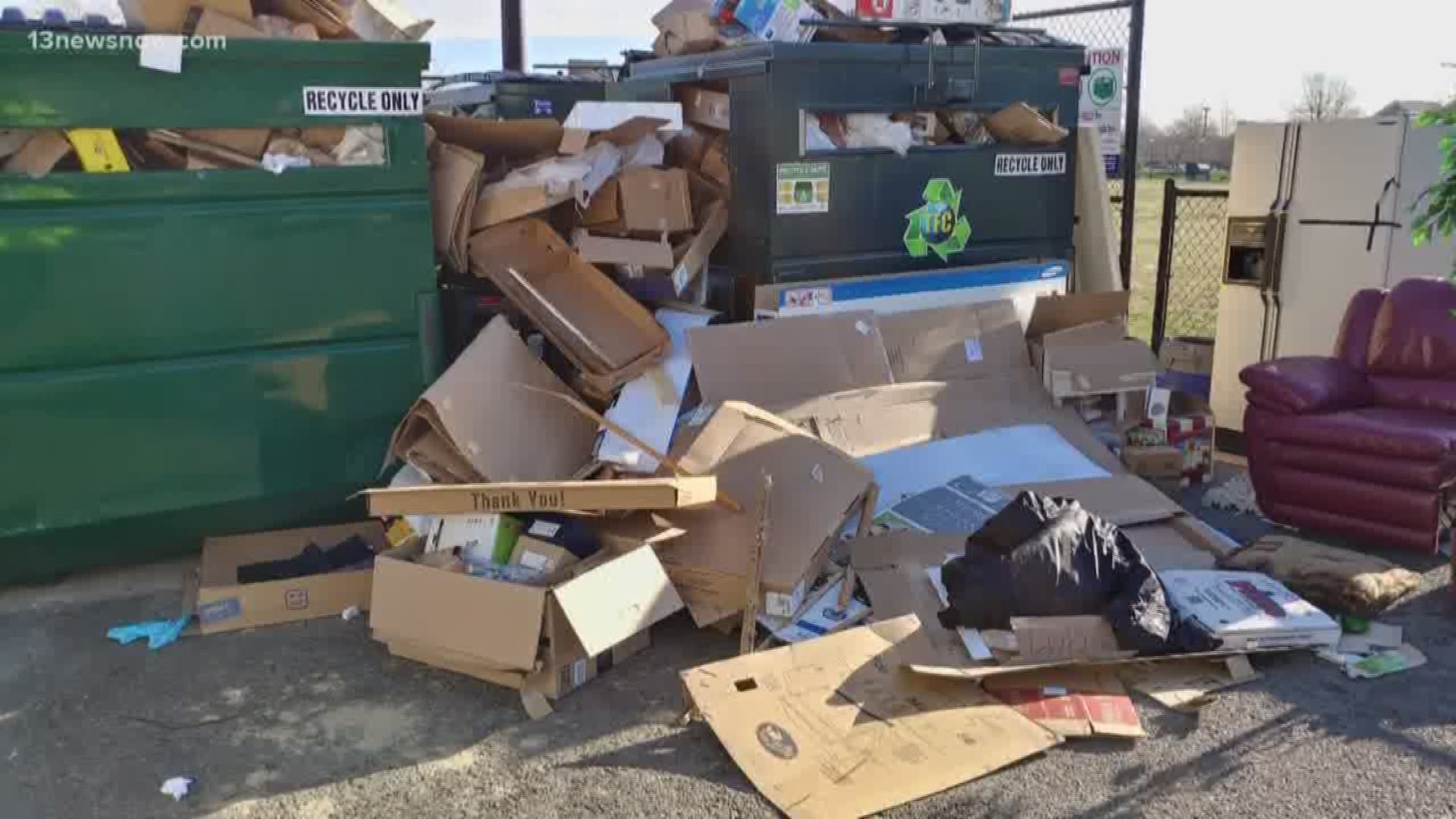
Mitigating risks
Before you choose a risk management strategy for your business, it is important that you carefully consider the possible consequences. Once you know what risks are most likely to occur, you can choose between mitigating them or accepting them. Testing and developing controls are key to mitigating risks. You must ensure your plan is effective and in compliance with the business environment once it has been established.
Companies must decide which risks are most likely to affect their operations before they will accept them. After deciding which risks are most dangerous, companies allocate funds to pay them. This includes insurance coverage for their buildings, stocks and employees.
Limiting risks
Limiting risks is a fundamental principle in risk management. It is about defining your risk appetite and setting limits in accordance with your business model. Limiting risks offers flexibility for the risk taker and the market environment, both of which are constantly changing. This concept can help you make informed business decisions that will protect you and your company.
There are many risk factors that could lead to financial loss, such as overly aggressive competition and exchange rates. There is also credit risk. Accepting risks is the same as self-insurance. While companies may be willing to accept risk as a way to save money they might also be betting that they will have large expenses in the future.
