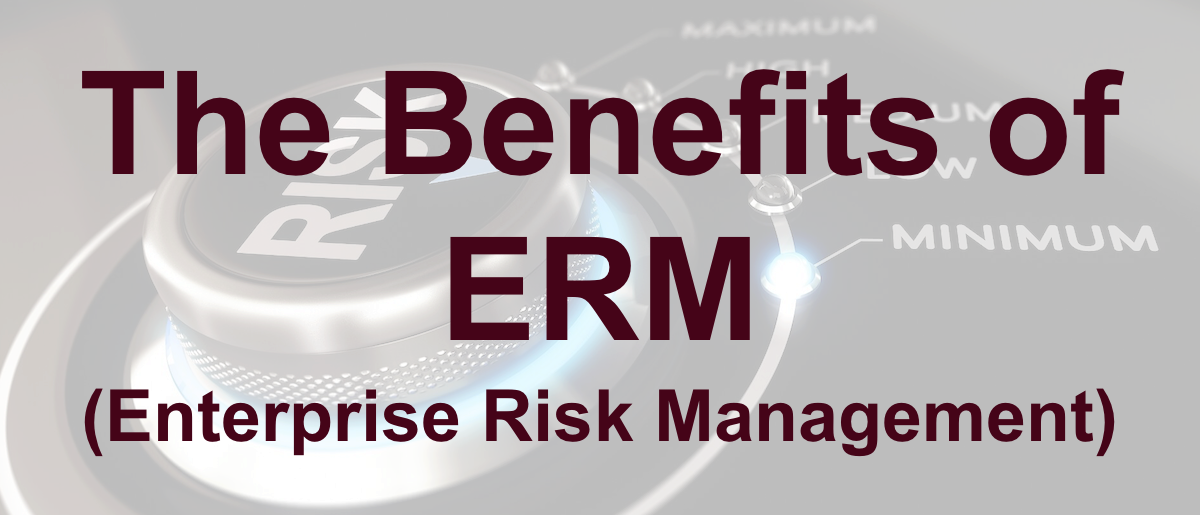
The five essential elements of supply chain success are: These elements include collaboration, cost reduction, managing upstream and downstream business issues, and working with suppliers. Identifying and implementing each of these elements is vital for supply chain success. Additionally, supply chain success is affected by government and regulatory agencies.
Five strategic elements to ensure supply chain success
A company's success depends on its supply chain management, particularly if it wants to fulfill customer expectations. Your supply chain strategy should be based on customer needs in order to achieve this. This basically means that the fulfillment experience must match the brand's promises. If a brand promises quick delivery, it must be capable of fulfilling that promise. Customers are also attracted to the smallest details. Customers value thoughtfulness which shows the thought process behind the brand.
Supply chain success must address supplier issues. For example, if a supplier has to pay tariffs, that can cause delays. These delays can be avoided by finding alternative suppliers or buying bulk before tariffs go into effect. These delays can be overcome by a supply chain solution. These software solutions can give accurate information about inventory levels and movement as well as future inventory needs.
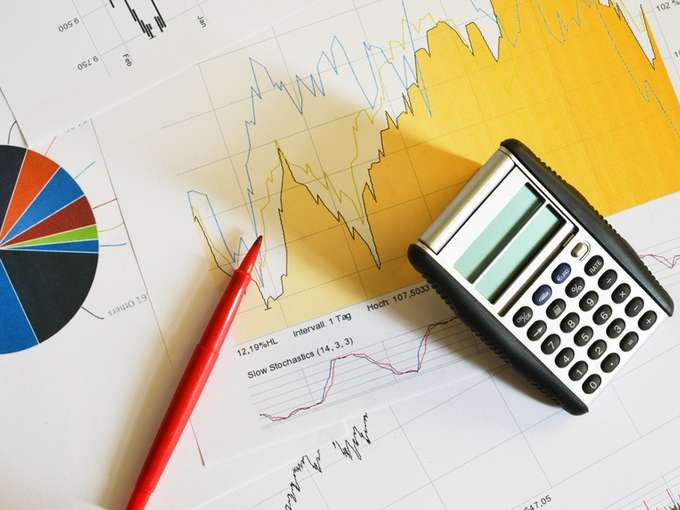
Supply chain success can be influenced by regulatory and government bodies
Many factors impact supply chain success. These include government policies and regulations. The United States government spends federal dollar to encourage domestic capacity and develop overseas markets. While simultaneously encouraging collaboration mechanisms between domestic companies, foreign countries are also supported. These mechanisms may be private, public, or cross-government. These efforts are meant to assist companies with their dual goals, which depend on a strong and trusted global supply chain.
