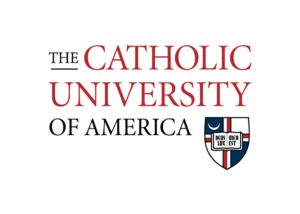
Expanding the supply network is the next logical step in healthcare delivery. The supply must be extended beyond the hospital walls and must include last-mile transportation. Telemedicine, at home testing kits, and Telehealth will all require that the healthcare supply chain extends beyond the hospital. This article looks at some of the key indicators of a healthy supply chain.
Indicators of supply chain performance
Supply chain management is essential as it plays an important role in healthcare facilities. Key Performance Indicators or KPIs are an excellent tool that can help track progress and improve internal decision-making. KPIs are available at all levels of an organisation, from doctors to nurses. This paper examines the relative importance and validation of KPIs related to healthcare.
How well supply chains support patient care is key to the success of healthcare supply chains. Hospitals can improve many aspects of their patient care by using the data provided to them by supply chain managers. They can also improve patient safety by ensuring that the treatment process runs smoothly.
Reliability and stability of the supply chains
Reliability is a key aspect of logistics in healthcare. This reliability can depend on the context and be crucial in meeting patient requirements and maintaining continuity of care. A reliable supply chain is critical to ensure that patients and services are always available in hospitals, clinics, as well as other medical facilities.
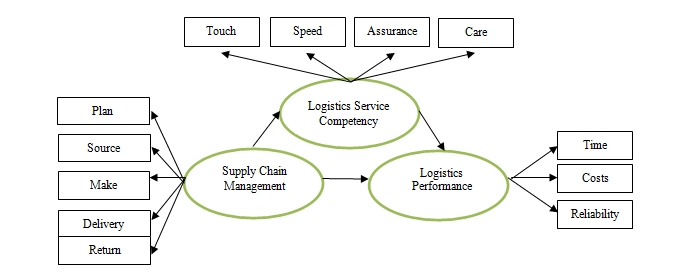
Reliability in healthcare can be measured by assessing three key elements: timeliness, effectiveness, and patient focus. It is crucial that these processes are able to deliver the necessary medication to the correct place at the right time without compromising the patient's health. In addition to these three factors, the reliability of a healthcare supply chain must be linked to a patient-centric approach and integrated action.
Interconnectivity
Health care is an industry that can greatly benefit from increased interconnectivity. It can facilitate fast, same day delivery for patients and immediate access to medical services. The supply chain can make this dream a reality. Companies are addressing patient-centric needs by developing innovative solutions for direct-to-consumer delivery and flexible last-mile processes.
Improving health care delivery is an imperative in the fight against emerging diseases and to promote the health of the population. Many healthcare organizations are trying to improve processes and resource efficiency in order to decrease costs and increase efficiency. They are also focusing on building and fostering integrated operations that involve all the key stakeholders. Research on healthcare has increased exponentially in recent years. This has resulted in a self-sustaining discipline in operations.
Entry points
There are several challenges that plague the supply chain of healthcare products. Misalignment in incentives is one example. The healthcare industry faces increasing costs, increasing regulations, and more. Healthcare organizations need to have greater visibility into the goods they buy and ship in order to overcome these challenges. These organizations must form strategic partnerships to address these issues.
A healthcare supply chain is a network of interrelated relationships that helps provide superior customer value at lower prices. The supply chain begins with the manufacturer of the medicine. It then moves through the distribution centers and hospitals. Hospitals have the option to purchase medicine directly from the manufacturer, or through a distributor. Distributors buy medicines in bulk and keep a large supply of medicines at their locations.
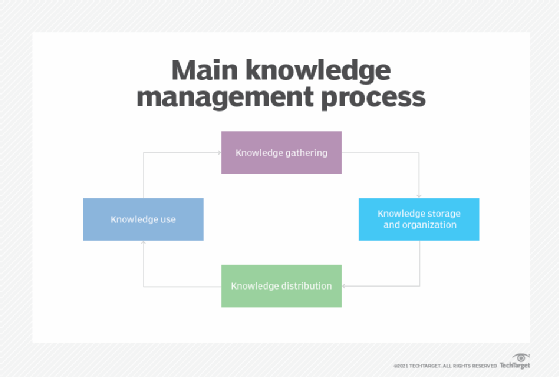
Human capital
Human capital is essential to the supply chain of healthcare. It manages the workforce, the quality of services, and the people who use it. This asset can be valuable if managed well. With the right systems in place, it will increase the success of businesses and maximize the value of the workforce.
Human capital management is an assortment of organizational practices that aim to build and maintain employee engagement. Employee engagement is critical to the success of a company and can be measured using a variety if measures. Gallup reports that highly engaged business units experience 40% fewer quality incidents, achieve 10 percent higher customer metrics, and achieve 20% higher sales.