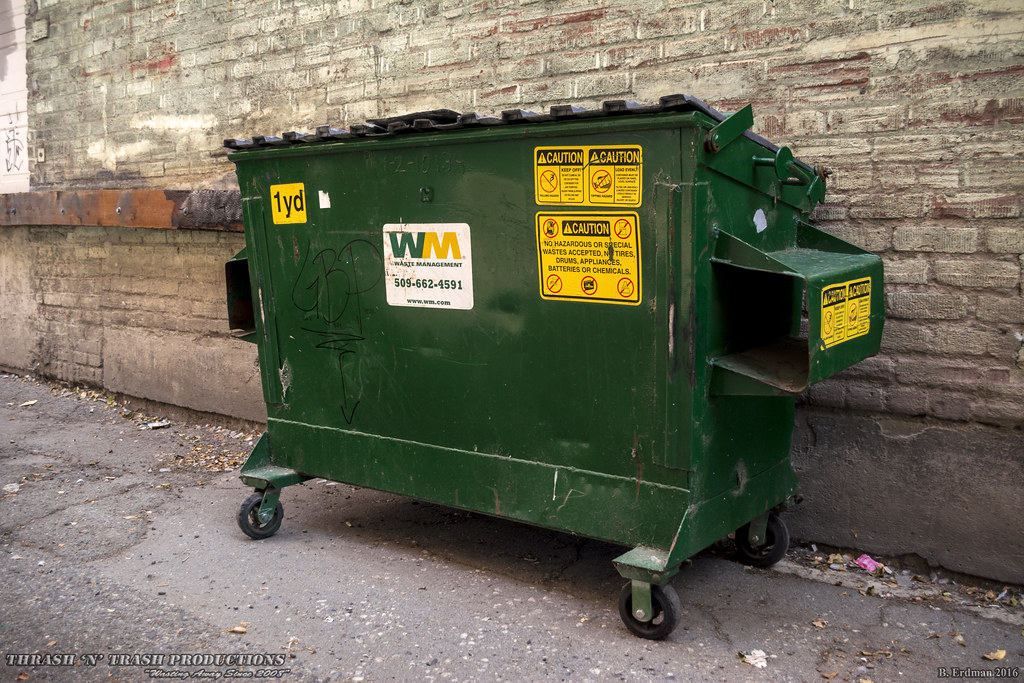
Accepting risks
Accepting risk in business is about being open to potential threats and ready to address them. It involves many strategies. Companies need to identify the most pressing threats, rank them according priority, and determine the appropriate level risk management. For example, an organization may need to address legal obligations, deal with project failures, or adjust corporate policies or communication plans.
When the risks are low or rare, risk acceptance can help reduce insurance premiums. This type is helpful for setting priorities and budgets.
FAQ
What are the 5 management processes?
Each business has five stages: planning, execution and monitoring.
Setting goals for the future is part of planning. It involves setting goals and making plans.
Execution is when you actually execute the plans. It is important to ensure that everyone follows the plans.
Monitoring is checking on progress towards achieving your objectives. Regular reviews should be done of your performance against targets or budgets.
Each year, reviews are held at the end. They give you an opportunity to review the year and assess how it went. If not, it is possible to make improvements for next year.
After each year's review, evaluation occurs. It helps identify what worked well and what didn't. It also provides feedback on how well people performed.
How does a manager motivate their employees?
Motivation is the desire to do well.
You can get motivated by doing something enjoyable.
You can also be motivated by the idea of making a difference to the success and growth of your organization.
If you are a doctor and want to be one, it will likely be more rewarding to see patients than to read medical books every day.
A different type of motivation comes directly from the inside.
You might feel a strong sense for responsibility and want to help others.
You may even find it enjoyable to work hard.
If you don’t feel motivated, find out why.
You can then think of ways to improve your motivation.
What do we mean when we say "project management"?
This refers to managing all activities that are involved in a project's execution.
These include planning the scope and identifying the needs, creating the budget, organizing the team, scheduling the work and monitoring progress. Finally, we close down the project.
What is Six Sigma?
It's a strategy for quality improvement that emphasizes customer care and continuous learning. This is an approach to quality improvement that uses statistical techniques to eliminate defects.
Motorola created Six Sigma as part of their efforts to improve manufacturing processes in 1986.
The idea quickly spread in the industry. Many organizations today use six-sigma methods to improve product design and production, delivery and customer service.
Statistics
- Hire the top business lawyers and save up to 60% on legal fees (upcounsel.com)
- 100% of the courses are offered online, and no campus visits are required — a big time-saver for you. (online.uc.edu)
- The average salary for financial advisors in 2021 is around $60,000 per year, with the top 10% of the profession making more than $111,000 per year. (wgu.edu)
- As of 2020, personal bankers or tellers make an average of $32,620 per year, according to the BLS. (wgu.edu)
- The BLS says that financial services jobs like banking are expected to grow 4% by 2030, about as fast as the national average. (wgu.edu)
External Links
How To
How is Lean Manufacturing done?
Lean Manufacturing techniques are used to reduce waste while increasing efficiency by using structured methods. They were created by Toyota Motor Corporation in Japan in the 1980s. It was designed to produce high-quality products at lower prices while maintaining their quality. Lean manufacturing seeks to eliminate unnecessary steps and activities in the production process. It consists of five basic elements: pull systems, continuous improvement, just-in-time, kaizen (continuous change), and 5S. It is a system that produces only the product the customer requests without additional work. Continuous improvement is constantly improving upon existing processes. Just-in time refers to components and materials being delivered right at the place they are needed. Kaizen is continuous improvement. This can be achieved by making small, incremental changes every day. Last but not least, 5S is for sort. These five elements are used together to ensure the best possible results.
Lean Production System
Six key concepts form the foundation of the lean production system:
-
Flow is about moving material and information as near as customers can.
-
Value stream mapping- This allows you to break down each step of a process and create a flowchart detailing the entire process.
-
Five S’s - Sorted, In Order. Shine. Standardize. And Sustain.
-
Kanban – visual signals like colored tape, stickers or other visual cues are used to keep track inventory.
-
Theory of constraints: identify bottlenecks in your process and eliminate them using lean tools, such as kanban board.
-
Just-in-time - deliver components and materials directly to the point of use;
-
Continuous improvement - incremental improvements are made to the process, not a complete overhaul.