In the healthcare industry, this is especially important, as the needs of patients and staff can influence the flow of healthcare supplies. Some hospitals might need to have the right size gloves in stock, while others may require specialized medical products. Finance managers may also want to cut healthcare costs by reducing out-of date products. Others may prefer certain brands or types. The lack of coordination and alignment of incentives can disrupt the flow of supply chains.
Collaboration with suppliers
Supply chain collaboration is when a company works with suppliers in order to improve its procurement efficiency. It can bring both benefits and a lot of value to both parties. Collaboration is more flexible and creates value for both companies than the traditional customer/supplier partnership. Companies can also view their suppliers and collaborate with them to achieve competitive advantage.
A supply chain's success is dependent on the collaboration of suppliers. Each party must find ways to improve the relationship between them in order to maximize collaboration's value. This can be achieved by having regular meetings with all your suppliers. This will allow them to voice their concerns and give constructive feedback.
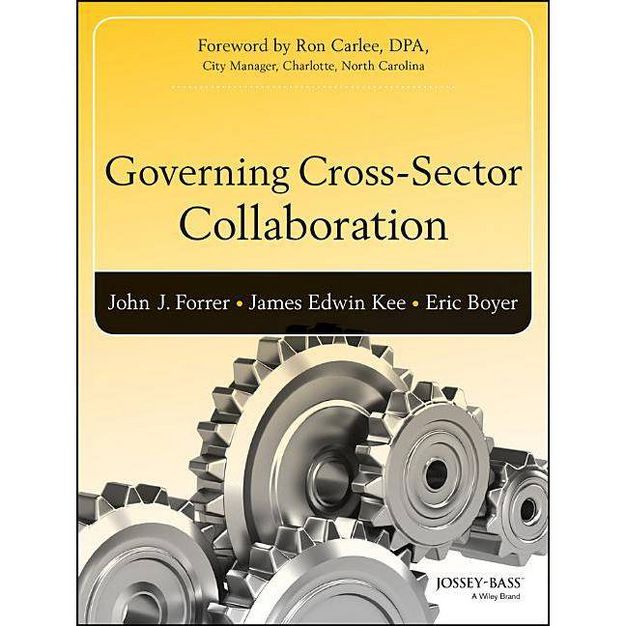
Managing upstream and downstream business issues
Supply chain management consists of integrating a variety of processes and tasks, with a focus on delivering value to customers and other stakeholders. There are many issues involved, including operational, reputational and legal risks. These issues can have a direct effect on the success and sustainability of a supply chain.
Supply chain management professionals must understand and anticipate the main issues impacting their business and develop robust management plans. They must also build strong contracts and work with customers and suppliers to resolve potential problems before they occur. In order to respond to increasing complexity and global economic instability, supply chain managers must be proactive and alert. In some cases, tariffs may be imposed on trade routes by political circumstances. This could lead to increased costs and longer processing times for customs, as well slowing down international shipping.
FAQ
What is the difference between Six Sigma Six Sigma and TQM?
The major difference between the two tools for quality management is that six Sigma focuses on eliminating defect while total quality control (TQM), on improving processes and decreasing costs.
Six Sigma is an approach for continuous improvement. It emphasizes the elimination of defects by using statistical methods such as control charts, p-charts, and Pareto analysis.
This method has the goal to reduce variation of product output. This is accomplished by identifying the root cause of problems and fixing them.