FAQ
It seems so difficult sometimes to make sound business decisions.
Complex systems and many moving parts make up businesses. People who manage them have to balance multiple priorities while dealing with complexity and uncertainty.
Understanding the impact of these factors on the system is crucial to making sound decisions.
You need to be clear about the roles and responsibilities of each system. It's important to also consider how they interact with each other.
Also, you should ask yourself if there have been any assumptions in your past behavior. You might consider revisiting them if they are not.
You can always ask someone for help if you still have questions after all of this. They might have different perspectives than you, and could offer insight that could help you solve your problem.
How do you effectively manage employees?
The key to effective management of employees is ensuring their happiness and productivity.
It means setting clear expectations for them and keeping an eye on their performance.
To do this successfully, managers need to set clear goals for themselves and for their teams.
They must communicate clearly with their staff. They also need to make sure that they discipline and reward the best performers.
They will also need to keep records about their team's activities. These include:
-
What did you accomplish?
-
How much work was put in?
-
Who did it?
-
When it was done?
-
Why did it happen?
This data can be used to evaluate and monitor performance.
How can we create a culture of success in our company?
Successful company culture is one where people feel valued and respected.
It's built on three fundamental principles:
-
Everyone has something to contribute
-
People are treated fairly
-
There is mutual respect between individuals and groups
These values are reflected in the way people behave. They will treat others with respect and kindness.
They will respect the opinions of others.
They will also encourage others to share their ideas and feelings.
Company culture also encourages open communication, collaboration, and cooperation.
People feel safe to voice their opinions without fear of reprisal.
They know that they will not be judged if they make mistakes, as long as the matter is dealt with honestly.
The company culture encourages honesty and integrity.
Everyone knows that they must always tell truth.
Everyone understands there are rules that they must follow.
Everyone does not expect to receive special treatment.
What kind of people use Six Sigma
Six Sigma will most likely be familiar to people who have worked in statistics and operations research. It can be used by anyone in any business aspect.
It is a commitment-intensive task that requires strong leadership skills.
What is the difference in Six Sigma and TQM?
The key difference between the two quality management tools is that while six-sigma focuses its efforts on eliminating defects, total quality management (TQM), focuses more on improving processes and reducing cost.
Six Sigma is an approach for continuous improvement. It emphasizes the elimination and improvement of defects using statistical methods, such as control charts, P-charts and Pareto analysis.
This method has the goal to reduce variation of product output. This is achieved by identifying and addressing the root causes of problems.
Total quality management is the measurement and monitoring of all aspects within an organization. It also involves training employees to improve performance.
It is often used to increase productivity.
What does "project management" mean?
That is the management of all activities associated with a project.
This includes defining the scope, identifying the requirements and preparing the budget. We also organize the project team, schedule the work, monitor progress, evaluate results, and close the project.
Statistics
- UpCounsel accepts only the top 5 percent of lawyers on its site. (upcounsel.com)
- The average salary for financial advisors in 2021 is around $60,000 per year, with the top 10% of the profession making more than $111,000 per year. (wgu.edu)
- As of 2020, personal bankers or tellers make an average of $32,620 per year, according to the BLS. (wgu.edu)
- Hire the top business lawyers and save up to 60% on legal fees (upcounsel.com)
- Our program is 100% engineered for your success. (online.uc.edu)
External Links
How To
How do you apply the Kaizen method to your life?
Kaizen means continuous improvement. This term was first used by Toyota Motor Corporation in the 1950s. It refers to the Japanese philosophy that emphasizes continuous improvement through small incremental changes. It's a team effort to continuously improve processes.
Kaizen, a Lean Manufacturing method, is one of its most powerful. This concept requires employees to identify and solve problems during manufacturing before they become major issues. This improves the quality of products, while reducing the cost.
Kaizen is about making everyone aware of the world around them. To prevent problems from happening, any problem should be addressed immediately. If someone is aware of a problem at work, he/she should inform his/her manager immediately.
Kaizen is based on a few principles. The end product is always our starting point and we work toward the beginning. In order to improve our factory's production, we must first fix the machines producing the final product. Next, we repair the machines that make components. Then, the machines that make raw materials. And finally, we fix the workers who work directly with those machines.
This is why it's called "kaizen" because it works step-by-step to improve everything. After we're done with the factory, it's time to go back and fix the problem.
Before you can implement kaizen into your business, it is necessary to learn how to measure its effectiveness. There are many ways you can determine if kaizen has been implemented well. One of these ways is to check the number of defects found on the finished products. Another way is to check how much productivity has grown since kaizen was implemented.
A good way to determine whether kaizen has been implemented is to ask why. You were trying to save money or obey the law? Did you really believe it would lead to success?
Congratulations! You are now ready to begin kaizen.