Total Quality Management involves monitoring and measuring every aspect of the organization. It also includes the training of employees to improve performance.
It is commonly used as a strategy for increasing productivity.
What is the difference of a program and project?
A project is temporary; a program is permanent.
A project usually has a specific goal and deadline.
It is often carried out by a team of people who report back to someone else.
A program usually has a set of goals and objectives.
It is usually done by one person.
What are the key management skills?
Managerial skills are crucial for every business owner, regardless of whether they run a small store in their locality or a large corporation. They include the ability to manage people, finances, resources, time, and space, as well as other factors.
These skills are necessary for setting goals and objectives as well as planning strategies, leading groups, motivating employees and solving problems.
As you can see, there's no end to the list of managerial duties!
What is TQM, exactly?
The industrial revolution led to the birth and growth of the quality movement. Manufacturing companies realized they couldn't compete solely on price. To remain competitive, they had to improve quality as well as efficiency.
Management developed Total Quality Management to address the need for improvement. It focused on all aspects of an organisation's performance. It included continuous improvement, employee involvement and customer satisfaction.
Statistics
- Your choice in Step 5 may very likely be the same or similar to the alternative you placed at the top of your list at the end of Step 4. (umassd.edu)
- Our program is 100% engineered for your success. (online.uc.edu)
- The BLS says that financial services jobs like banking are expected to grow 4% by 2030, about as fast as the national average. (wgu.edu)
- UpCounsel accepts only the top 5 percent of lawyers on its site. (upcounsel.com)
- The average salary for financial advisors in 2021 is around $60,000 per year, with the top 10% of the profession making more than $111,000 per year. (wgu.edu)
External Links
How To
How can you create a Quality Management Plan, (QMP)?
The Quality Management Plan (QMP) was established in ISO 9001. It is a systematic way to improve processes, products and services. It emphasizes on how to continuously measure, analyze, control, and improve processes, product/service, and customer satisfaction.
QMP is a standard way to improve business performance. QMP is a standard method that improves the production process, service delivery, customer relationship, and overall business performance. QMPs should encompass all three components - Products and Services, as well as Processes. When the QMP includes only one aspect, it is called a "Process" QMP. QMPs that focus on a Product/Service are known as "Product" QMPs. QMP is also used to refer to QMPs that focus on customer relations.
Scope, Strategy and the Implementation of a QMP are the two major elements. These elements are as follows:
Scope: This describes the scope and duration for the QMP. This scope can be used to determine activities for the first six-months of implementation of a QMP in your company.
Strategy: This is the description of the steps taken to achieve goals.
A typical QMP is composed of five phases: Planning Design, Development, Implementation and Maintenance. The following describes each phase.
Planning: In this stage the QMP's objectives and priorities are established. To understand the expectations and requirements of all stakeholders, the project is consulted. The next step is to create the strategy for achieving those objectives.
Design: In this stage, the design team designs the vision and mission, strategies, as well as the tactics that will be required to successfully implement the QMP. These strategies are then put into practice by creating detailed plans.
Development: Here, the development team works towards building the necessary capabilities and resources to support the implementation of the QMP successfully.
Implementation: This refers to the actual implementation or the use of the strategies planned.
Maintenance: Maintaining the QMP over time is an ongoing effort.
Additionally, the QMP should include additional items:
Stakeholder Engagement: It is crucial for the QMP to be a success. They should be involved in planning, design, development and implementation of the QMP.
Project Initiation. It is important to understand the problem and the solution in order to initiate any project. The initiator must know the reason they are doing something and the expected outcome.
Time Frame: This is a critical aspect of the QMP. The simplest version can be used if the QMP is only being implemented for a short time. If you are looking for a longer-term commitment, however, you might need more complex versions.
Cost Estimation. Cost estimation is another crucial component of QMP. You can't plan without knowing how much money it will cost. Cost estimation is crucial before you begin the QMP.
QMPs are not just a written document. They should be a living document. It evolves as the company grows and changes. It is important to review it periodically to ensure it meets all current requirements.